Blog
[Explanation] Types and Features of Molded Pulp Technologies for Achieving Plastic-Free Packaging
2023/11/09

Introduction
In recent years, global efforts towards achieving Sustainable Development Goals (SDGs) have intensified, and the reduction of environmental impact has become more critical. Consequently, many companies are working on transitioning from plastic packaging to more sustainable alternatives. In this article, we will explain the types and features of molded pulp, which contribute to reducing plastic packaging.
What is Pulp?
Pulp refers to fibers extracted from plants. The primary raw materials for “paper,” which is abundant in our daily lives, are mainly recycled paper and wood pulp.
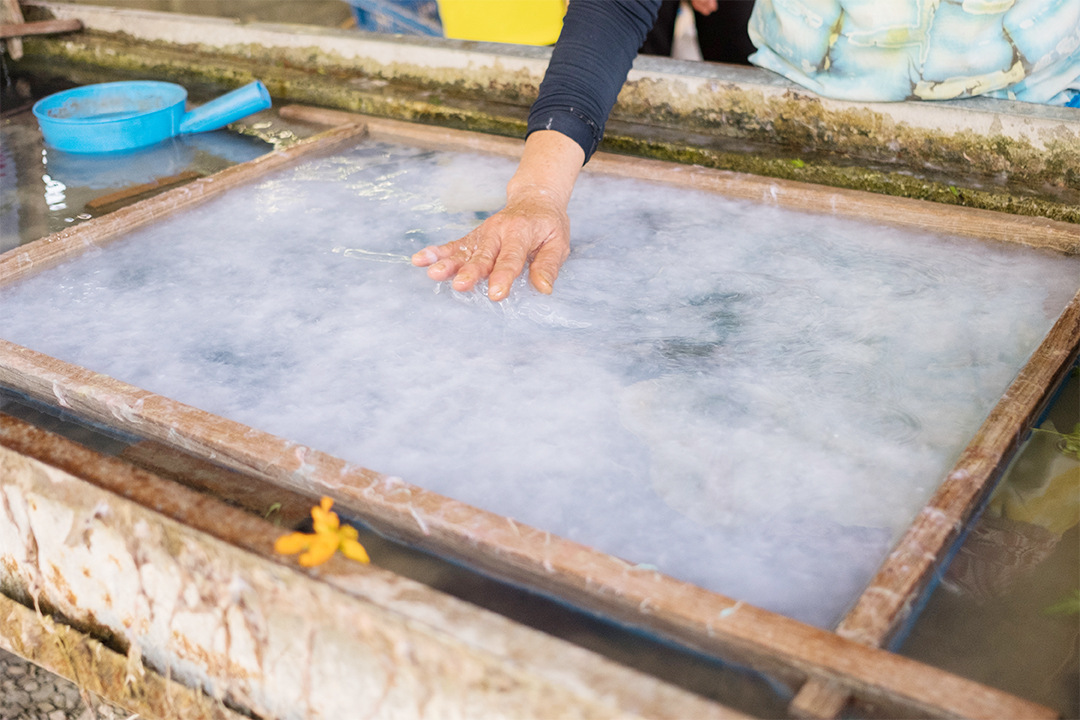
What is Molded pulp?
When we think of “paper,” we often imagine thin, sheet-like materials used for printing. However, paper products like egg cartons, used as packaging materials, are molded into three-dimensional shapes. Products created in this manner using pulp are called “Molded pulp products.” Molded pulp is the process of shaping plant fibers (pulp) with molds into three-dimensional forms.
