Blog
Molded Fiber– A Comprehensive Guide of Eco-Friendly and Their Innovative Applications
2023/08/18
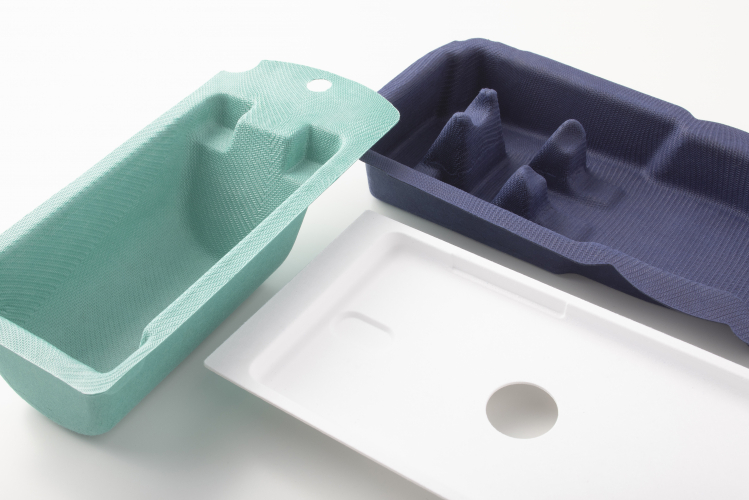
Pulp-Molding, also known as Molded Fiber in the industry, has emerged as an eco-conscious alternative, reducing the environmental impact caused by plastic. However, within the realm of Pulp-Molding/Molded Fiber, various products with distinct characteristics exist, making it essential to choose the most suitable one depending on whether the emphasis is on design or strength. In this article, we will delve into the process and applications of Pulp-Molding while introducing its advanced forms – two unique pulp molding technologies that Nissha also offers: Pulp-Injection and PaperFoam®. We will highlight their differences in the manufacturing process and unique features.
What is Molded Fiber?
Pulp-Molding, also known as Molded Fiber, is the molded packaging products or its manufacturing process that uses pulp, including recycled pulp/paper, derived from wood fibers, bamboo, bagasse as raw material. Because the raw material is bio-based, the packaging is biodegradable and recyclable. It offers a warm paper texture, tactile sensation, breathability, and water retention.
Originating approximately a century ago as materials for speaker cones, molded fiber products are now extensively used in various applications, including trays and boxes for food, CPG goods, medical devices, pharmaceuticals, and electronic devices.
Process
The manufacturing process of Pulp-Molding / Molded Fiber involves the following steps.
Raw Material Preparation
Pulp Molding commonly employs recycled paper, cardboard, and sometimes virgin paper, that come from wood fibers, bamboo, and bagasse. The paper or fibers used as raw materials are processed in a machine called a pulper, where they are mixed with water and crushed into a slurry using large blades. This crushed recycled paper transforms into a muddy liquid material. The liquid material undergoes centrifugation and screen filtering to remove foreign objects such as metal pieces and debris. Once filtered, the remaining slurry contains only water and pulp fibers, which is then used for molding. No additives such as glue or adhesives are used in this process.
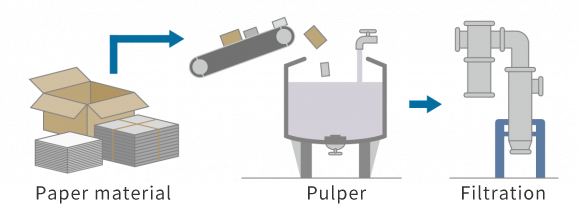
Molding and Drying
The filtered and adjusted slurry is poured into a material tank. Molds are immersed in the material tank, allowing the slurry to absorb and layer the pulp fibers on the mesh-like surface of the molds. The pulp fibers on the mesh surface are fixed to the shape of the molds. The molded fiber material is then covered with pressing molds. The material is compressed between the molding and pressing molds, removing the water content.
The compressed molded fiber material is transferred to the pressing mold side. The material on the pressing mold is placed on a conveyor and passed through a drying oven, eliminating all moisture and completing the molded fiber product.
The above is the basic processing flow of molded fiber. The actual manufacturing process is slightly adjusted based on the characteristics such as the thickness, strength, surface finishes and design of the molded products.
