The characteristics of this case are as follows.
- In-mold decoration : molding and design printing
- Clear plastic molding for display
- Formation of sealing components by urethane elastomer (TPU) molding
- Plastic molding parts assembly by ultrasound heating
IMD (In-Mold Decoration) / molding and design printing
IMD (In-Mold Decoration) is a technique where a design printed transfer foil film is loaded into a mold, and the design is transferred onto the surface of the molded product during injection molding.
The transfer foil is produced by multi-color printing using gravure printing. Compared to the method of screen printing designs on the surface of the molded product, IMD allows for a much wider range of artistic designs.
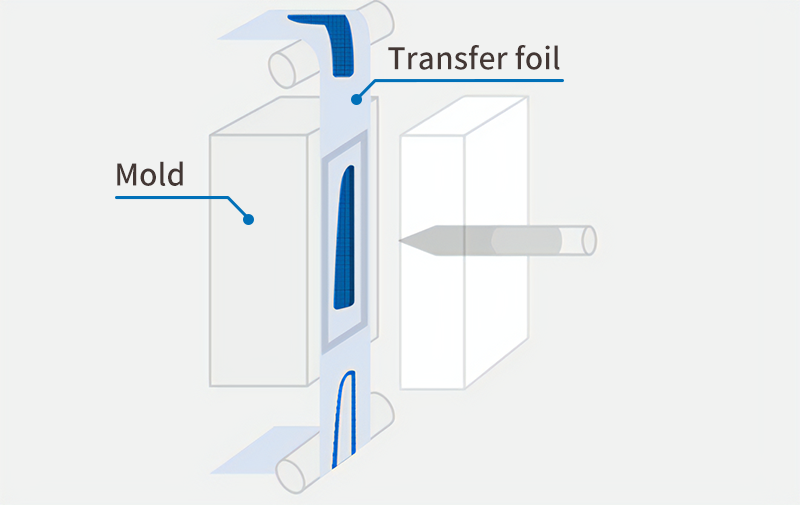
In the case of CPAP cover, a black monochrome frame pattern was formed using a transfer foil. By printing the frame on the surface of the molded product, a seamless shape without any steps can be achieved. As a result, it has become possible to provide a hygienic product without dust accumulating in the steps.
In this example, only a single-color frame pattern is transferred. However, it is also possible to form a print pattern considering usability, such as printing text where buttons are incorporated, or changing the color in places where attention needs to be drawn.
Nissha has a wealth of experience in IMD (In-Mold Decoration). We also have an in-house design department, and we are prepared to propose original designs that reflect our customers' voices.
Clear plastic molding for display
In IMD (In-Mold Decoration), by combining transparent resin molding and decorative transfer, it is possible to manufacture the window frame parts of the display in one process. In other words, you can manufacture the display panel with a simpler process than two-shot molding.
Furthermore, since a hard coating layer is provided on the surface of the transfer foil, it is possible to provide a display panel that has excellent scratch resistance for touch input.
Furthermore, the transparent window part is manufactured considering optical properties. Optical specifications required as characteristics of the display, such as welds and retardation, are quality-checked at the design and manufacturing stages to meet the customer's requirements.
Formation of sealing components by urethane elastomer (TPU) molding
The CPAP cover required a sealing component at the mating part with the main body. This sealing component is a part to deal with dustproof and waterproofing of the main body of the equipment. This sealing component used urethane elastomer (TPU). The sealing component and the back component are formed in one process using a two-shot injection molding.
Sealing component: urethane elastomer (TPU)
Back component: thermoplastic
Plastic molding parts assembly by ultrasound heating
The display panel and the back component with the sealing part are molded separately, joined by ultrasonic welding, and assembled as a display panel for CPAP.
Contract manufacturing supplier of plastic parts for medical devices
At Nissha, we accept consultations for contract manufacturing of plastic parts for medical devices.
We have a support system in place for all phases, from design considerations and prototype requests to mass production consultations.
If you have any inquiries about the planning, development, and manufacturing of medical devices, please do not hesitate to contact us.
製造拠点Production sites
アジアAsia
成形工場Molding site
- 中国・昆山(Kunshan)Kunshan, China
- 中国・広州(Guangzhou)Guangzhou, China
- マレーシアMalaysia
印刷工場Printing site
- 日本・甲賀Koka, Japan
北米North America
成形工場Molding site
- ミシガン州・VicksburgVicksburg (MI), USA
- メキシコ・San Luis PotosiSan Luis Potosi, Mexico