Blog
A Brief History of Biodegradable Plastics – with an itemized timeline
2023/11/16
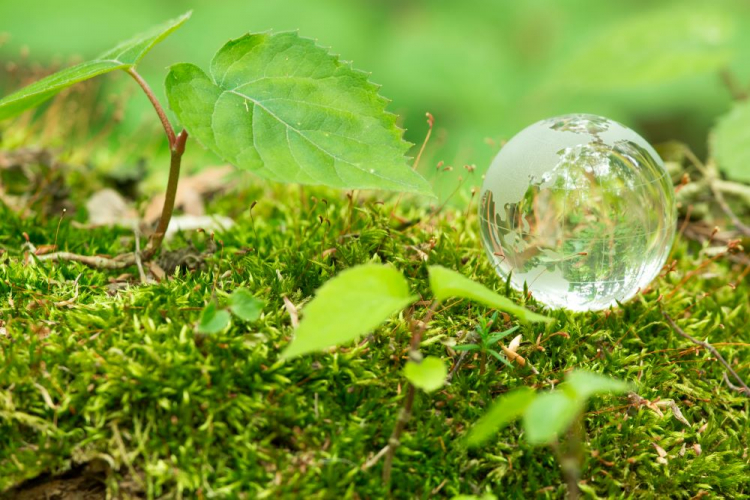
Plastic pollution becomes increasingly serious problem. Approx. 8million tons of plastic get dumped into the ocean, every year. Plastic waste causes immeasurable impact on marine life.
While the world faces environmental problems, biodegradable plastic is expected to be one of the solutions to address the challenges. The material was discovered in the 1920s and have been developed further in response to worsening the problem, and development continues to evolve with the aim of achieving both biodegradability and durability.
In this article, we show the history of biodegradable plastic development. Towards the end of the article, you will also find a development history of major materials. We hope you have better understanding the characteristics of the materials.
About Biodegradable plastic
Japan Bioplastics Association introduces “Biodegradable plastic” is a type of plastic that can be used like conventional plastic and, after use, is broken down in the natural environment by the action of microorganisms, ultimately decomposing into water and carbon dioxide, returning to the natural environment.
In addition, there is the term ‘biomass plastic,’ which refers to plastic materials made from plant-based resources, and it includes materials like bio polyethylene that do not necessarily possess biodegradable properties.
How it breaks down
Biodegradable plastics break down when placed in natural environments where microorganisms are actively present, such as in soil or water, or in controlled environments like composting facilities. The rate of decomposition can vary depending on the specific material. Among common biodegradable plastics, Polyhydroxy butyrate/ Hydroxy hexanoate (PHBH) can decompose in soil, water, and composting environments. Polybutylene Succinate (PBS), on the other hand, decomposes in soil and composting conditions, while Polylactic Acid (PLA) requires a composting environment for degradation. In the case of PLA, data suggests that it can start to break down within about one week after being introduced into a composting system.
How it is used
Biodegradable plastics are currently widely used in consumer goods related to the food industry, such as packaging materials, checkout bags, and disposable tableware. One of their advantages is that they can be composted when disposed of with organic waste. Additionally, their ability to eventually break down and be excreted after a certain period of residence in the body has led to their use in medical devices like surgical sutures, taking advantage of their characteristics in the healthcare industry.
Future developments
In the future, developments in biodegradable plastics are likely to focus on enhancing their performance, versatility, and sustainability. Researchers and manufacturers are working to improve the mechanical and thermal properties of these plastics, making them more suitable for a wider range of applications. While biodegradability is required in certain applications, there is also a need to ensure durability, especially in products like electronic components where rapid decomposition is not desirable.
Nowadays, the issue of marine plastic pollution has brought significant attention to the development of materials with high underwater biodegradability.
History of Biodegradable Plastics
P(3HB)
In 1920, “P(3HB),” an organic polymer with biodegradable properties, was discovered. Polyhydroxybutyrate (P(3HB)) is a biodegradable plastic that is produced inside microorganisms in a process known as the “microbial biosynthesis pathway.” The discovery of P(3HB) is credited to researcher Lemoigne at the Pasteur Institute in France, a renowned institution for microbiological research. P(3HB) belongs to the family of aliphatic polyesters and serves as an energy storage material accumulated within the cells of microorganisms, particularly a bacterium called ” Bacillus megaterium.” This discovery marked the beginning of the history of biodegradable plastics.
