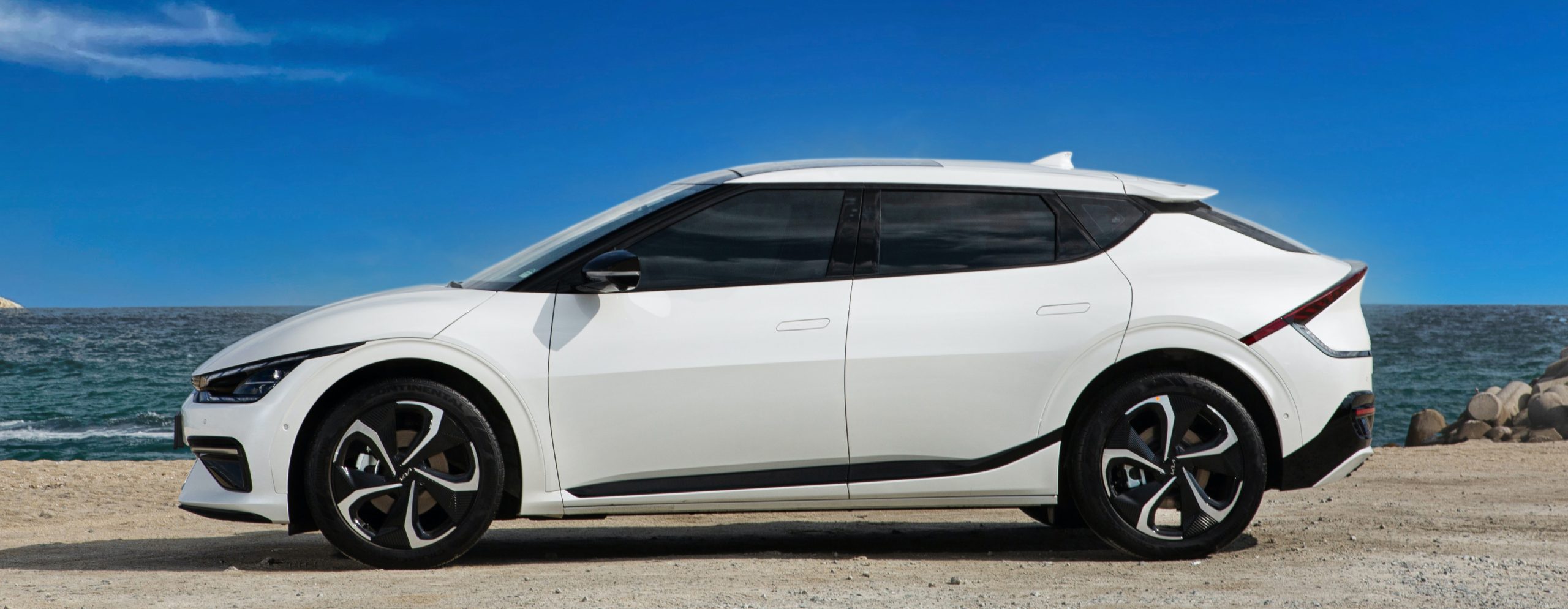
Film insert molding
Contract manufacturing of automotive exterior components
Low environmental impact
Chipping resistance
equivalent to that of painted productsDiverse designs
Incorporation of functional components
such as heaters
Contract manufacturing for decorative plastic molded products for automotive exteriors
skid plates, pillars, EV front grilles, and more
Benefits of film insert molding
for automotive exterior components
Manufacturing process with low environmental impact
Film insert molding is a method in which decorating is carried out at the same time as injection molding. The manufacturing process is extremely simple, and this is partly because no drying processes are required. As a result, CO2 emissions from the fabrication process are about 50% less compared with those from exterior-resin decoration through painting.