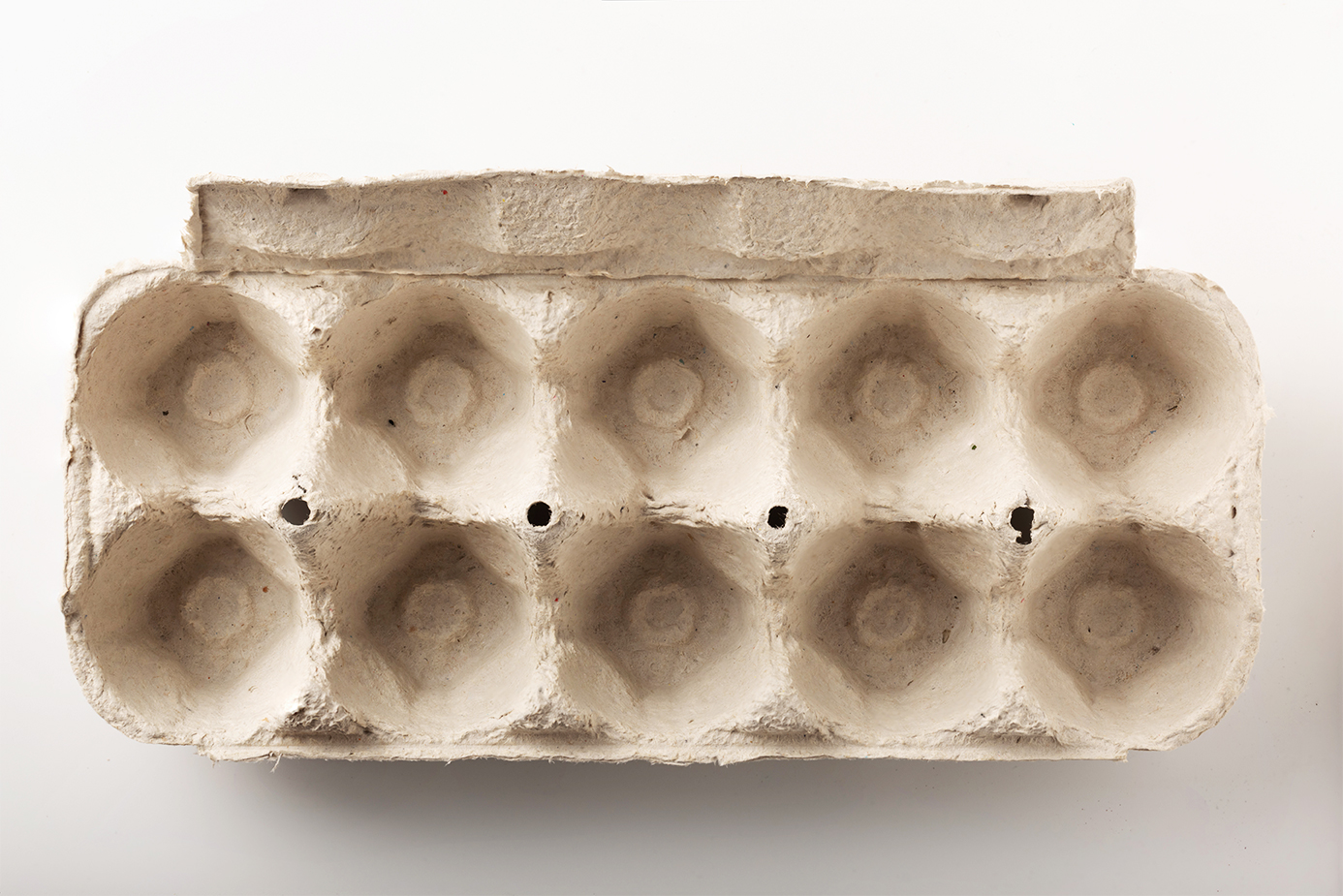
Features of Molded pulp Products
Molded pulp products possess the following characteristics:
Environmentally Friendly Material:
Molded pulp mainly uses plant fibers, basically eliminating the need for plastic materials. As a result, these products are biodegradable. Biodegradation is a natural process in which microorganisms consume the material, breaking it down into natural byproducts such as carbon dioxide, methane, water, and biomass when left in environments like compost. Testing shows that these products start to decompose after two weeks, lose their original shape after five weeks, and can become compost in about three months. However, it’s essential to note that the biodegradable nature of these products may make them susceptible to pests, so some caution is necessary. Additionally, they can be recycled as paper, contributing to sustainability with a lower environmental footprint.

Warm Texture:
Traditionally, paper has been used extensively in Japan for items like shoji screens and fusuma doors. The texture and feel of these products cannot be replicated with plastic. By employing modern molded pulp, products can be given a warm and tactile texture. However, it’s important to note that due to the characteristics of paper as a material, these products may lose strength and deform in high-temperature and high-humidity environments.
