PaperFoam®
Foam Molded Products -
Lightweight and Cushioning
- Foam molding of pulp and starch
- Lightweight but high cushioning properties
- Securely fix products or components
- Lightweight compared to plastic
(specific gravity: approx. 0.2) - Extensive design freedom in shape achieved through molding process
- Various colors, textures, embossing options
- Recyclable as paper*
*It depends on the regulations and guidelines of each country or region.
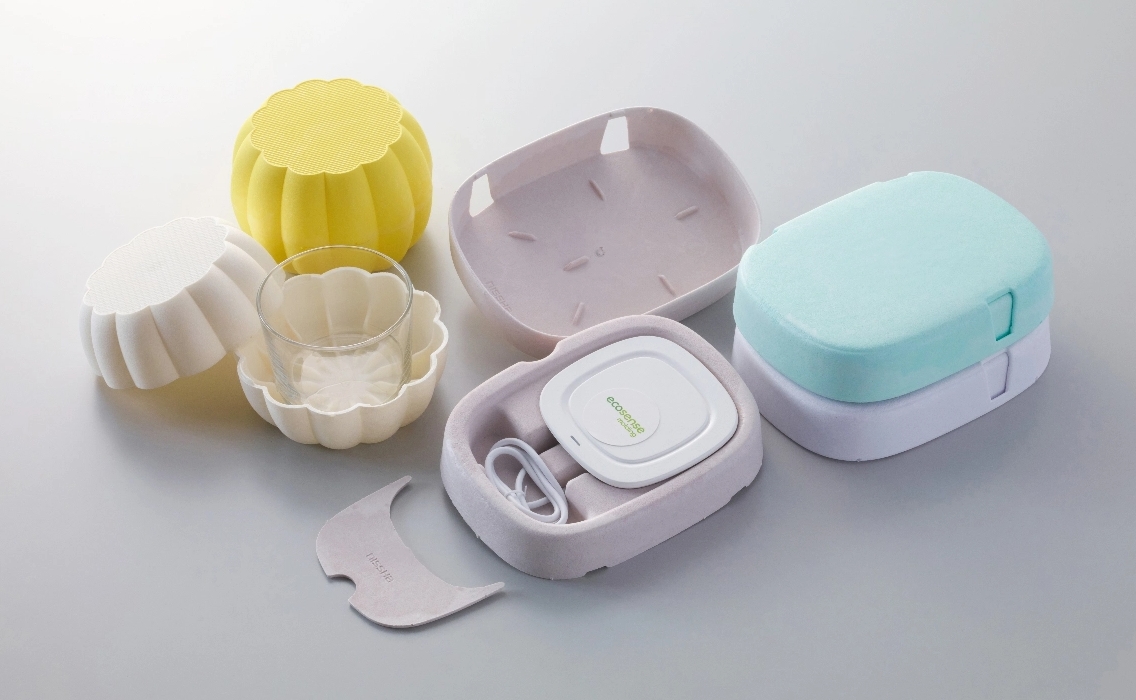
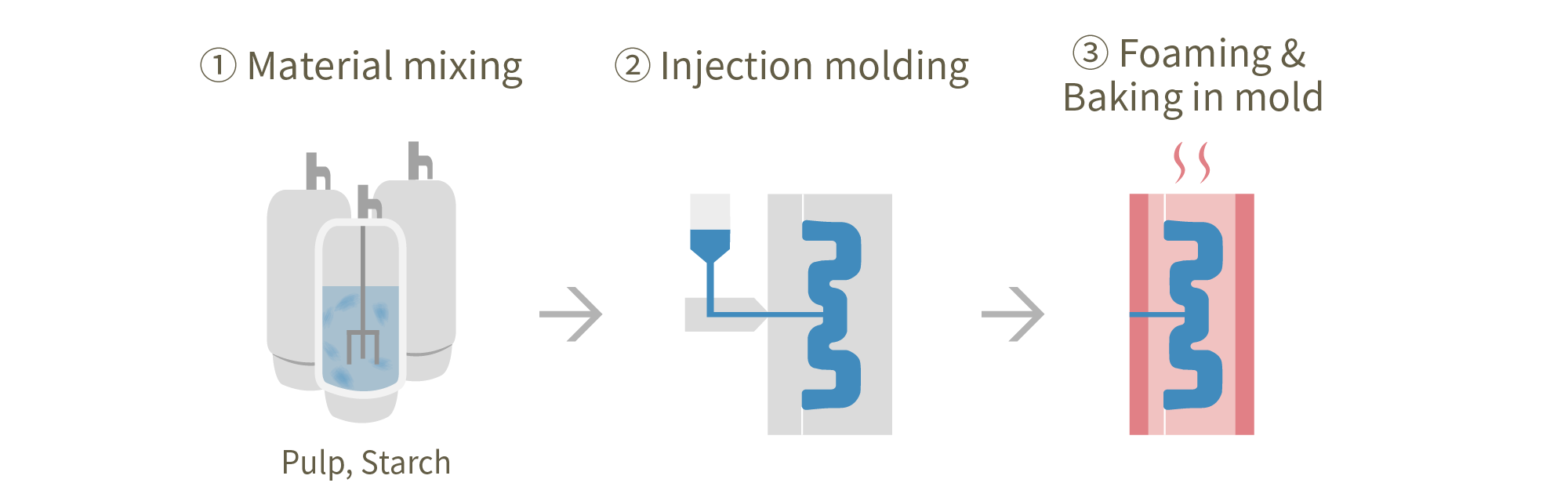
Process
- The main ingredients, starch and pulp, are mixed with water and injected into the mold.
