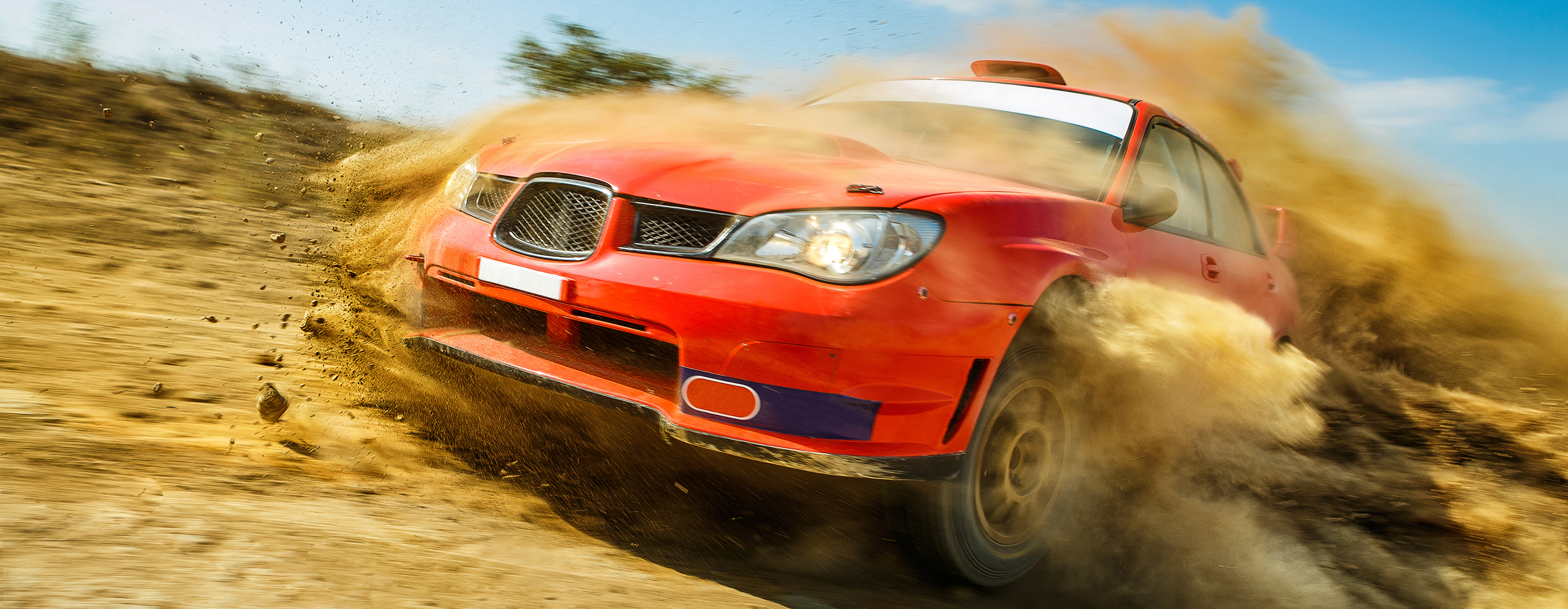
Chipping resistance
Film insert molded products for Automotive exterior components
Film insert molding delivers chipping resistance at required level for automotive exterior decorative components without painting
What is chipping-resistance testing?
Chipping-resistance testing is endurance testing for evaluating levels of damage that molded-product surfaces sustain from impacts by stones, gravel, and so on. It is also referred to by names such as gravelometer testing and stone-impact testing.
A molded product is mounted on a testing stand, and gravel is sprayed onto the surface of the product at a fixed pressure. Following this, the degree of deterioration of the surface is evaluated.
In the case of the chipping-resistance testing of automotive components, there are testing standards that include JASO M104, SAE J400, ISO 20567-1 Test Method B, and ASTM D3170-3.
Paintless components that have outstanding chipping resistance
Film insert molding is a method in which design films are preformed, and then undergo integral molding by loading them into an injection mold.
Molded-product surfaces are protected by acrylic transparent films. Therefore, overcoating treatment is not carried out.
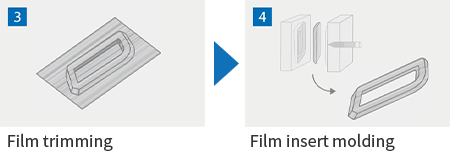
General acrylic films do to the meet the requirements of chipping-resistance testing at the level for painted components.
Thus, we at Nissha specially process the surfaces of top-layer acrylic films, and have thereby realized surface-protection films with outstanding chipping resistance.
