- Focus resources on research and development!
- Build a globally competitive manufacturing system!
- Review the supply chain for stable supply!
We offer contract manufacturing services for a wide range of medical devices, including single-use (disposable) devices, absorbable and non-absorbable products made from biocompatible materials, catheters, tubes, endoscopic instruments, and surgical tools.
Our clean manufacturing environment allows us to handle high-risk medical devices.
We are also capable of meeting international regulations such as FDA requirements, enabling us to establish a global manufacturing system. Whether you need to transfer or expand existing production lines or outsource the manufacturing of new products, please consult with us.
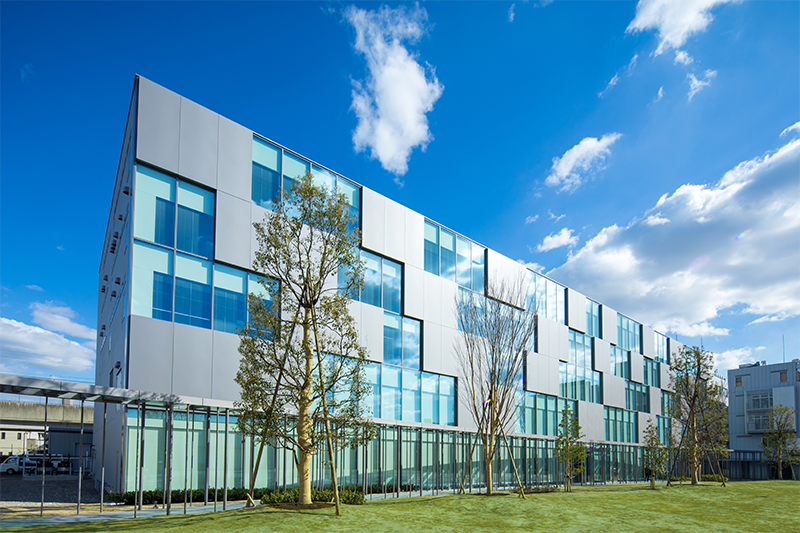
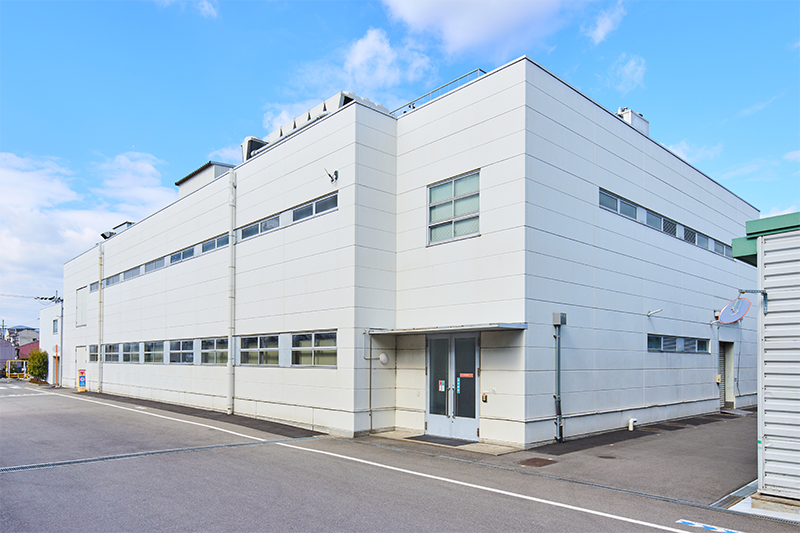
One-Stop Manufacturing Management Centered at Global Headquarters in Kyoto
Our Global Headquarters in Kyoto houses both an Innovation Center and a manufacturing factory, enabling seamless production from engineering to manufacturing.
Even for global manufacturing, we manage production by collaborating with our global sites, ensuring peace of mind.
We contribute to the evolution and advancement of medical devices through our "Made in Kyoto" craftsmanship and Nissha Medical Technologies' global network.
- Production line transfer
- Construction and operation of manufacturing processes
- Manufacturing, final devices/component assembly, packaging, sterilization
Equipped with Class 10,000 Clean Rooms
We have established a management system for clean rooms that comply with QMS regulations (Quality Management System), which set the standards for manufacturing and quality control of medical devices.