- Heat is applied simultaneously during molding to cause foaming and create a 3D shape.
- At the same time, the moisture inside the material is evaporated, drying the product and completing the manufacturing process.
Key Features
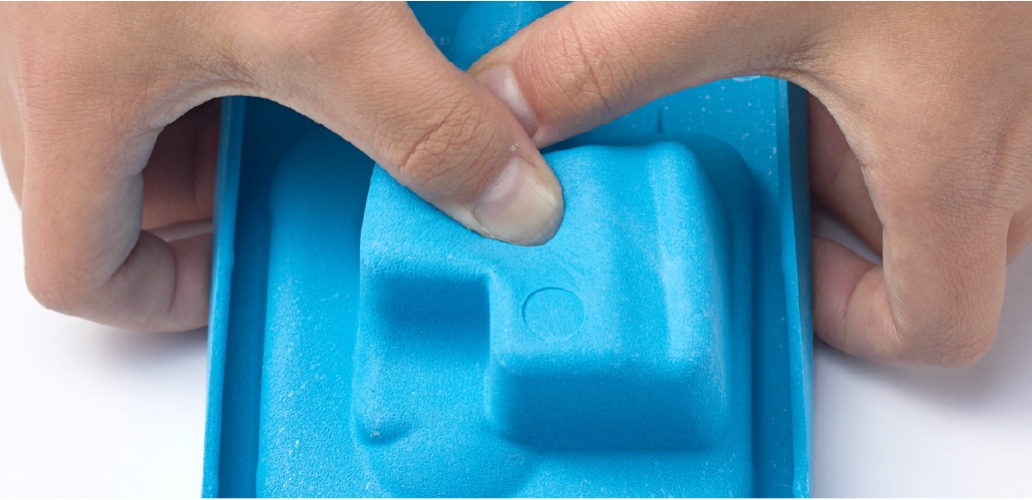
- Lightweight and Cushioning properties
- PaperFoam® has excellent cushioning properties due to its foaming process. Additionally, its lightweight material properties (specific gravity is approx. 0.2) contribute to total weight reduction of packaging.
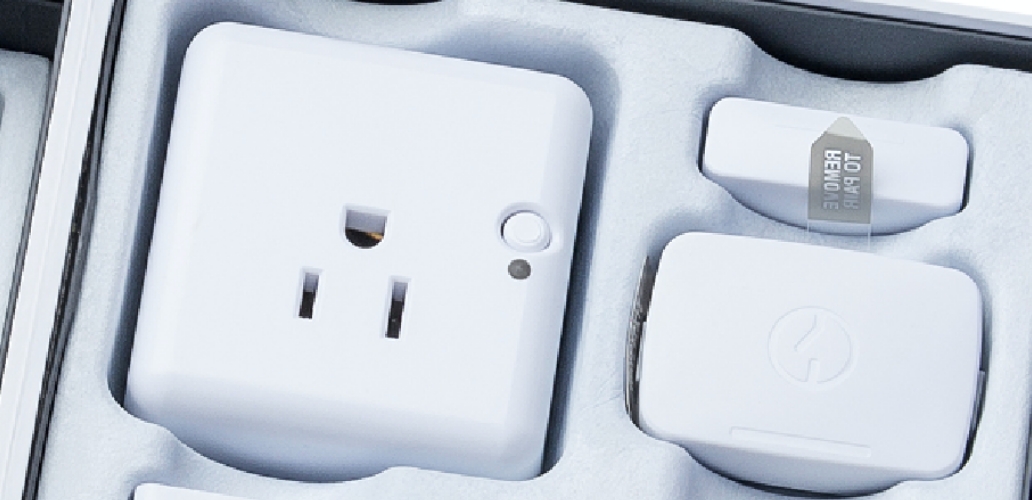
- Securely fix products or components
- Thanks to the molding process, PaperFoam® is capable of taking on a shape that perfectly fits to the product, providing a secure fit and effectively safeguarding it against shakings and vibrations during transportation.