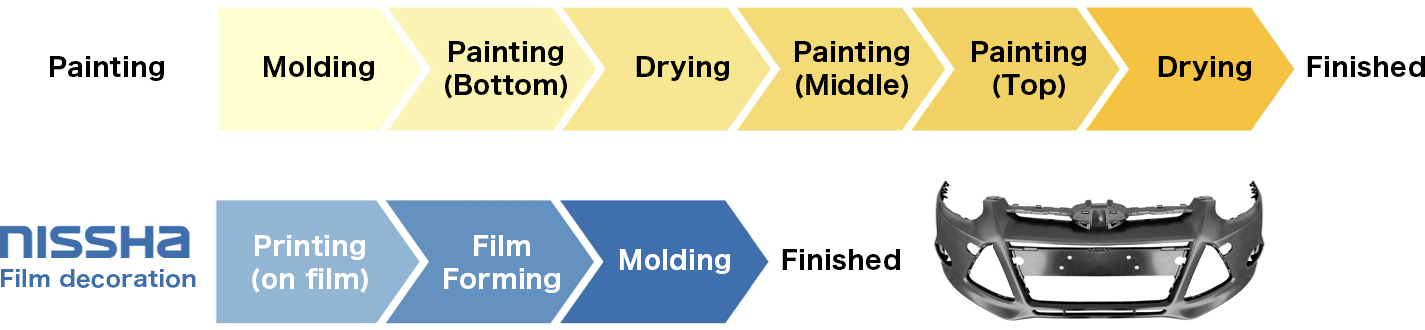
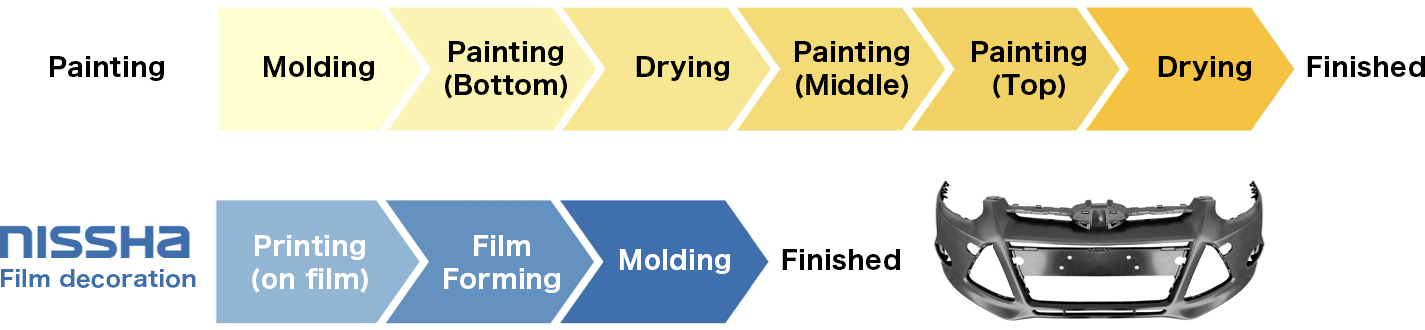
Realization of diverse designs
Various designs can be realized that cannot be achieved through painting.
The possible designs include metallic finishes, carbon-fiber patterns, and geometric designs, and furthermore, on the back surface of molded products, it is possible to achieve hidden-til-lit designs that incorporate LED light sources.
Through our in-house CMF Design Team, we at Nissha propose high-quality designs while listening to the requests of customers. We ask for customers to first of all let us know what they would like to do.
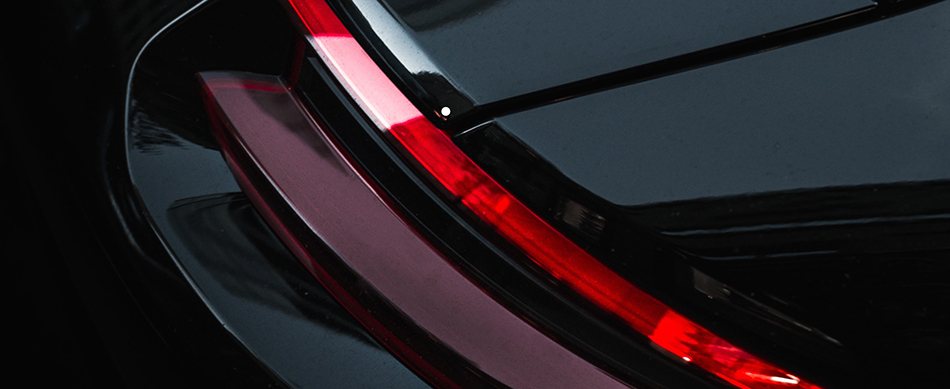
