Blog
【Design Point Explanation】Hanging Package of Pulp Mold | Realizing Free and Complex Shapes with Paper
2024/04/12
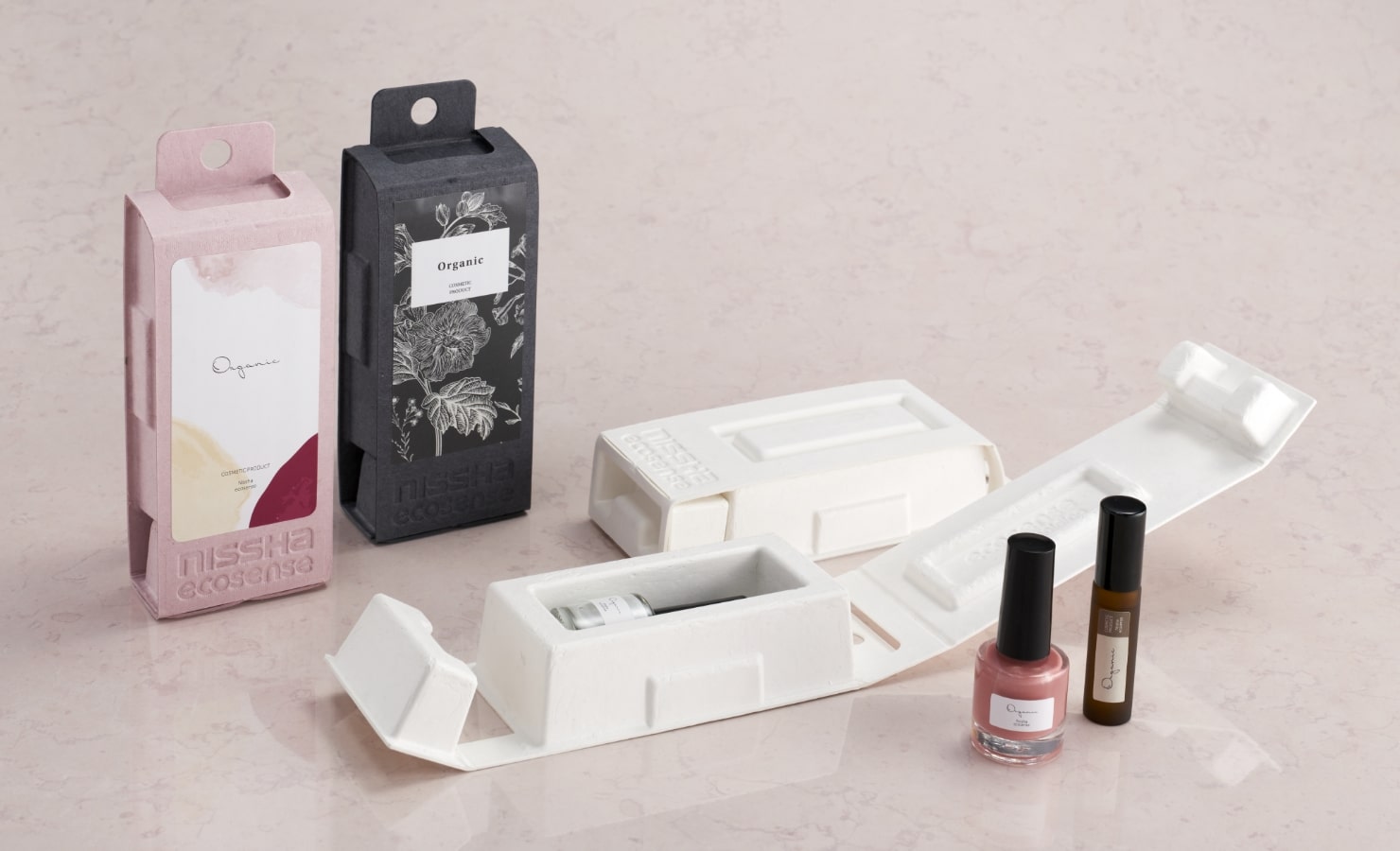
This blog is the first in the 【Design Point Explanation】 series, which explains design examples and ingenious points during the design of sustainable packaging and packing materials.
This time, using the “SoftLock® Box ” (patent pending), a hanging package designed by NISSHA that takes advantage of the features of Pulp-Molding , we will explain in detail its appearance and functions. The SoftLock® Box is a package for small items where the tray and cosmetic box are integrated and can be used for a wide range of applications, including cosmetics.
Introduction
About Pulp Molding
Pulp molding is a method of forming a 3D shape by dissolving pulp in water and adhering the raw material to a metal mold using the same principle as papermaking. Materials used include wastepaper such as old newspapers and cardboard, wood pulp, bamboo fiber, sugar cane fiber, and other fibrous materials (pulp). Therefore, it can give shape while retaining the texture of the paper itself.