Based on ISO13485 and QMS regulations, our clean rooms meet Class 10,000 standards.
Experts in clean room manufacturing support the entire production process, from manufacturing to assembly, inspection, packaging, sterilization (outsourced), and shipping. We also offer packaging services from primary packaging before sterilization to coordination with sterilization vendors, shipping, storage, and shipping to end users.
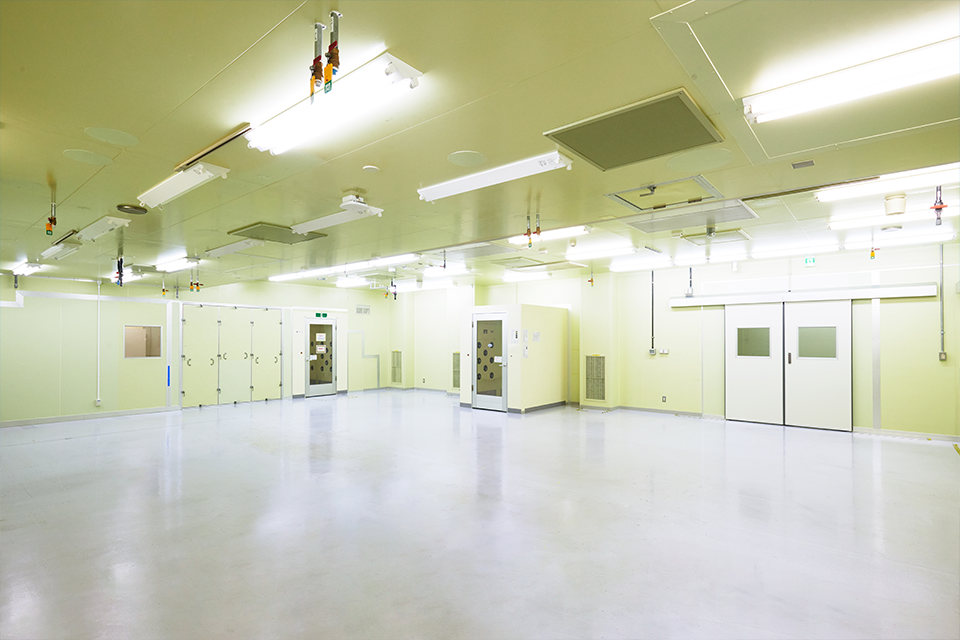
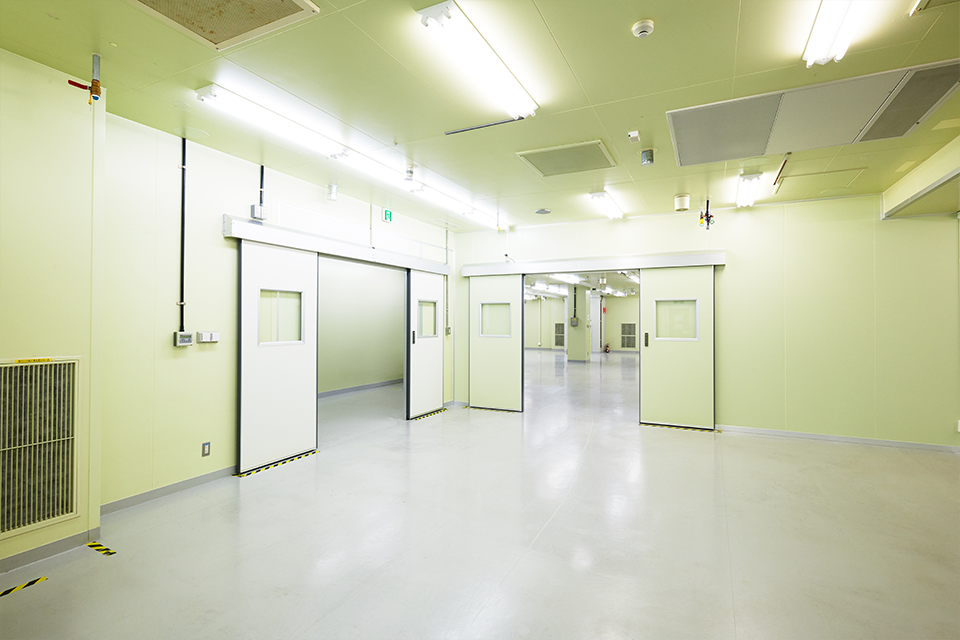
Global Medical Device Manufacturing System and
Compliance with International Regulations
If you are considering contract manufacturing of medical devices for overseas markets, including the United States, please consult Nissha.
