Pulp-Molding
Mature fiber technology with beautiful, luxurious smooth texture
- Various surface finishes – ranging from smooth and luxurious to a rough texture reminiscent of paper.
- Precise accuracy of fit ensures a snug fit between the body and lid.
- Mold technology with minimal draft angles.
- Available in both wet and dry press process.
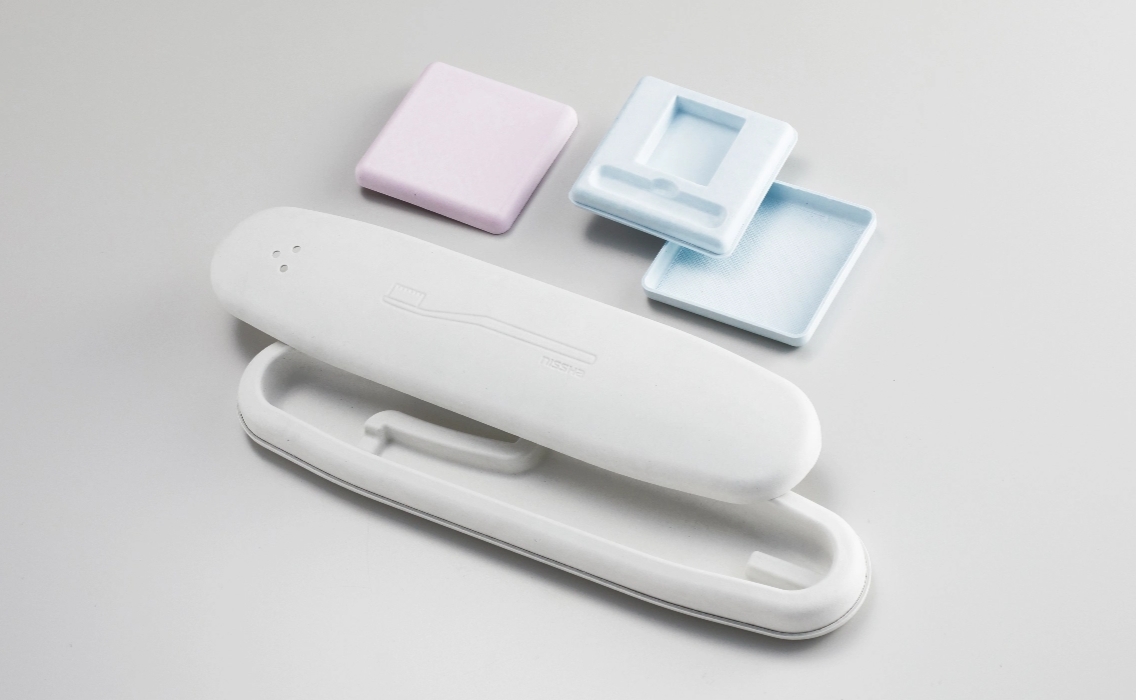
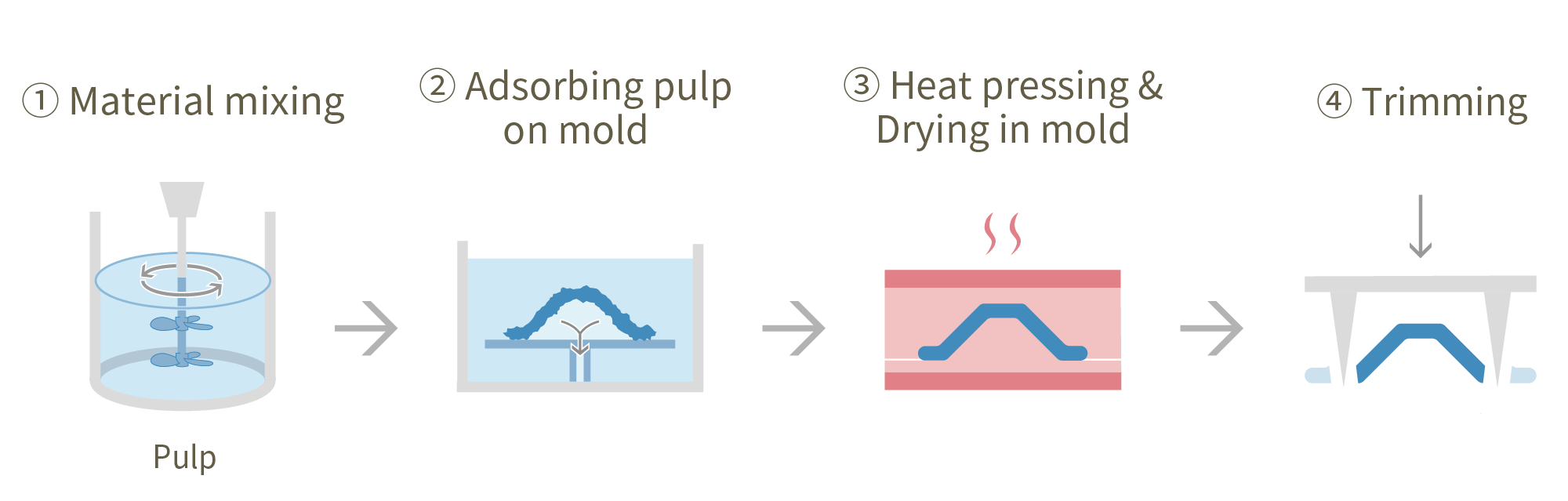
Process( wet mold )
- Pulp is mixed with water.