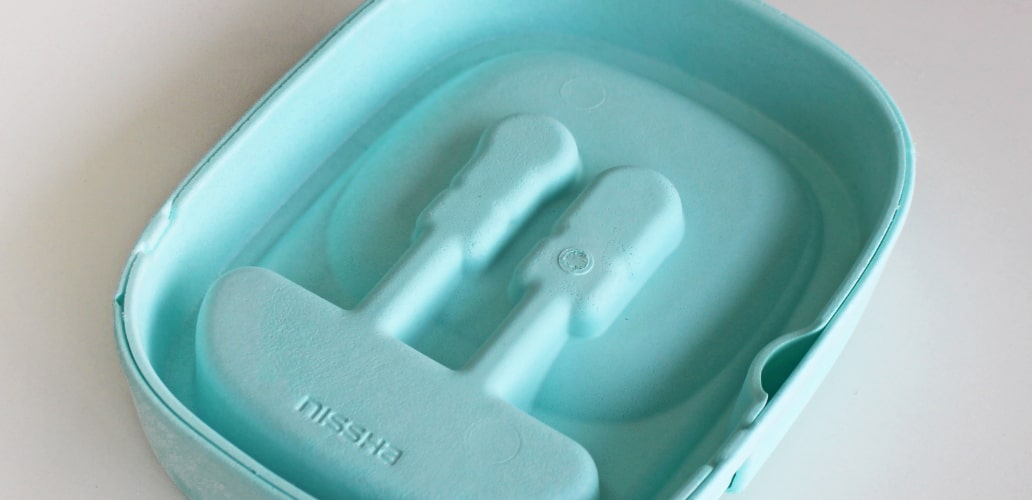
- Precise dimensional accuracy
- It is possible to design an integrated tray by combining several packaging parts made of PaperFoam®, such as the lid and body, thanks to its precise dimensional accuracy.
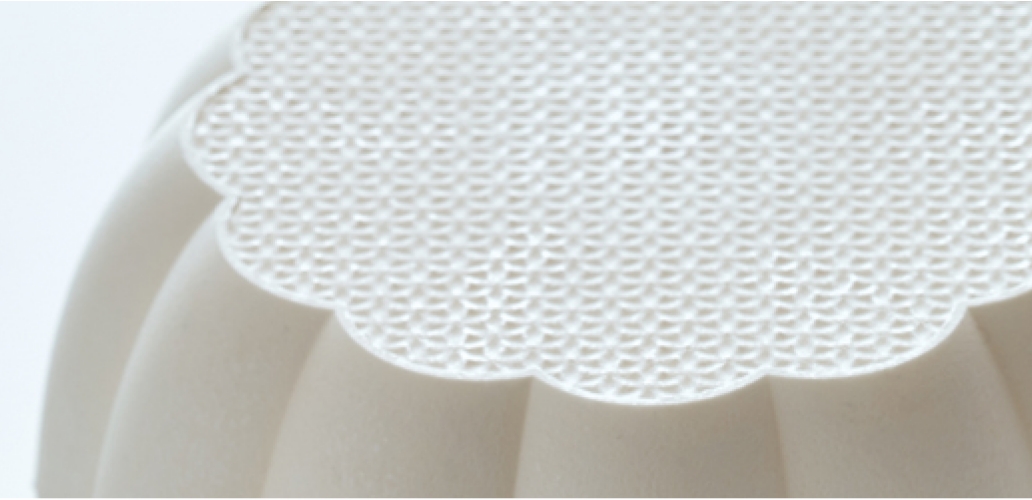
- Customized textures and colors
- Products can be colored, textured and embossed in a wide range of designs.
Applications
-
Mobile battery
case -
Cosmetics
Set box inner tray -
CPG (Earplug)
Inner tray
Certification

TUV Austria OK biobased (4 stars)
TUV Austria OK compost Home & Industrial
UL Validated: 99% recovery rate of available fibers
Specification
Max. parts size(mm) | 200 × 300 × 150 |
---|
Parts thickness(mm) | 2.2 〜 3.0 |
---|
Minimum radius(mm) | 2.0 |
---|
Typical production volume (annually)(pcs) | 100,000 〜 |
---|