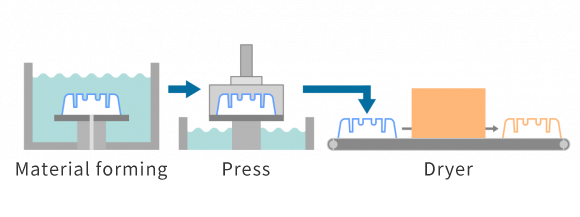
Dry Press Molding and Wet Press Molding, Understanding the Differences
Pulp-Molding / Molded Fiber comes in two manufacturing methods: Wet press molding and Dry press molding. Each method is used selectively based on product thickness, packaging requirements, and desired appearance quality.
Dry Press Molding
Dry Press Molding is a type of Pulp-Molding product where heat pressing is not involved, resulting in a rough paper-like texture. It primarily uses recycled paper or old paper as raw materials, and the pulp material adheres and layers in the tooling without undergoing pressing. It’s also called Thick Mold, featuring a coarse surface texture and a thickness of 5-10mm. They are commonly used as cushioning materials for heavy items like machinery, automotive, appliance components.
Additionally, there is a version called Transfer Mold, which involves adding a pressing process to achieve a smoother surface finish. After forming the pulp in the tooling, it undergoes compression dehydration in a press tooling (without applying heat), and then it is moved to a drying oven for further drying. Transfer Mold products are commonly used as packaging trays for household appliances and medical devices.

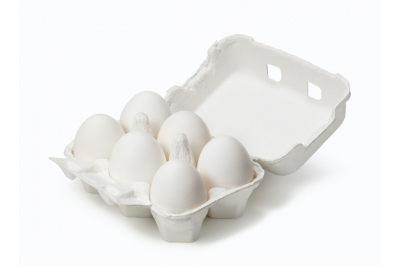
Wet Press Molding
Wet Press Molding, also known as Thermoformed Mold, utilizes a heated press tooling to complete the compression, dehydration, and drying of the molded pulp material within the tooling. Molding with a heated press tooling enhances the efficiency of dehydration and allows the pulp material to be compressed to a high density, resulting in an exceptionally smooth and high-quality surface texture. The pulp material is formed into thin wall with a thickness of 1 to 3mm, and this method enables the molding of complex shapes. As a result, it is well-suited for products that demand design aesthetics, such as consumer electronics and cosmetic packaging.
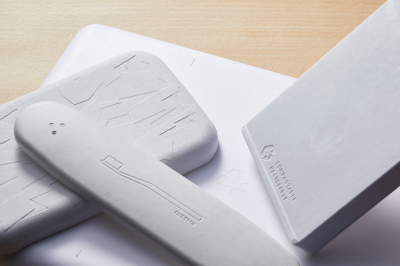
Pulp-Injection and PaperFoam® – Development from Pulp Molding
Pulp molding, which has been commonly used as packaging material, is now facing various demands. These demands include the need for design versatility to withstand the use as luxury packaging, the ability to provide cushioning for glass products, and the capability to create complex shapes for use as functional components beyond simple packaging tray. In response to this diversification of needs, Nissha has been conducting research and development of new Pulp-Molding technologies. Currently, Nissha offers not only Pulp-Molding but also two new and unique pulp packaging products called Pulp-Injection and PaperFoam®.
Pulp-Injection
Pulp-Injection is a technology that molds pulp material using an injection molding process. Its distinctive feature lies in its ability to mold complex structures like snap-fits, bosses, and ribs, similar to plastic molded products.
Materials for Pulp-Injection
Unlike conventional Pulp-Molding that uses a mixture of pulp fibers and water, Pulp-Injection incorporates starch as a binding agent. The mixture of pulp fibers and starch is processed into solid pellets, which are then supplied to the molding machine.
Process
The pellets are filled into the nozzle of the molding machine. Inside the nozzle, the material is heated and moisturized, transforming it into a flowable, viscous state, which is then injected into the tooling. As the material fills the tooling, the tooling undergoes subtle openings and closings, eliminating water content from the material.
After drying, the tool temperature is lowered to cool and solidify the molded product, and the tooling is opened to complete the product.