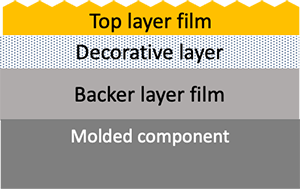
Chipping-resistance specifications of Nissha film-insert-molded products
Test standard: SAE J400
Testing conditions
Test angle: 90°
Spray pressure: 70 psi
Spray volume: 1.4 L
Test-environment conditions:
-20℃ ± 2℃, room temperature
Achievement of durability at level
required for application of product
as automotive exterior component
We have also met the required specifications for automotive exterior products in areas of durability testing other than chipping resistance, such as heat resistance and weather resistance.
Feel free to contact us
Benefits of film insert molded products
Manufacturing process with low environmental impact
Film insert molding is a method in which decorating is carried out at the same time as injection molding. The manufacturing process is extremely simple, and this is partly because no drying processes are required. As a result, CO2 emissions from the fabrication process are about 50% less compared with those from exterior-resin decoration through painting.
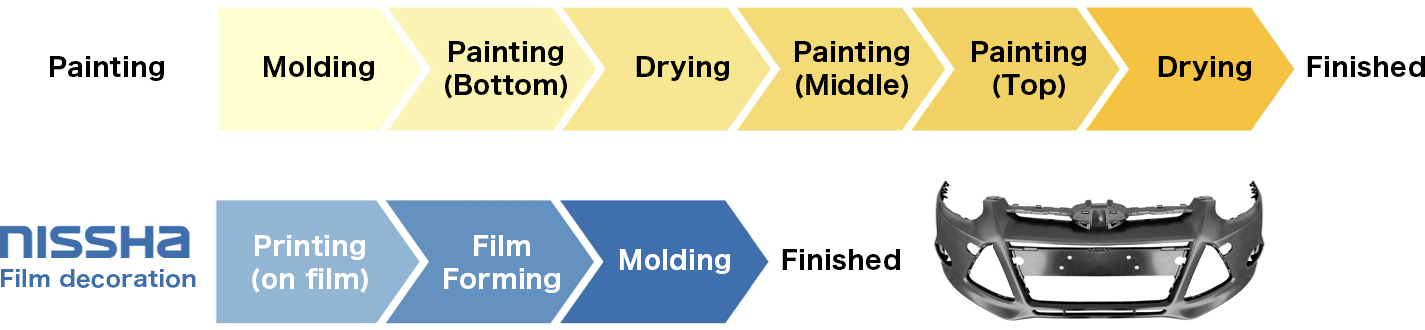
Realization of diverse designs
Various designs can be realized that cannot be achieved through painting.