- Pulp is applied to a mesh-covered mold and formed.
- A press mold is utilized to clamp the material from the top and bottom, while heat and pressure is applied to press it and remove moisture.
- After molding, the products are trimmed to remove excess material.
Key Features
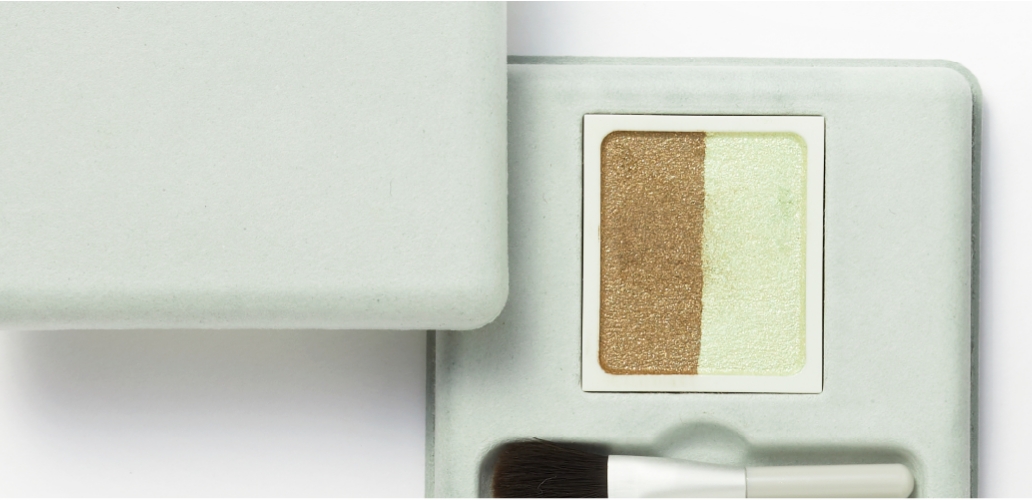
- Smooth and luxurious surface texture
- It features a smooth surface achieved through wet press process, providing a soft and gentle texture. It is suitable for products that require beauty and a sense of luxury.
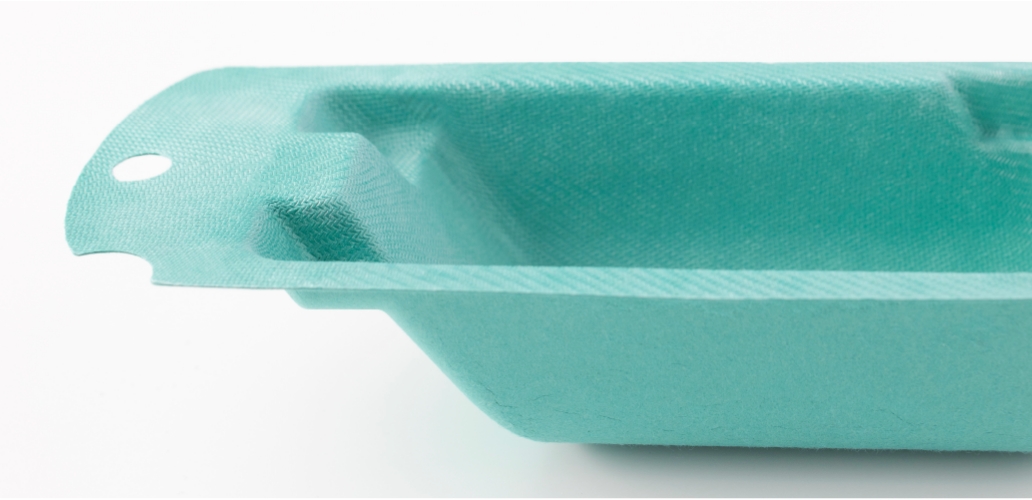
- Thinness
- The standard wall thickness is 0.7 to 1.5 mm and can be changed freely. This construction method works with lightweight and design-oriented designs.