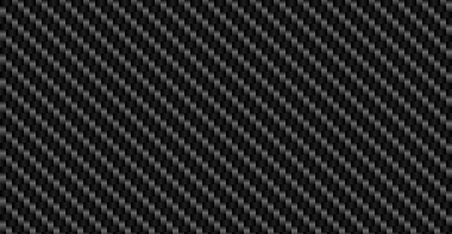
Carbon pattern
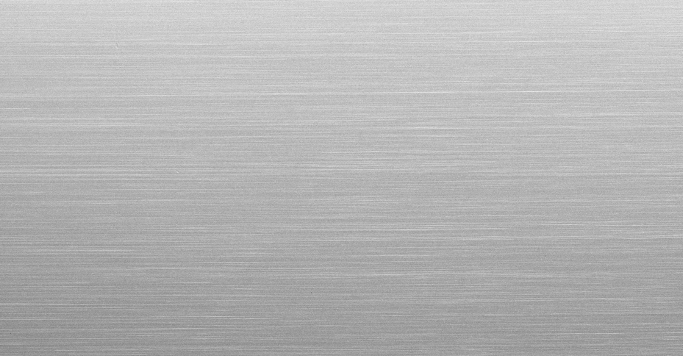
Hair line
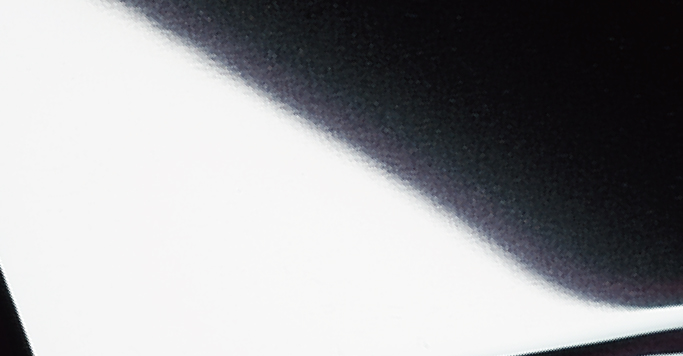
Metallic color
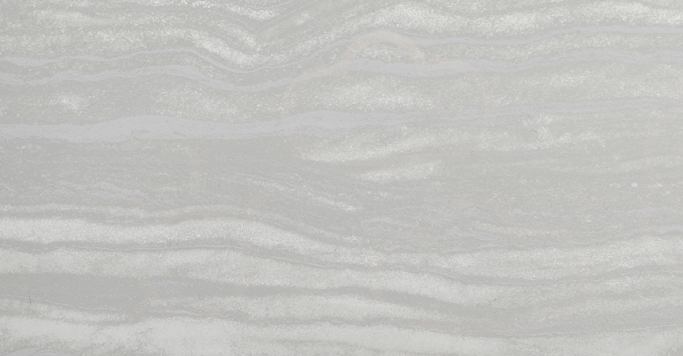
Abstract pattern
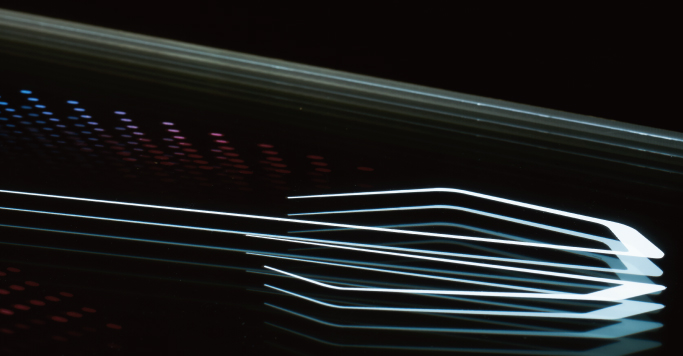
Translucent light emittion
(Dead front)
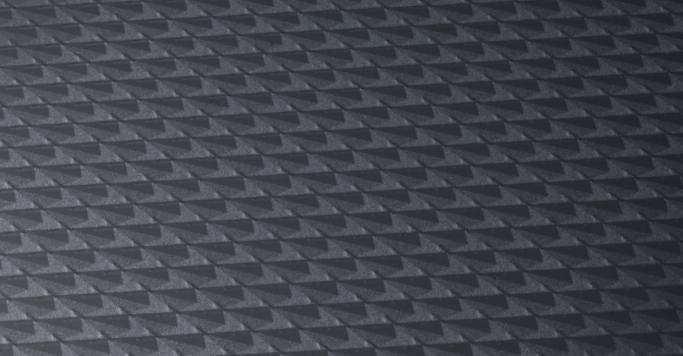
Geometric pattern
Durability equivalent to that of painted products
For the top layer, we use acrylic films that have been specially processed to give them outstanding chipping resistance. Furthermore, the products meet all of the durability specifications that are required for exterior components with regard to resistance to weather, chemicals, and so on.
