Blog
Pulp-Injection – Biodegradable, Recyclable Injection Molded Paper / Pulp
2023/07/05
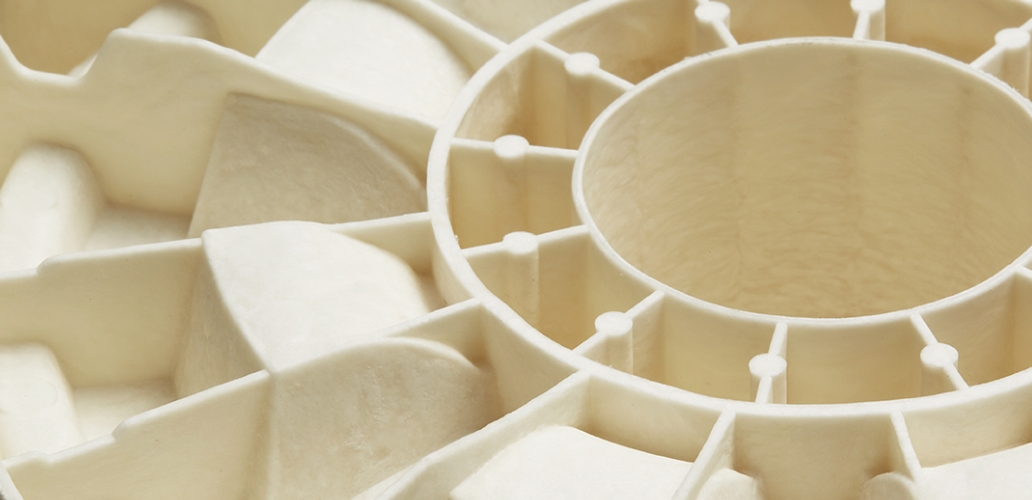
Injection molding technology is utilized across various industries, ranging from consumer electronics housing and beauty and cosmetics to everyday goods and their packaging. It allows for the creation of intricate shapes using plastic materials on a large scale, ensuring consistent quality at an affordable cost. However, the petroleum-based polymers used in injection molding have numerous environmental impacts. Presently, this concern is escalating worldwide, prompting us to contemplate ways to maintain a clean and sustainable Earth and transition our mass consumption society to one that is eco-friendly.
This is why Nissha is actively developing Pulp-Injection, one of the products in the Pulp Series of ecosense molding. It provides exceptional, precise, and distinctive solutions.
What is Pulp-Injection?
Instead of using plastic resin, this technology employs injection molding to create three-dimensional structural parts using injection-molded “paper (pulp)”. This innovative approach utilizes environmentally friendly and sustainable materials. The molded parts possess a distinctive surface finish like a paper, which imparts a nature feel. Not only is the product recyclable biodegradable, created from natural materials, and environmentally friendly, but users can also experience the unique tactile sensation of the pulp material.
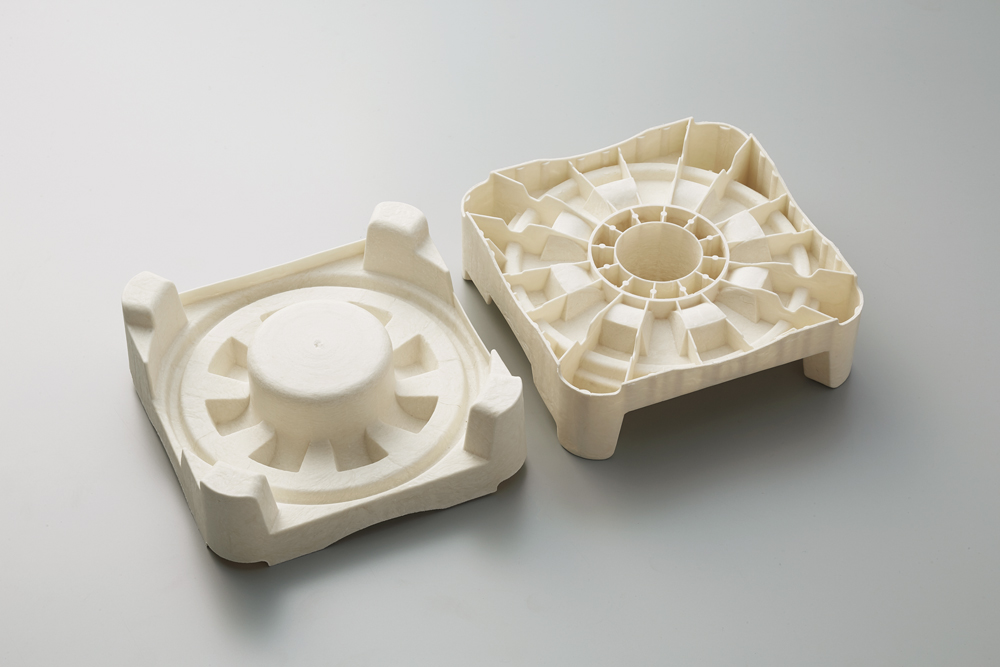
Process
The process is straightforward and can be likened to conventional plastic injection molding. It involves heating resin pellets, melting the resin, and then injecting it into a molding tool to produce three-dimensional structural parts. However, there are two notable distinctions: instead of plastic, the material used is pulp, and it is necessary to remove moisture from the Pulp-Injection material. The process involves mixing pellets with water before injection molding, so during the injection molding process, it is essential to periodically and slightly open the tool to facilitate the drying of the material.