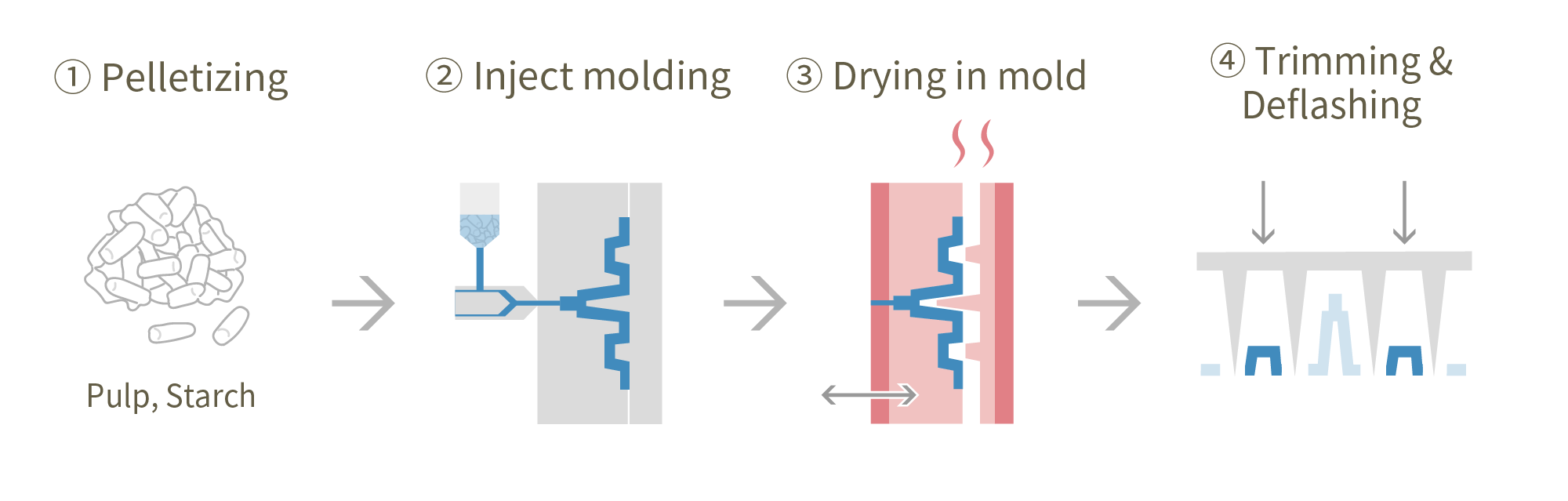
Applications of Pulp-Injection
In Pulp Injection, it is possible to impart complex 3-dimensional shapes like plastic molded parts. It is used for packaging products such as cosmetic cases, medical device trays, and pharmaceutical packaging. For more detailed information about Pulp-Injection, please visit the article Pulp-Injection Biodegradable Injection Molded Paper Pulp or the product site Pulp-Injection.
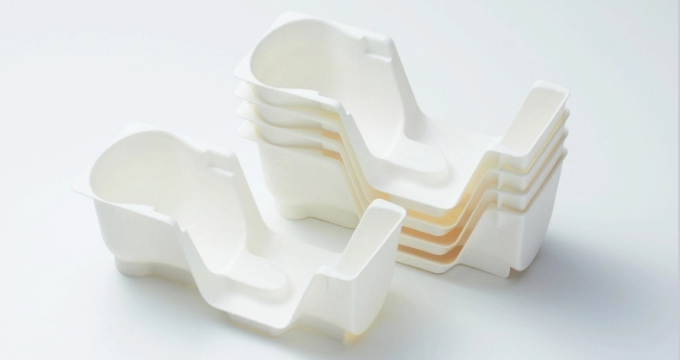
Self injector tray
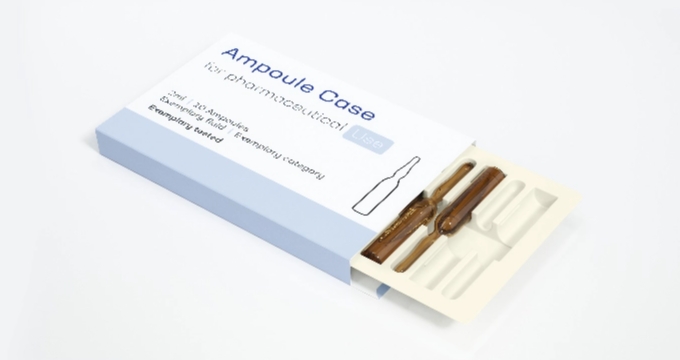
tray
PaperFoam🄬
PaperFoam® is a foaming molding technology made from pulp and starch. By generating bubbles within the molding material, it produces lightweight and flexible molded products.
Materials for PaperFoam🄬
Similar to Pulp-Injection, PaperFoam® uses a mixture of pulp fibers, starch, and water as its materials. The mixture is supplied to the nozzle directly in liquid form.
