印刷済みキャリアフィルムのリサイクルの課題と取り組み内容について
当社はこれまで印刷済みキャリアフィルムのマテリアルリサイクル手法の開発と、リサイクル樹脂活用の可能性を模索すべく、さまざまな取り組みを行ってきました。マテリアルリサイクルの取り組み第一弾では3D プリンタを用いて、第二弾では小型射出成形機を用いて、リサイクル樹脂の成形に挑みました。
第三弾となる今回は、当社の最も得意とする技術である「成形同時加飾技術IMD(In – mold Decoration)」の成形材料としてリサイクル樹脂を活用した取り組みについてご紹介します。
キャリアフィルムは転写工法において必ず使用されるPETフィルムであり、一度使用するとそのまま廃棄されることが一般的です。当社の転写工法「IMD」においても、印刷済みのフィルムが廃棄されています。それらをマテリアルリサイクルすることで再利用したいと考えているものの、PET以外の不純物(インクなど)が混ざっているため、そのままではリサイクルが難しい状況でした。
そこで今回、リサイクル材料をペレット化するための条件検証はもちろんのこと、成形条件の調整や別素材を少量混合(ドライブレンド)する手法を開発することにより、当社の得意とするIMDに適用できるマテリアルリサイクルを実現しました。
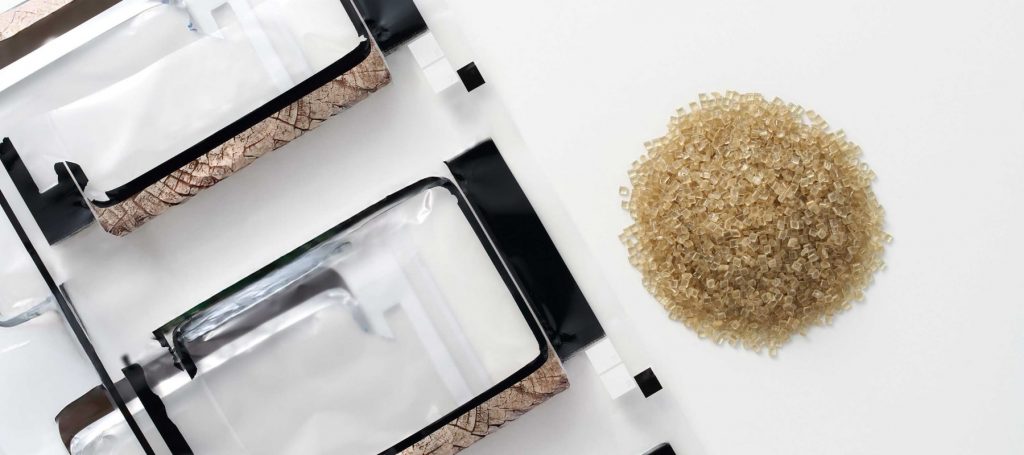
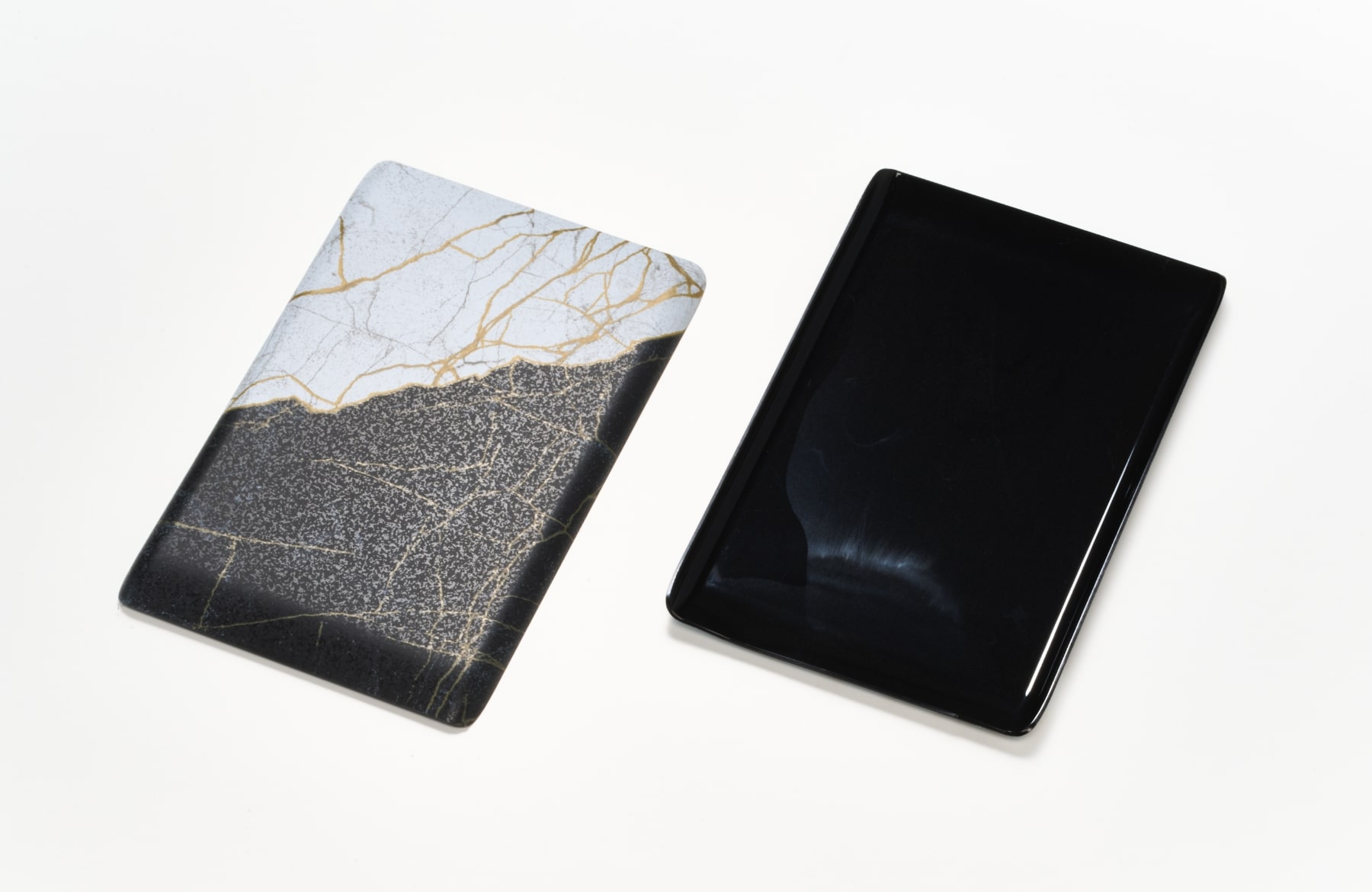
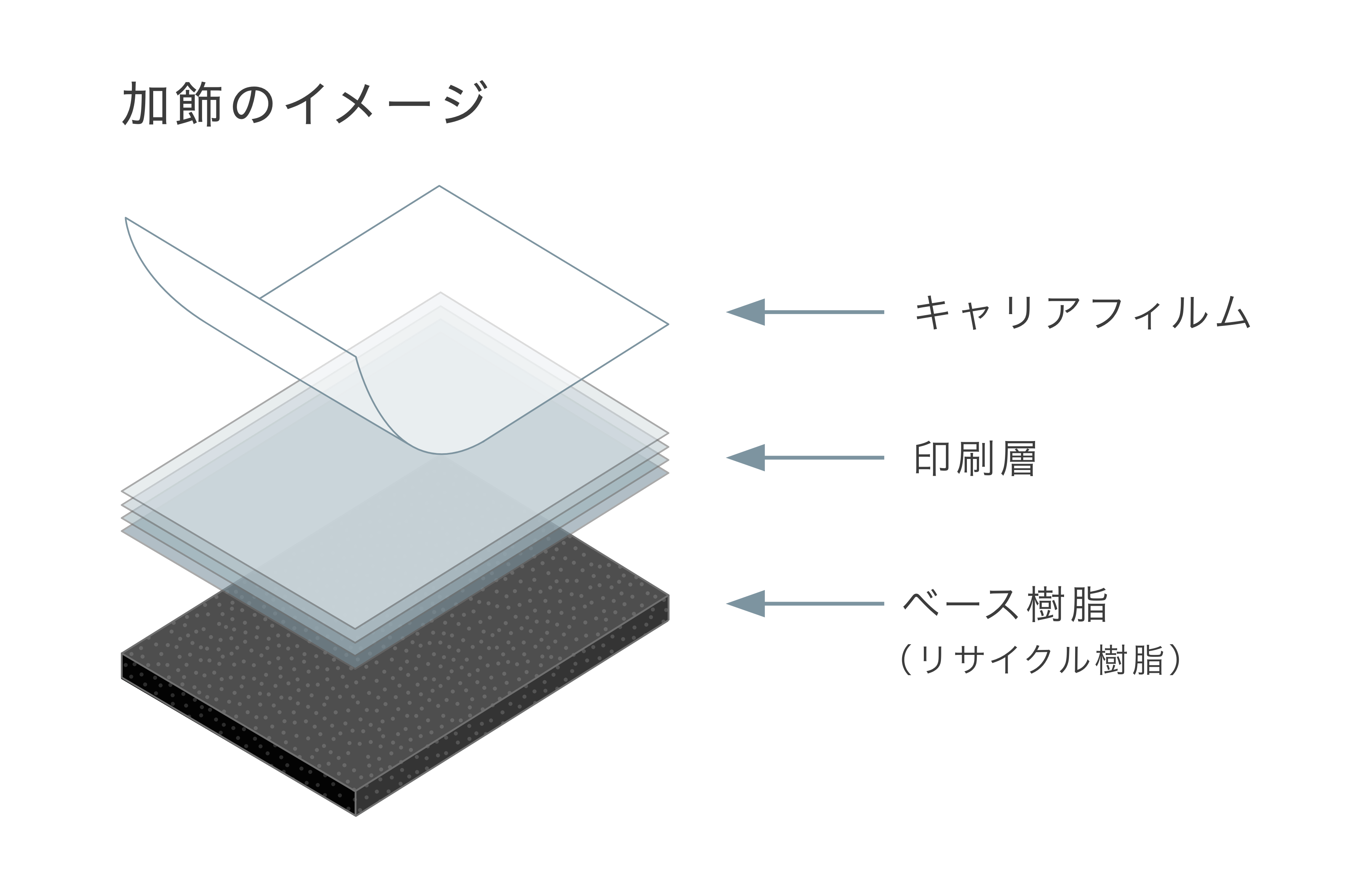
キャリアフィルムリサイクル × IMDによる表面加飾
当社のIMDは、3D形状のプラスチックを射出成形すると同時に、その成形品表面にキャリアフィルムに印刷された意匠を転写する技術です。このプロセスの強みは、加飾フィルムによる多彩な意匠表現が可能でありながら工程がシンプルで、連続成形による高い生産性をもつ点にあります。安定した品質を実現するためには、ベース樹脂の成形のしやすさや加飾フィルムとの相性が非常に大切となります。
今回、リサイクルPET樹脂で射出成形をするにあたり一番課題となった点は、樹脂の流れが良くないために射出が安定しないことでした。特に、成形機のノズル先端で詰まりやすく連続成形ができないため、安定した生産が非常に難しい状況でした。