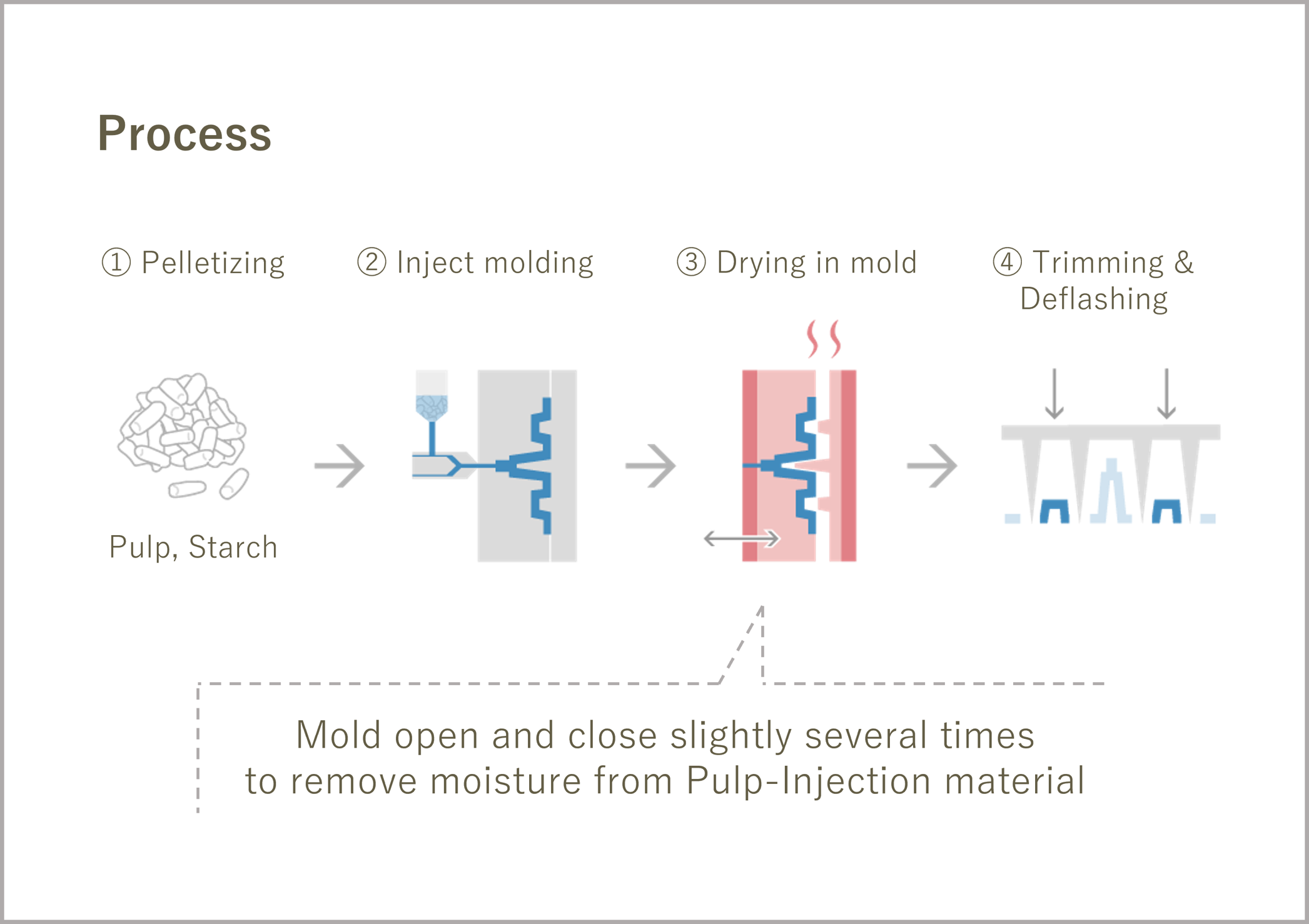
Geometry design freedom
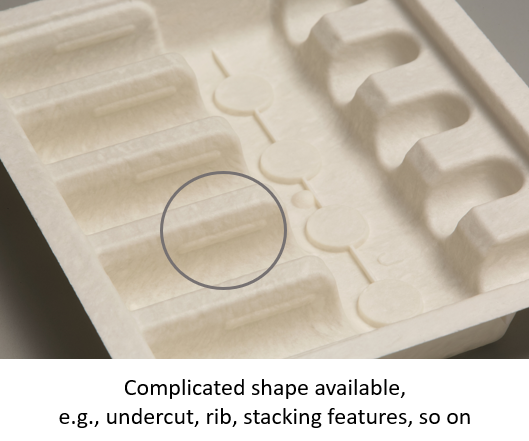
This is one of the key unique features of Pulp -Injection technology. Since the process is derived from injection molding, we can achieve the shaping and formation of any possible geometry using paper/pulp. In other words, Pulp-Injection offers significantly greater design freedom compared to other conventional pulp / paper processes such as molded pulp or folding box. Take a look at the geometry features: intricate geometry, thin walls, undercuts, and thickness deviation. Pulp-Injection parts exhibit high precision and boast a beautiful surface quality.
Material of Pulp-Injection, comes from nature
The Pulp-Injection material is environmentally friendly and sourced from natural materials. Its main ingredients are pulp (paper), starch. The Pulp-Injection products or parts are recyclable and biodegradable※.
- ※Evaluated as recyclable*1 as paperboard by the PTS method at a third-party European institution*2.
- *1 Can be blended up to 10% for paperboard
- *2 KCL Oy
Application of Pulp-Injection
Pulp-Injection products provide an exceptional user experience while being environmentally friendly, thanks to their structural versatility, design capabilities, and authentic texture. Pulp-Injection is particularly well-suited for applications such as medical, pharmaceutical, and cosmetics packaging trays that require functionality, rigidity and premium surface quality. Additionally, due to its precise and highly flexible geometry and design, it seamlessly integrates with automation processes and conveyor robots. We believe the potential applications are limitless and eagerly anticipate collaborating with our customers to develop unique and value-added uses.