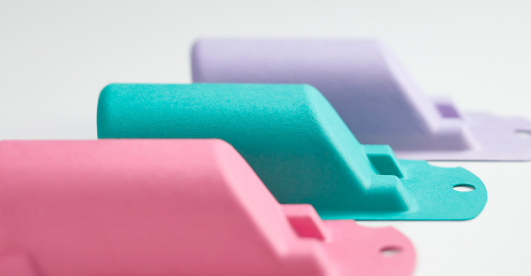
Types and Features of Molded pulp Technologies for Plastic-Free Packaging
The most well-known Molded pulp method is known as ” Molded fiber.” While Molded fiber has been used for items like egg cartons and electronic product packaging for a long time, recent years have seen the development and practical use of various processing methods, including injection molding and foam molding, to accelerate the transition away from plastic packaging
Now, let’s introduce the types and features of molded pulp, as well as the suitable applications for each molding technique.
Molded fiber
Molded fiber is a manufacturing method where paper fibers dissolved in water are deposited onto the surface of a mold, and then dried and solidified to create the desired shape. This process involves applying the material onto the surface of a convex-shaped mold and using suction to shape it. The resulting product typically has a thickness of approximately 1 to 3 millimeters.
Materials used include recycled paper, wood pulp, bamboo fibers, sugarcane fibers, and other fiber materials. It primarily relies on paper and water as raw materials, without the addition of starch or adhesives.