“P(3HB)” is structurally a brittle material, and its melting point (the temperature at which the material melts into a liquid) and thermal decomposition temperature (the temperature at which the material degrades, resulting in weight loss) are too close, making it unsuitable for use as a molding material. After Lemoigne’s initial discovery, research on P(3HB) did not progress significantly for some time.
However, in 1958, William Williamson discovered a method for mass-producing P(3HB) through fermentation using microorganisms. This breakthrough accelerated research and development efforts related to P(3HB).
Mass production of P(3HB,HV)
In 1980, the UK-based company ICI succeeded in mass-producing a material called P(3HB/3HV) by copolymerizing polyhydroxybutyrate (P(3HB)) with poly-3-hydroxyvalerate (P(3HV)). This development allowed ICI to advance its research in polyhydroxybutyrate-based materials. By the early 1990s, they had successfully commercialized these materials, using them for products such as shampoo bottles. However, due to their inferior physical properties compared to conventional plastics and the high manufacturing costs involved, ICI decided to sell its polyhydroxybutyrate-based materials business to other companies.
Today, this business is continued by BASF, a prominent chemical company. Polyhydroxybutyrate, known for its biocompatibility, is utilized in various medical applications, including surgical sutures and other medical supplies.
“PLA”, most common material in biodegradable plastic
The successful synthesis of polylactic acid (PLA)
Currently, one of the most popular and actively developed biodegradable plastics is polylactic acid (PLA), which belongs to the category of chemically synthesized plastics. PLA has gained significant attention as an alternative material to polyester, such as in PET bottle manufacturing, and its development has expanded to various applications, including shopping bags, tableware, and enclosure parts for electronic appliances.
The existence of polylactic acid has been known for some time. The development of PLA took a significant step forward with the successful synthesis of low molecular weight polylactic acid by W.H. Carothers, a researcher at Dupont, in 1932. This breakthrough marked the beginning of PLA’s development. However, early versions of PLA had poor durability and were unsuitable for industrial applications.
1990s to Present: The Surging Development Rush of Polylactic Acid (PLA)
After Carothers’ successful synthesis in 1932, polylactic acid (PLA), which had poor durability, remained relatively obscure, and research progress was limited. With the end of World War II and the onset of the era of mass production, the world shifted its focus towards the development of plastics that could ‘persist’ without breaking down. There was little interest in PLA, which degraded and ‘disappeared.’
However, in the 1990s, the situation underwent a significant transformation. Amidst rapid economic growth, the disposal of large quantities of plastic products became a pressing social issue. The world began to seek plastic materials with low environmental impact that could be safely disposed of. Polylactic acid (PLA) came into the spotlight. This marked the beginning of a development rush for PLA.
The development of polylactic acid (PLA) was primarily driven by companies in Japan and the United States.
It all began with the launch of polylactic acid (PLA) material sales by Showa Denko in 1993, and during the 1990s, various companies including Cargill, Shimadzu Corporation, Kanebo, and Mitsui Chemicals established large-scale PLA production plants. Material development became more active, leading to improvements in PLA durability. Various methods for enhancing heat resistance and impact resistance, such as promoting crystallization through annealing during molding or incorporating inorganic fillers, were introduced.
Furthermore, in 2001, a joint venture between Cargill and Mitsui Chemicals led to the establishment of NatureWorks, a prominent brand representing polylactic acid (PLA). Beyond 2002, various large corporations and startups continued their efforts in the development of PLA.
Today, polylactic acid (PLA) finds wide applications, primarily as the material for disposable products like shopping bags and beverage bottles.
The history of biodegradable plastics is also the history of ‘surgical sutures’.
The fact that they are biodegradable means that they are absorbed and broken down inside the body. Leveraging this feature, biodegradable plastics are used as sutures for closing organs or skin within the body after surgical incisions. Biodegradable sutures serve the role of sealing the incision site and are naturally absorbed by the body after fulfilling their function.