Process
The heated material is filled into the tooling through the nozzle. After filling, the tooling is heated, causing the material to foam and form numerous fine bubbles within the molded product. After bubble formation, the material is dried within the high-temperature mold, and the tooling is cooled and opened to complete the product.
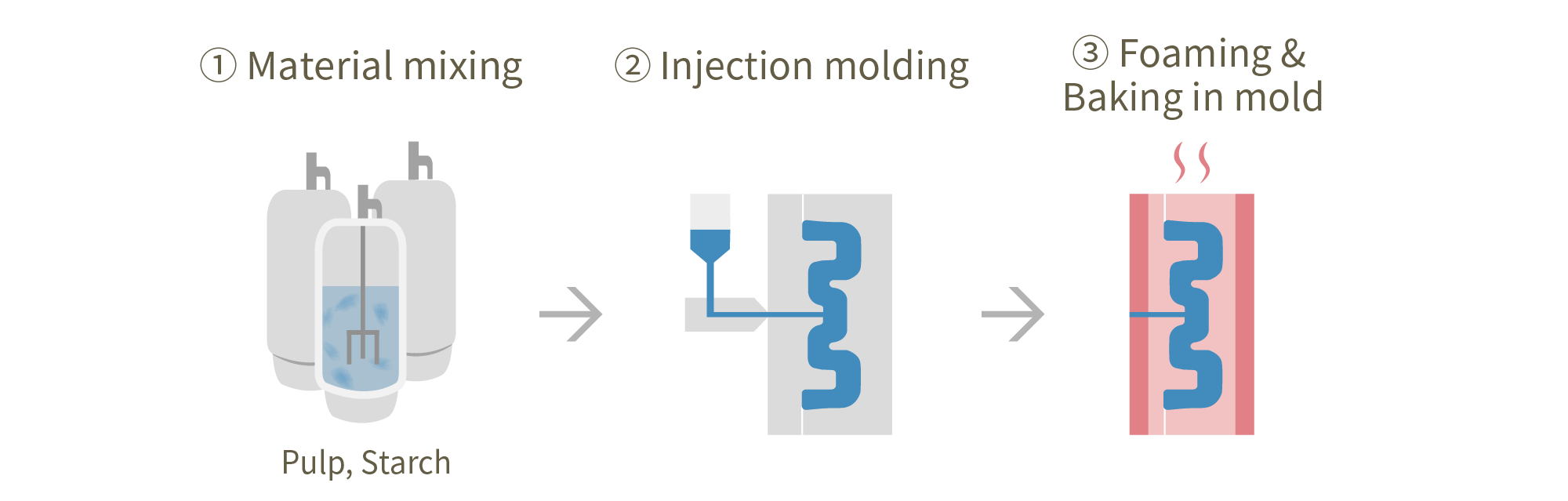
Applications of PaperFoam🄬
PaperFoam® is used for packaging numerous items that require cushioning, such as cosmetics, consumer