Molded fiber is a technology with a long history, dating back to the 1920s when it was already in use, notably for speaker cones. It is frequently employed for relatively simple-shaped molded products such as trays for eggs and fruits, as well as packaging materials for electronic products.
For more detailed information on Molded fiber, you can find further information here.
Dry / Wet Molded fiber
There are two main types of molded fiber, namely dry molded fiber and wet molded fiber. The difference between dry and wet lies in the drying method.
“Dry molded fiber ” are formed in a mold and then poured into an oven to dry.
Therefore, it has a rough surface like an egg carton and is characterized by its high cushioning property.
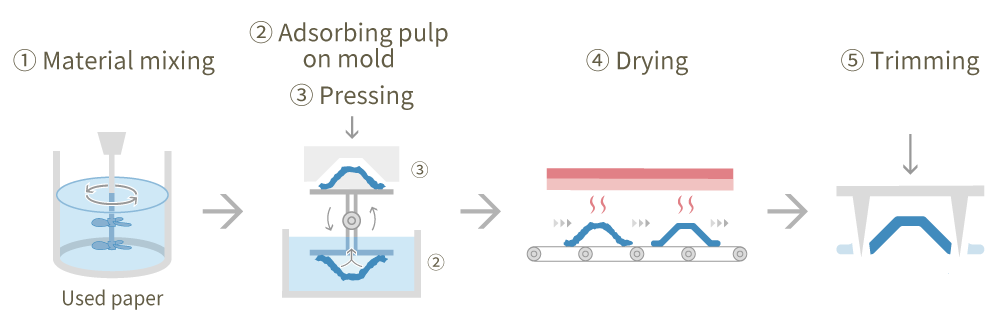
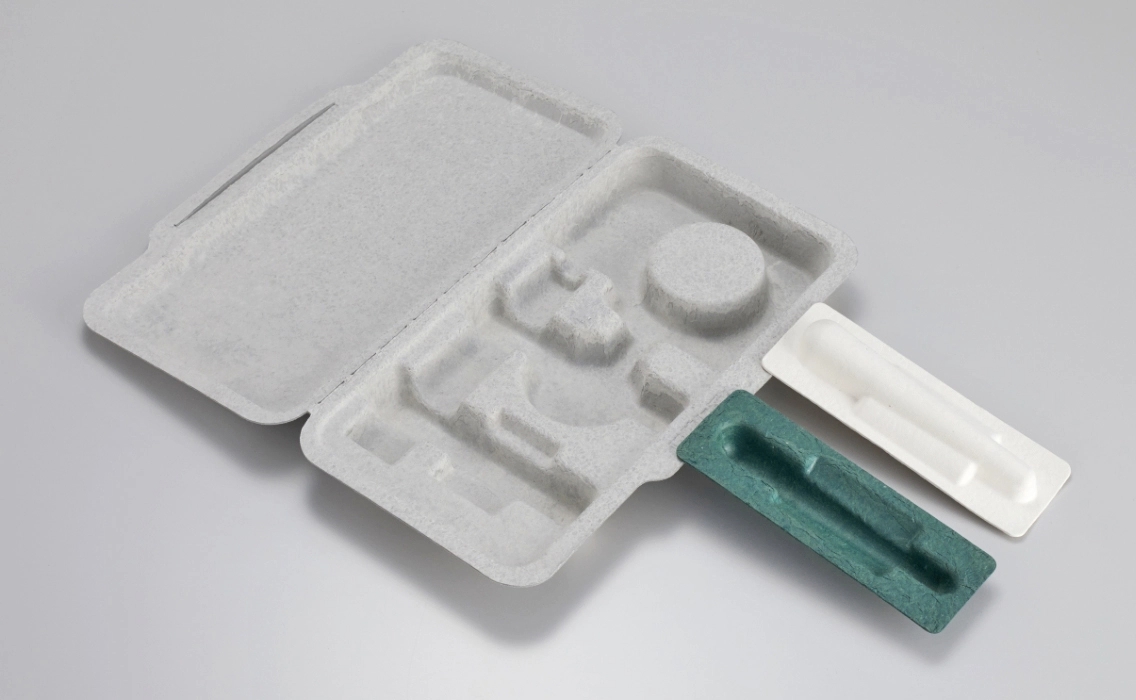
On the other hand, the “Wet molded fiber” is dried by pressing the pulp in the mold while drying it to remove the water content.
This process results in a very smooth surface.
Dry molded fiber are often used for cushioning materials, whereas wet molded fiber are often used for outer boxes and other applications that require high design quality.