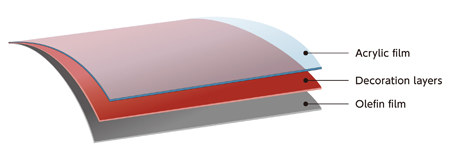
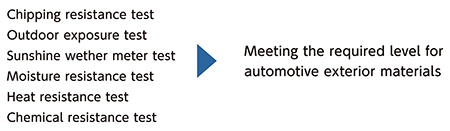
Incorporation of functional components such as heaters
We have also developed technologies that enable the incorporation of electronic components into plastic molded products.
We offer manufacturing technologies that contribute to ADAS development, and these include technologies for embedding wire heaters into molded products, and ones for incorporating LED into molded products.
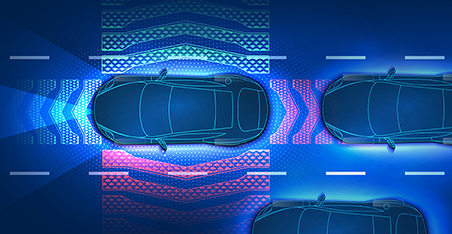
Radio-wave transparency
Learn more >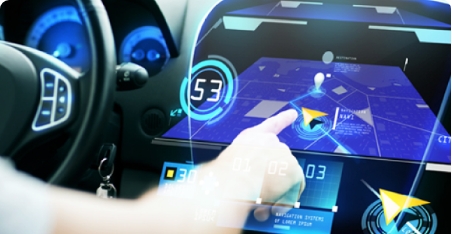
Touch screen
embedding
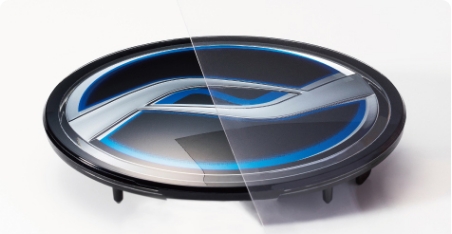
Heater embedding
Learn more >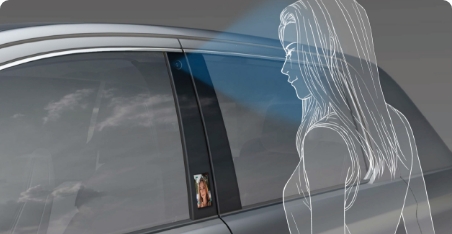
IR-wave transparency
Large-scale plastic molding
We possess molding machines that range up to the 850-ton class.
We can accommodate the film insert molding of large exterior components, including bumper guards, door trims, and pillars.
Feel free to contact us
Example of adoption
Front panel with wire heater for electric vehicle (EV)
This is a front panel with an embedded wire heater for preventing snow accretion on the vehicle’s LiDAR sensor surface. The structure of the heater has been designed while taking into consideration radio-wave transparency so that sensor performance is not affected.

Embedded heater on Backside of the molded panel
Other envisioned applications
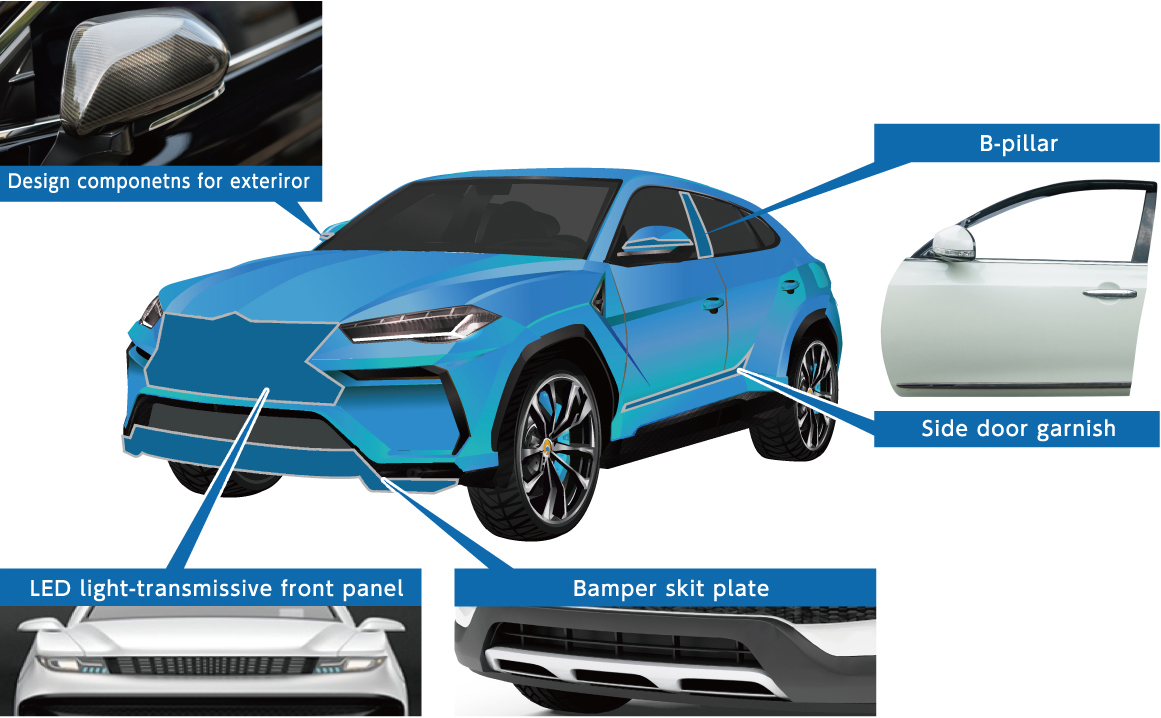
Feel free to contact us
Technical information
regarding film insert molding
Fabrication process
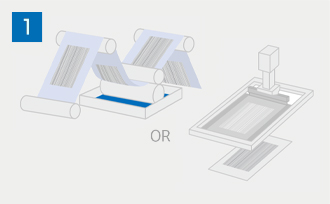
Printing
We are able to accommodate the process starting from the printing of decorative films.
Using multicolor gravure printing machines, we can create not only monochrome expressions, but also a diverse range of patterns that are achieved through the overprinting of various inks.
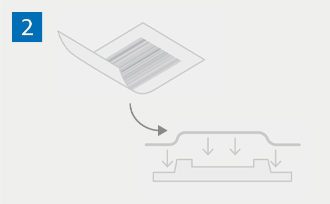
Film preforming
The films that have undergone printing are preformed through pressure forming.
For the decorative films, olefin or acrylic films, which have outstanding stretchability, are used. This is to enable the films to be used for the deep shapes of items such as bumper guards and center-cap ornaments.