The history of sutures themselves is quite ancient, dating back to records from ancient Egypt. In the past, sutures were made from plant fibers. The use of silk thread for sutures became more widespread with time. Simultaneously, sutures made from materials that could be absorbed by the body were also employed. These were known as “catgut” sutures and were made from the membrane of sheep or cattle intestines. Catgut had the property of being absorbed by the body but posed quality and infection risks. To address these issues, biodegradable plastic sutures were developed.
Around the 1970s, the development of sutures made from polyglycolic acid marked the beginning of the history of synthetic polymer sutures. In Japan, in 1986, Gunze started selling sutures made from polyglycolic acid. Subsequently, the development of biodegradable sutures, such as those made from polylactic acid and polycaprolactone, progressed. Today, biodegradable plastic sutures have taken the place of catgut as absorbable sutures in medical practice, playing a vital role in the field of healthcare.
Other biodegradable plastics
Chitin and chitosan
derived from the shells of crustaceans such as crabs and shrimp, are biodegradable plastics belonging to the polysaccharide family. They were discovered in the 1800s and have seen accelerated development since the 1970s. Currently, they are primarily used in medical applications, such as artificial skin.
Polycaprolactone
is a chemically synthesized biodegradable plastic that is derived from petroleum-based materials, without the use of biomass feedstock. In the 1970s, bacteria capable of breaking down polycaprolactone were discovered, initiating the development of this material as a biodegradable substance. As mentioned in the explanation about sutures, polycaprolactone is primarily utilized as a fiber material.
Timeline of the Development of Biodegradable Plastics
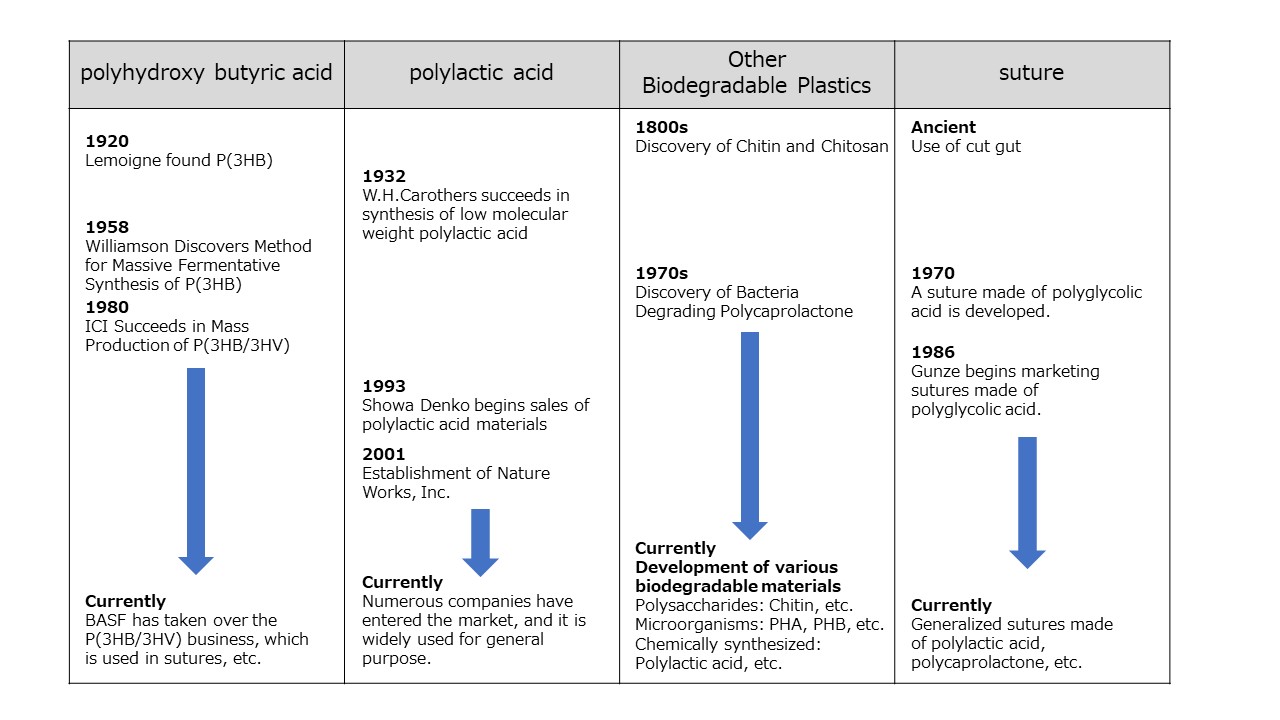
Summary
we have been looking at the history of the development of biodegradable plastics.