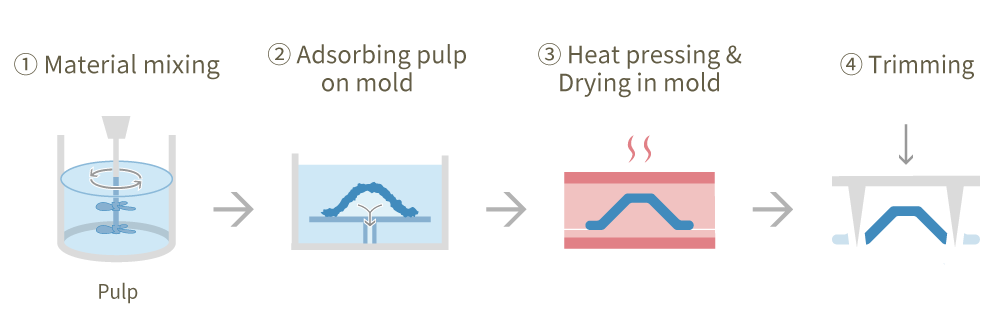
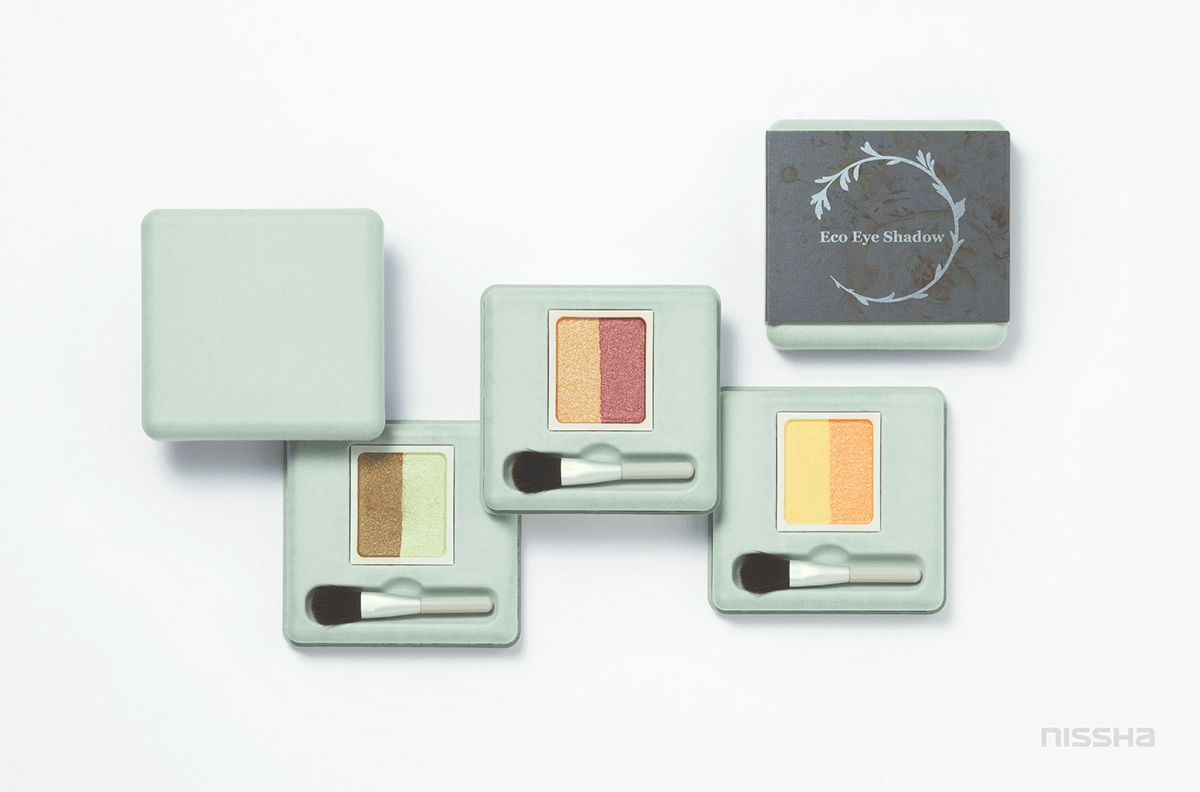
Pulp injection
Pulp injection is a method where the raw material is injected and filled into a sealed mold for shaping. The raw material for injection molding consists of pulp and starch dissolved in water, mixed thoroughly to create a paste-like substance, and then prepared in the form of small, rice-grain-sized pellets. These prepared pellets are heated within the injection nozzle, transforming them into a viscous molten state.
This molten material is then injected and filled into the mold, and further heating is applied to evaporate the moisture content within the material. This process results in the production of Molded pulp products.
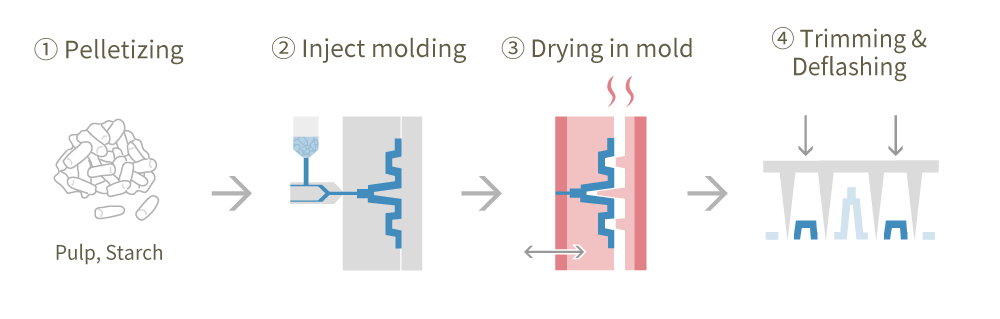
Pulp injection molding allows for the production of molded products with more intricate and complex shapes compared to traditional Molded fiber methods. It is particularly useful for creating molded products with features like rib structures for increased strength. However, since the raw material includes starch for binding the fibers, recycling these products as paper may depend on local regulations and policies.