The possible designs include metallic finishes, carbon-fiber patterns, and geometric designs, and furthermore, on the back surface of molded products, it is possible to achieve hidden-lit designs that incorporate LED light sources.
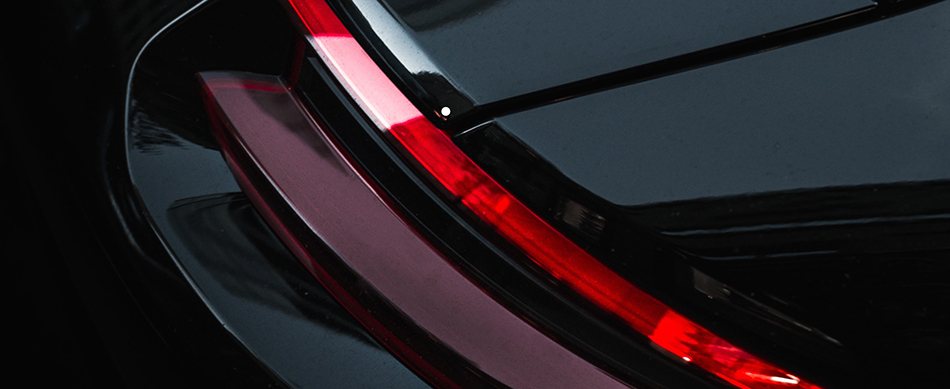
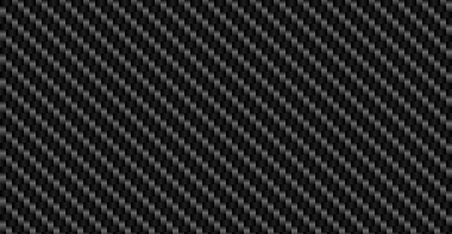
Carbon pattern
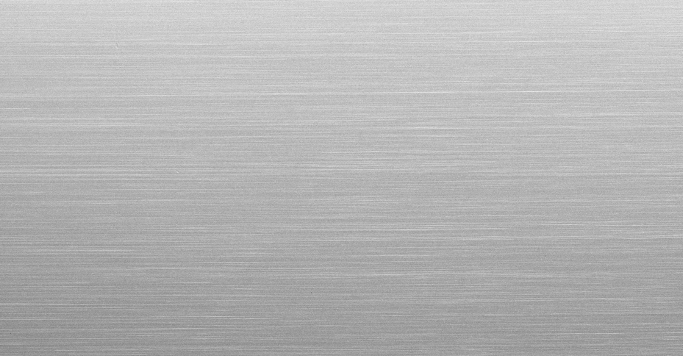
Hair line
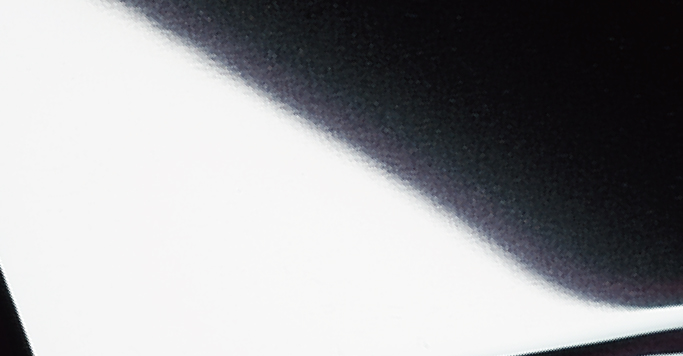
Metallic color
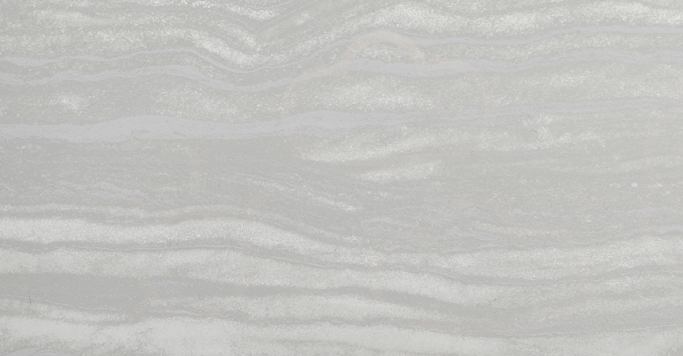
Abstract pattern
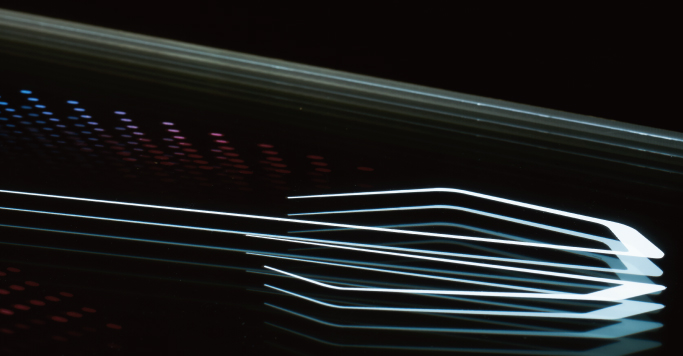
translucent light emittion
(Dead front)
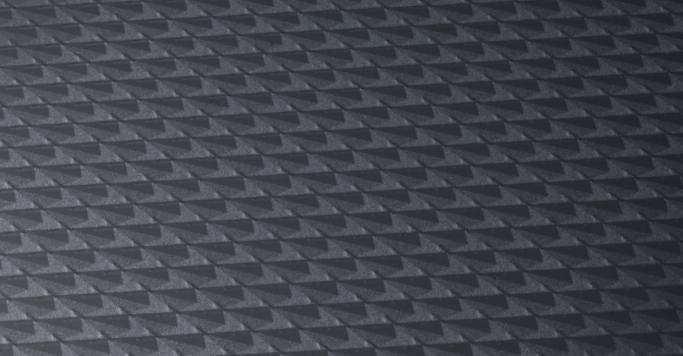
Geometric pattern
Contract manufacturing of decorative molded products for automotive exteriors.
Business models with supply chain
Film roll delivery
Film roll delivery is possible for those who mold it in house
Molded parts delivery
We can supply molded parts from Nissha’s global factories.
We can process molding at your preferred location worldwide.
We can provide service that starts with addressing customer’s questions and concerns
We are able to accommodate requests that include:
• Requests to just see films
• Requests to view molding samples
• Requests to receive prototypes for the presentation of drawings
We would like to encourage customers to first of all consult us.
Feel free to contact us