課題解決のためには、成形するリサイクル樹脂の特性を変化させる必要があったため、異なるマテリアルリサイクル材とのブレンドを考えました。そこで当社の異なる工法に注目しました。別工法では印刷したフィルムが製品に残り、プラスチック射出成形品と一体化されます。その後の加工工程でトリミングされた不要部分が、廃棄物として発生します。この廃棄された部分をペレット化し、リサイクルABSペレットとして利用する方法を試みました。 このリサイクルABSペレットをリサイクルPETペレットに少量混合(ドライブレンド)して射出成形を行うことで、安定した成形が可能になるということが分かりました。
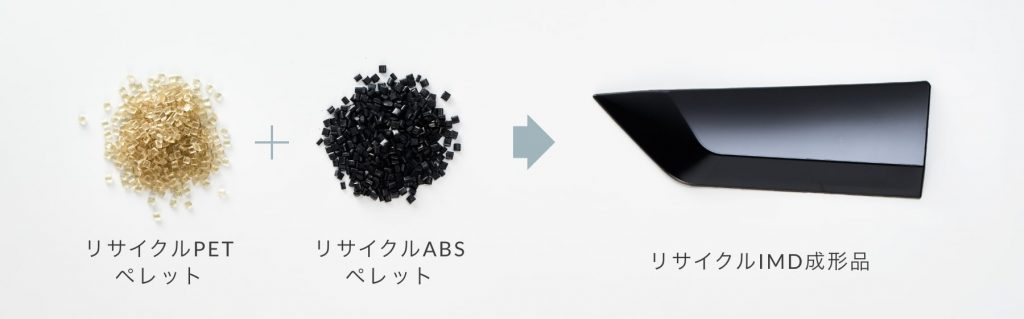
こうすることで、このブレンドしたリサイクル樹脂を使用し、加飾フィルムを用いたIMD工法に適合できました。通常、リサイクル樹脂を使用した成形品は、バージン樹脂で成形したものと比べて均質化が難しく、特に外観面でのばらつきやむらが出やすい傾向があります。しかし、今回の取り組みのように加飾フィルムを活用することで、金属調や木目調などの意匠を組み合わせることが可能になりました。技術的なリサイクル手法開発にとどまらず、 リサイクル製品とは思えない付加価値の高い製品へと昇華させることで、再生材料の活用の幅を広げる足掛かりとなると考えています。