For more detailed information on pulp injection molding, please visit our [guide here]
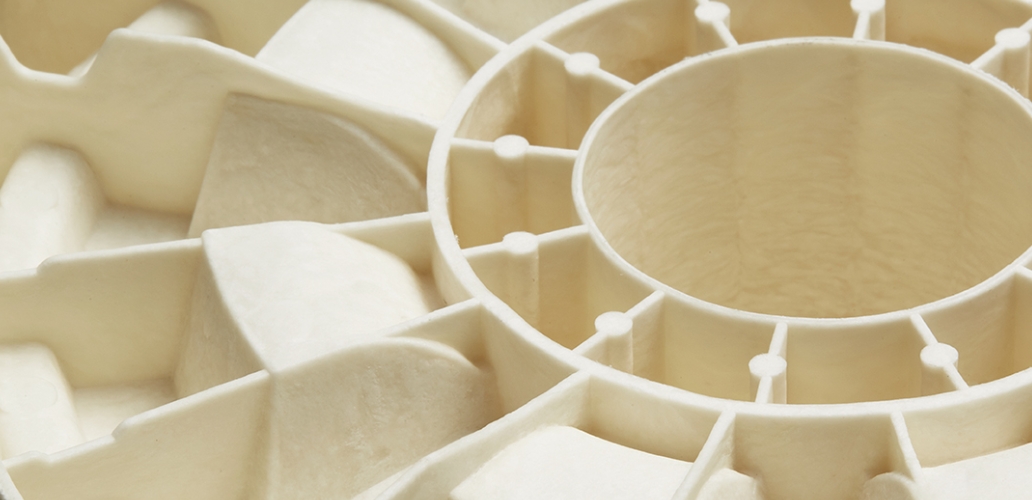
Pulp foam molding
Pulp foam molding is a molding method that involves filling the mold with a mixture of material containing foam ingredients, and then heating it to create tiny bubbles inside the molded product.
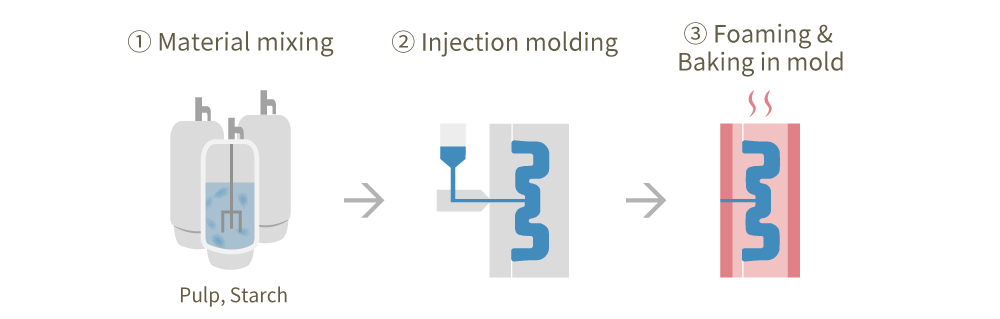
These bubbles result in lightweight products that also offer excellent cushioning properties. Pulp foam molding is particularly suitable for packaging products that require cushioning, such as electronics, cosmetics, medical devices, and pharmaceuticals.
For more detailed information on pulp foam molding, please visit our [guide here]
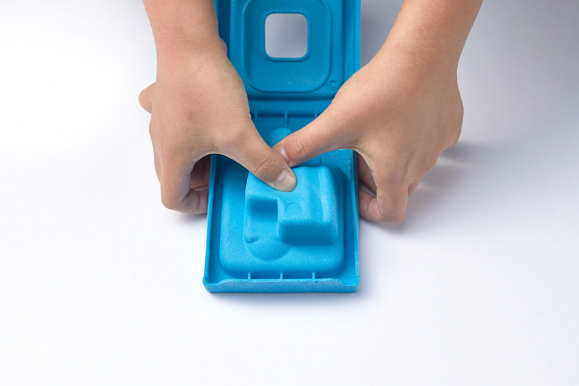
Conclusion: Achieving Plastic-Free Packaging with Molded pulp Technologies
Efforts to address environmental issues such as marine plastics and global warming have gained increasing global importance. Molded pulp products have garnered attention as a sustainable alternative to plastic, serving as plastic-free products and replacing expanded polystyrene (EPS) cushioning materials.
We provide Molded pulp products tailored to your specific needs and objectives.
We offer a range of Molded pulp products tailored to specific purposes, including Molded fiber, pulp injection molding, and pulp foam molding.
For more information on these products, please visit our product website.