Blog
What is Sulapac®, a plant-derived plastic material that returns to nature?
2024/04/05
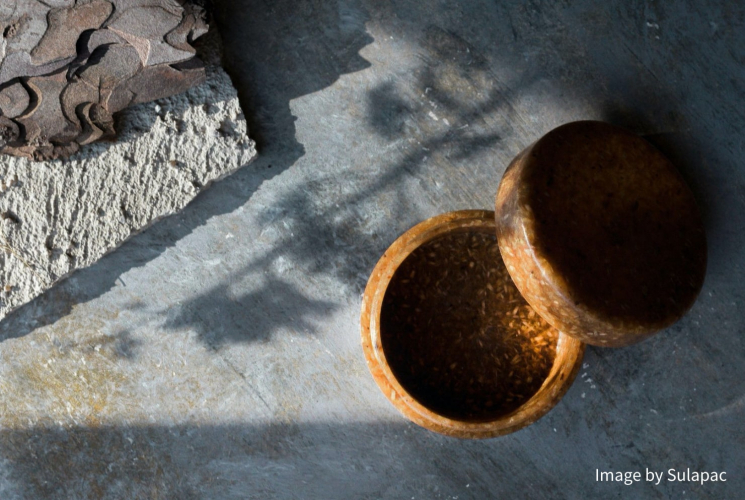
What is Sulapac?
Sulapac was born in Finland in 2016 with the aim of eliminating environmental pollution caused by petroleum-based plastics. Sulapac® is a material developed and designed based on “sustainability,” “beauty,” and “functionality.” It is a “bio-composite material” made by combining two raw materials: wood and waste collected from certified forests and bio-polymer (plant-derived plastic). Sulapac is used both as a material name and as a company name.
What is a bio-composite material?
Generally, materials combined from different raw materials to complement strengths and processability that cannot be achieved with a single material are called “composite materials.” “Bio-composite materials” refer to composite materials made from two or more different raw materials, including plant-derived ones. The types vary widely, and even those composed of petroleum-derived plastics and plant-derived materials are defined as bio-composites.
Sulapac® is up to 100% plant-derived material
Sulapac® is composed of wood chips and bio-polymer (plant-derived plastic), and there are grades made from 100% plant-derived materials. Using bio-polymer (plant-derived plastic) improves moldability during processing, and it also has significant environmental benefits such as the realization of 100% plant-derived grades and biodegradability that does not cause microplastic problems. Sulapac aims to compose all its materials from plant-derived or recycled materials only by 2025.
Why Sulapac Chooses “Plant-Derived” Materials
Conventional plastics like polyethylene (PE) and polypropylene (PP) are made from non-renewable resources, namely petroleum. There are mainly two reasons why the reduction of petroleum-based plastic usage is being called for worldwide.
The first reason is that petroleum-based raw materials (fossil fuels) emit a lot of carbon dioxide from the manufacturing process to disposal, which can potentially accelerate climate change.
The second reason is the risk of depletion of petroleum-based raw materials (fossil fuels) themselves in order to continue meeting the increasing demand.
So, does the use of plant-derived raw materials not emit carbon dioxide in the manufacturing process? That’s not the case. Like petroleum-based materials, carbon dioxide is emitted, but plants absorb carbon dioxide from the atmosphere through photosynthesis as they grow. In this sense, the number of emissions can be offset by the amount of absorption. In addition, plant-derived raw materials can regenerate in a much shorter period compared to petroleum-based materials. Generally, wood regenerates in several decades to centuries, while petroleum is formed over millions of years deep within the Earth.
Based on the above, Sulapac chooses plant-derived raw materials, which have less environmental impact, rather than petroleum-based raw materials that are depleting resources.
Disposal and Recycling
In terms of disposal, the general recycling system is designed for conventional petroleum-based plastics, so it is not suitable for recycling plant-based materials or materials with biodegradability. However, some systems can recycle these materials. As plant-derived materials become more widespread in the future, these recycling systems are expected to improve. Currently, Sulapac recommends disposal through industrial composting, but depending on the grade, mechanical recycling is possible up to a maximum of 5 times. They are also developing towards compatibility with chemical recycling in the future.
Achieving Sustainable Procurement
Regardless of whether the material is petroleum-based or plant-based, it is important to procure materials with consideration for the environment. For example, simply procuring wood from a nature reserve does not make it a renewable material. The wood chips used in Sulapac® are sourced from properly managed forests in Northern Europe to maintain forest resources, and many of them use waste generated during the processing of timber.
Biodegradation and Microplastics
Biodegradation refers to the biological process in which microorganisms present in nature break down materials into water, carbon dioxide, and organic matter. Polymers with biodegradability exist in both plant-derived and petroleum-derived forms, but many conventional plastics are non-biodegradable polymers.
Non-biodegradable plastics, once they leak into the natural environment, are said to take hundreds of years to decompose. Microplastics and nano plastics, which are created by degradation due to ultraviolet rays or erosion by water flow, do not biodegrade by microorganisms and continue to drift in the natural environment for a long time, raising concerns about their negative impact on ecosystems.
Even plant-based plastics can have the same molecular structure as petroleum-based plastics, so it is important to note that not all materials named “bioplastics” necessarily have biodegradability.
Summary
- Sulapac achieves “sustainability,” “beauty,” and “functionality”
- Up to 100% plant-derived material
- Uses wood and waste collected from certified forests
- Can be disposed of through industrial composting
- Can be mechanically recycled up to a maximum of 5 times
- Biodegradable, so it does not leave behind microplastics
Our company has formed a strategic partnership with Sulapac on a global scale, and we produce and sell various molded products through our molding factory. If you are interested in [sulapac], a plant-derived biodegradable material, please contact us here.