As mentioned earlier, the development of biodegradable plastics means the development of trade-off relationship between “disappearing” and “continuing to exist”. And the challenge to control these two properties is ongoing.
Furthermore, the characteristics of how biodegradation progresses vary significantly depending on the material, such as in what type of environment it breaks down. For products of concern in marine waste, materials with excellent underwater biodegradability are chosen. In the case of medical devices, materials that biodegrade inside living organisms are used. On the other hand, for products where durability is required, materials that only break down in composting environments are selected. To choose the right material that suits the purpose and application, it’s crucial to understand these specific characteristics. I would be very pleased if this article helps deepen your understanding of biodegradable plastics.
What is NISSHA?
NISSHA is an expert company in molding and processing. We offer an eco-friendly molded products alternative to plastic as “ecosense molding”.
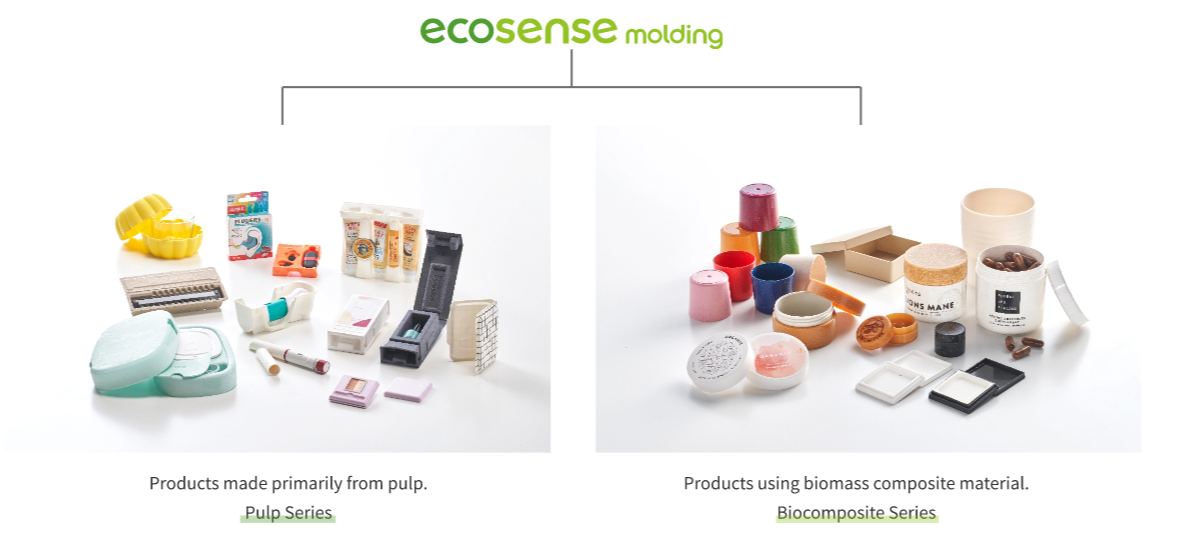
Products
- Pulp Series
- Molding technologies that use pulp, the raw material of paper, to create three-dimensional and highly designed containers or molded parts while retaining the texture of paper.
Learn more about Pulp Series - Biocomposite Series – Sulapac®
- Sulapac® is a material composed of wood chips and plant-based binders. It offers a unique design that allows you to experience the feel of wood while contributing to environmental pollution reduction through its microplastic-free properties. We have formed a strategic partnership with Sulapac, the company responsible for developing and producing this material, and we manufacture and sell it through our molding facilities on a global scale.
Learn more about Sulapac