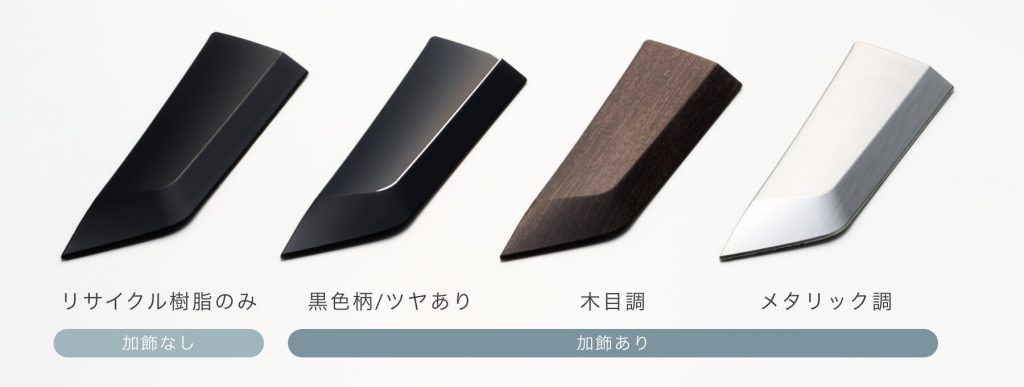
持続可能な製造プロセスを目指して
使用済みキャリアフィルムのマテリアルリサイクルに関する取り組みの第三弾として、当社の得意とするIMDの成形材料としてリサイクル樹脂を活用した取り組みをご紹介いたしました。
今回の試みにより、転写工法の成形時に一度使用したキャリアフィルムをペレット化し、成形樹脂として活用することで材料を無駄なく使用することが可能となりました。このようなPETフィルムのリサイクル、つまり製品製造における廃棄物の削減と再活用に向けての取り組みは、当社が力を入れているサステナビリティ対応のひとつです。
当社は今後も、多角的な視点から環境配慮に向けたアプローチを継続的に推進していきます。
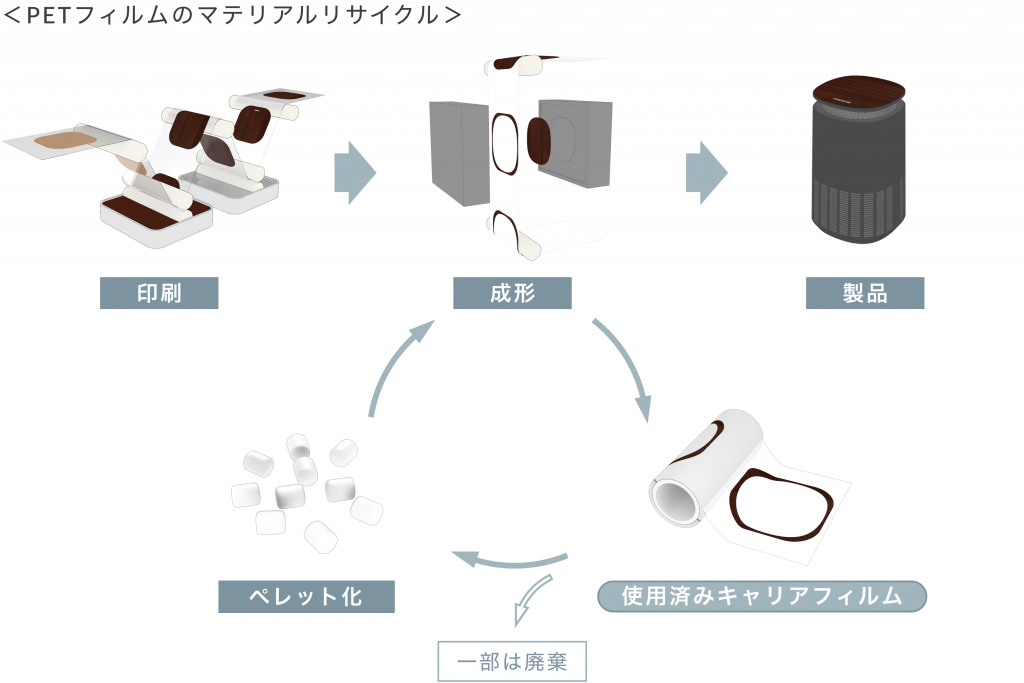
今回の取り組みで製作した成形品は、「CMF DESIGN 2024」にも掲載しています。
※本稿でご紹介している内容は、マテリアルリサイクルの実施に向けた試験的な取り組みです。