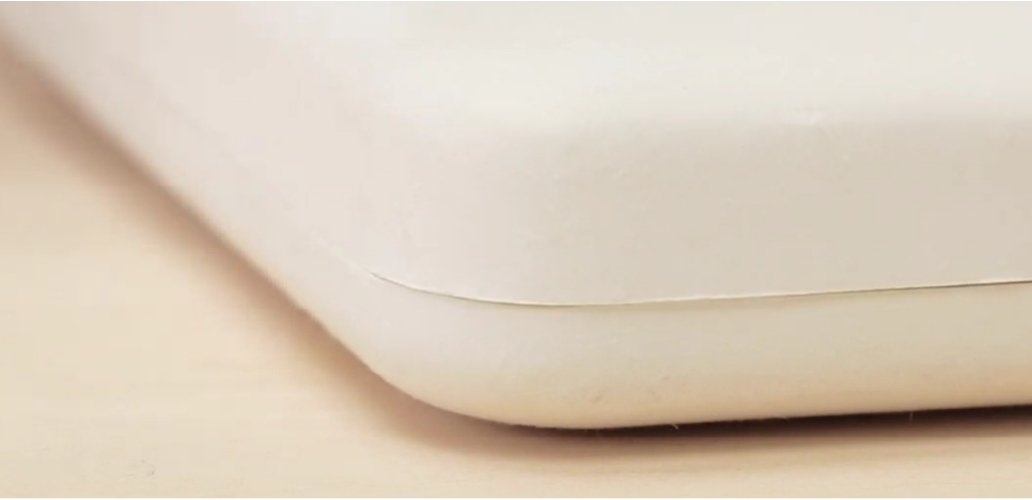
- Precise accuracy of fit
- It allows for the design of steep draft angles and minimal taper, enabling precise fitting of the body and lid.
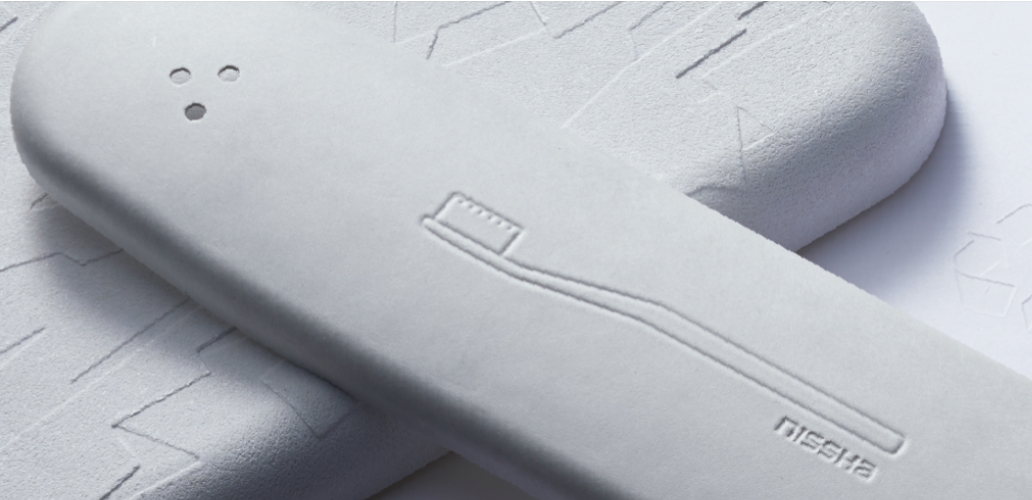
- A wide variety of textures available
- Coloring and engraving can be applied. The surface of molded products can be freely textured, to blend seamlessly with a wide range of products.
Applications
-
Food
Display/package case -
Cosmetics
Mascara blister -
Cosmetics
SoftLock® Box
Specification
Max. parts size(mm) | 960 × 800 × 80 |
---|
Parts thickness(mm) | 0.7 ~ 5.0* *Thick-wall parts is only available by dry process |
---|
Minimum radius(mm) | 1.0 ~ 2.0 |
---|
Typical production volume(annually)(pcs) | 200,000 〜 |
---|