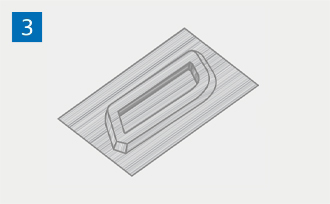
Film trimming
Following the preforming, the unnecessary portions of the film are trimmed in accordance with the size of the molded product, using a Thomson cutter or laser processing machine.
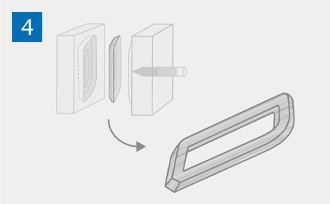
Film insert molding
The trimmed film is inserted into a mold, and insert molding is carried out.
During this process, the film is integrated with olefin resin, which is frequently used for exterior components, through the thermal pressure of injection molding.
We possess an integrated mass-production process that ranges from film printing in Japan to insert molding overseas. As a result of this, we are able to supply insert-molded products globally.
Also, we can accommodate supplying just films to a designated molding factory according to customers’ requests.
Film composition
Top layer
This consists of acrylic films that meet the specifications for exteriors.
Decorative layer
For this, we can create diverse designs through gravure printing, screen printing, vapor deposition processing, and so on. We are able to propose designs in accordance with the requests of customers, and these include carbon fiber patterns, hairline finishes, and metallic finishes.
Backer layer
This consists of olefin films that are focused on adhesiveness with molding resins.
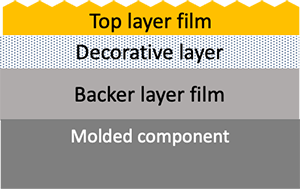
Molding resins
We can accommodate general molding resins that are used for exterior components, such as TPO and PP.
Business models with supply chain
Film roll delivery
Film roll delivery is possible for those who mold it in house
Molded parts delivery
We can supply molded parts from Nissha’s global factories.
We can process molding at your preferred location worldwide.
Molding plants by regions


Nissha has molding bases around the world, allowing production to provide parts near our customer.
We can provide service that starts with addressing customer’s questions and concerns
We are able to accommodate requests that include:
• Requests to just see films
• Requests to view molding sample
• Requests to receive prototypes for the presentation of drawings
We would like to encourage customers to first of all consult us.
Feel free to contact us