Our company handles two types of pulp molds, dry pulp molding and wet pulp molding.
Dry Pulp Molding Forming Process
Wet Pulp Molding Forming Process
Features of Pulp Molding
A characteristic of pulp molding is its ability to reproduce curved shapes that are difficult to achieve with paper containers. It is often used for packaging materials such as trays and cushioning materials, and by shaping it to follow the outer shape of the contents, it can minimize movement during transportation. By increasing the thickness, it is also possible to enhance its cushioning properties.
In addition, the main ingredient of pulp mold is paper, primarily made from wastepaper such as cardboard and copy paper, and fibers from renewable sources like bamboo and sugarcane. This makes it environmentally friendly, and after use, it can be recycled as paper*.
Pulp molding, which does not use plastic and can contribute to reducing CO2 emissions, is gaining attention as an alternative to trays, blister packs, and Styrofoam.
*Differences may exist depending on the country or region.
Explanation of Design Points for the Hanging Package “SoftLock® Box ”
Here, we will explain the design points of the hanging package “SoftLock® Box ” (patent pending), which is made with Pulp-Molding(dry pulp molding) divided into functional and appearance aspects.
Design Points of the SoftLock® Box
Functional Aspect
Structure to protect contents from external impacts
The area where the product is stored is designed to be one size smaller than the outer shape, creating a U-shaped wall. This U-shaped wall acts as a cushion to protect the contents from external shocks.
While the area where the product is stored can be freely designed according to the shape and size of the contents, in the SoftLock® Box , considering its versatility, we set the rectangular storage compartment to (width 25mm x length 70mm × height 25mm).
Easy-to-open unique snap structure (patent pending)
In pulp molding, it is difficult to reproduce a fastening structure that utilizes protrusions such as hooks, like in plastic injection molding, because undercuts cannot be formed. However, the SoftLock® Box has achieved a solid sealing structure by fitting together the concave and convex shapes of the lid side and the tray side.
Also, by setting a part to hook your finger, you can easily open the package without applying strong force.
By applying this sealing structure, it can adapt to packages of various variations such as spherical or hexagonal.
In addition, you can reproduce various forms of sealing structures as shown below.
High sealing lid
By firmly fitting the convex shape on the lid side and the concave shape on the body, the risk of foreign objects or debris entering the interior can be reduced. In addition, the convex shape on the lid side has the effect of fixing the contents so that they do not move up and down.
Shape to prevent biting during stacking
Until the contents are packed, packaging materials are often stacked (stacking) to store in the minimum space. At that time, the packages may bite into each other strongly due to their own weight and vibration, and when it comes to using them, the packages may not come apart. To avoid reducing work efficiency, the SoftLock® Box has a shape on its side to prevent biting.
Hanging tab
A tab shape is provided so that it can be hung on a display shelf in a store.
Appearance Aspect
Color Variations
It is possible to color by using dyes or craft paper. The combination of the texture of the paper and color variations results in a highly designed package that stands out and cannot be expressed with plastic.
Debossing
A concave stamping process can be applied to the surface of the molded product. It is often used for company names or brand names, and it gives a different impression from printed materials.
Ample display space
Packages require the display of a lot of information such as product name, description, and ingredient list. Traditional methods like showing the contents through the transparency of plastic trays, or combining with pre-printed backing paper are possible, but pulp molding, being a paper material, cannot use the same methods. Also, due to the characteristics of the method, the concave and convex shapes provided inside may affect the appearance, making it difficult to print on a flat surface.
For these reasons, in the SoftLock® Box , we believe it is appropriate to use label stickers and have provided ample display space to explain the product. In addition, by covering with a sticker, it is also possible to hide the concave shape, which leads to an improvement in design as a cosmetic box.
Uniform edge
After molding, the edge of the product is frayed with pulp fibers, so the periphery is punched out to make the edge uniform. This results in a finish that gives a high-quality impression while taking advantage of the texture of the paper.
Clean fold lines
Considering the ease of folding during packaging, normally, perforations are made in the folded part of the flap to prevent misalignment with the tray. However, perforations are noticeable because the cuts penetrate the molded product.
In the SoftLock® Box , which emphasizes design, instead of perforations, grooves for bending are put on the inside, so it becomes a clean fold line that is not noticeable when viewed from the outside. It is strong against repeated bending and has better durability compared to perforations.
Conclusion
- Pulp-Molding, while mainly made of paper, can reproduce curved shapes.
- By devising the design, it can accommodate not only trays and cushioning materials but also packages where the cosmetic box and tray are integrated.
- Ideal for replacing trays made from plastic such as vacuum forming and Styrofoam.
At NISSHA, we design according to customer’s requests. Please contact us for consultations about environmentally friendly packaging materials and packages.