electronics, medical equipment, pharmaceuticals, and food and beverages. For more detailed information about PaperFoam®, please visit the product site PaperFoam®.
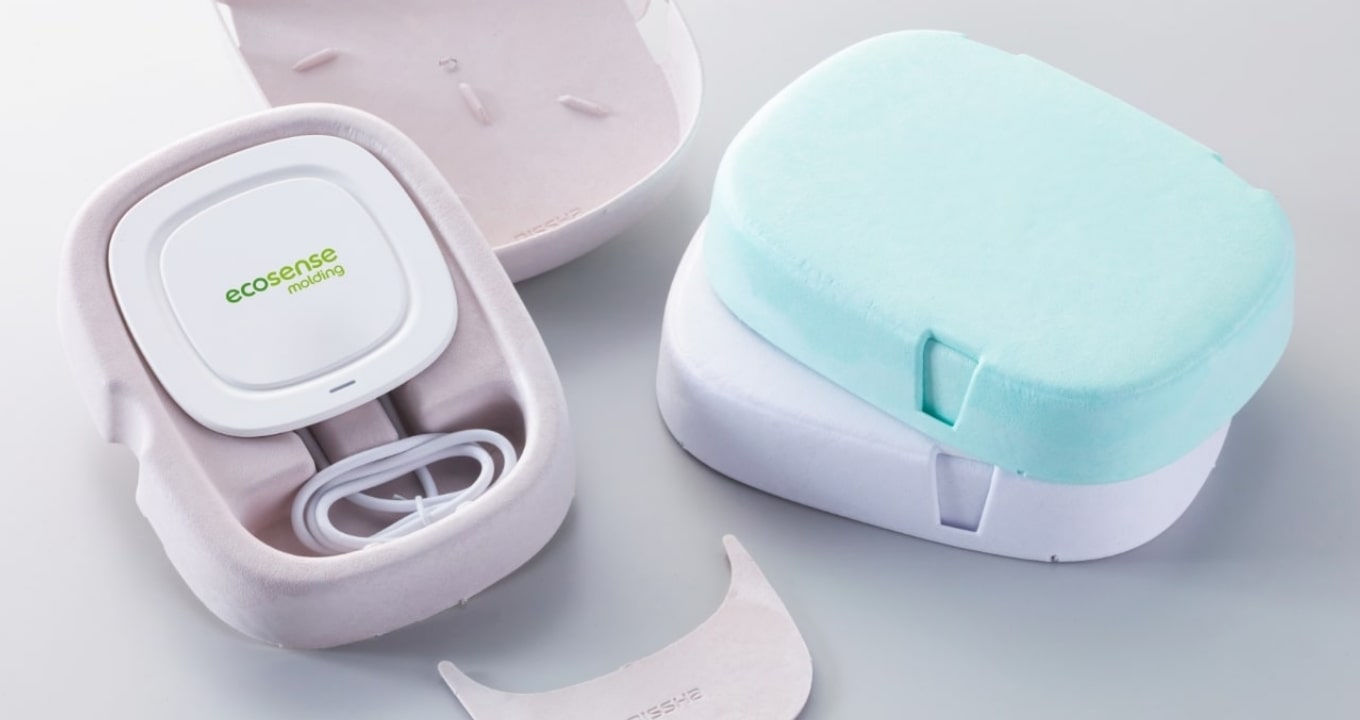
case
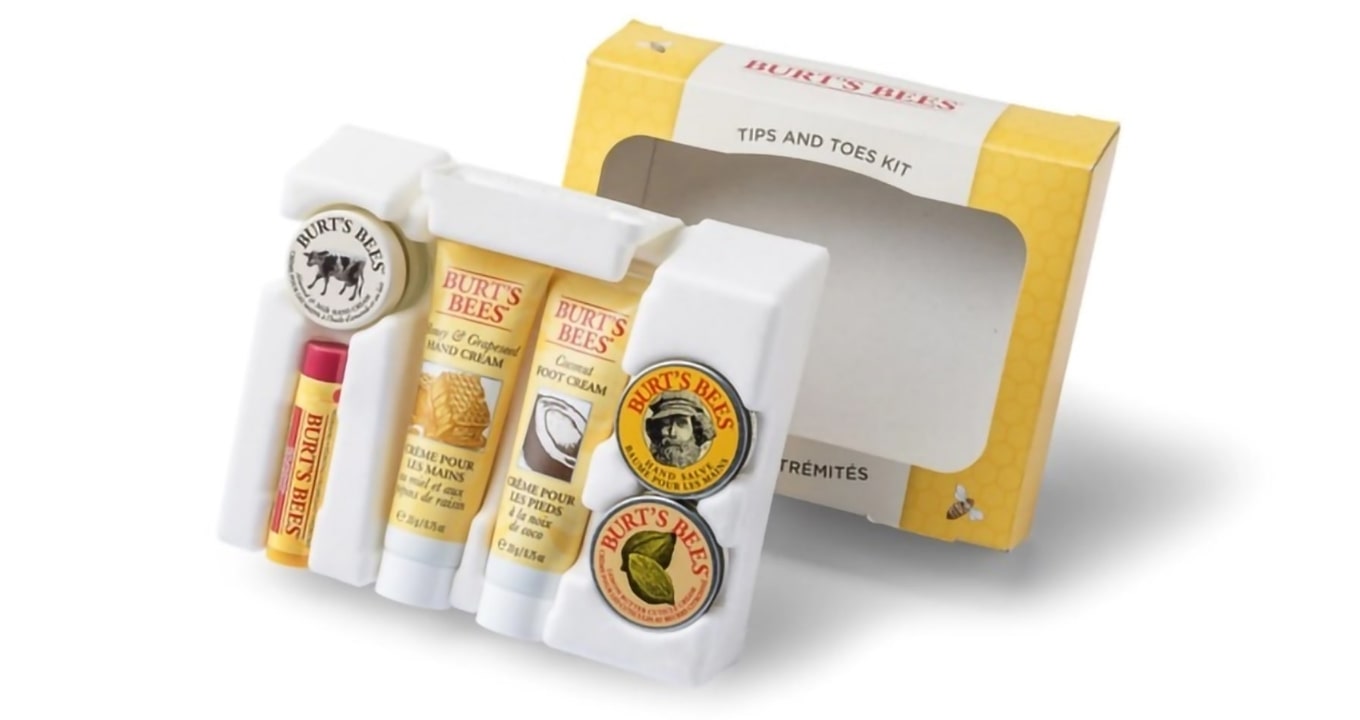
Set box inner tray
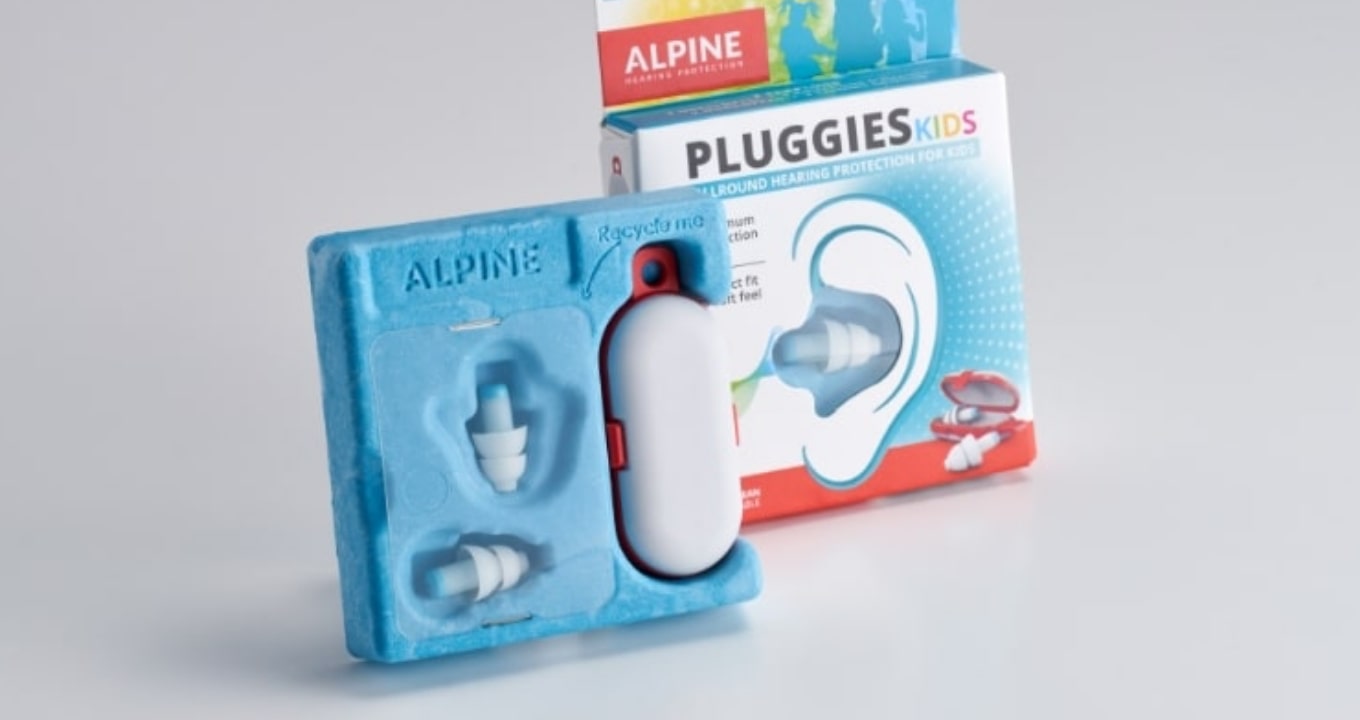
Inner tray
Nissha Offers Customized Molded Fiber Solutions for Your Needs
We have now summarized the features and applications of Pulp Molding / Molded Fiber technologies including Nissha’s unique pulp technologies – Pulp-Injection and PaperFoam®.
We offer a diverse range of pulp packaging products to meet all your sustainable packaging needs. Whether it’s reducing plastic usage, adding biodegradability and recyclability to packaging materials, or exploring innovative design expressions that showcase the unique texture of paper, we are here to cater to various sustainability-driven packaging demands from our valued customers.
For more details about Nissha’s molding technology, visit our product site: ecosense molding- pulp series