We have 14 manufacturing sites worldwide, all of which are ISO13485:2016 certified. For the US market, in particular, we have a factory in the Dominican Republic, providing internationally competitive mass production in terms of both quality and cost, with a total manufacturing space of 23,000 square meters and a workforce of over 400 personnel.
Comprehensive Manufacturing and Packaging Services
We offer comprehensive contract services from manufacturing to shipping. We can handle the arrangement of radiation-resistant and sterilization packaging materials specified by customers, containers, and bags, as well as requests to sterilization vendors for primary packaging before sterilization. Assembly and packaging can be done in kits or combination packaging. We streamline the manufacturing process of medical devices while ensuring quality.
Providing comprehensive contract services from manufacturing to shipping!
Comprehensive Manufacturing and Packaging Services
In various industries, including IT and mobility, we have supplied high-value-added products with advanced processing technology. Supporting Nissha's manufacturing are the “Six Core Technologies.”
By combining these technologies with our extensive knowledge of various materials, we solve customer problems and achieve high-performance, high-quality products.
-
Printing
-
Coating
-
Laminating
-
Molding
-
Patterning
-
Metal processing
Medical device
manufacturing site
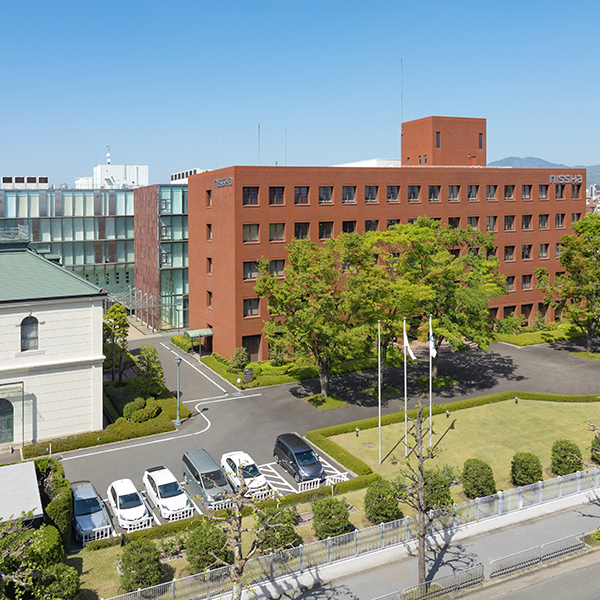
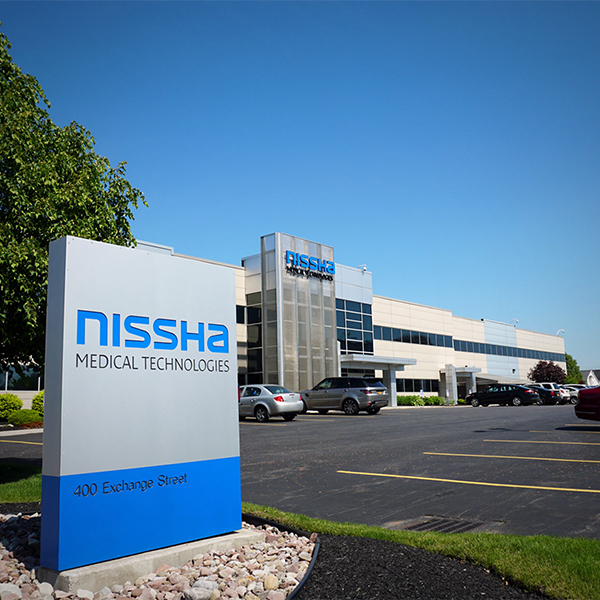
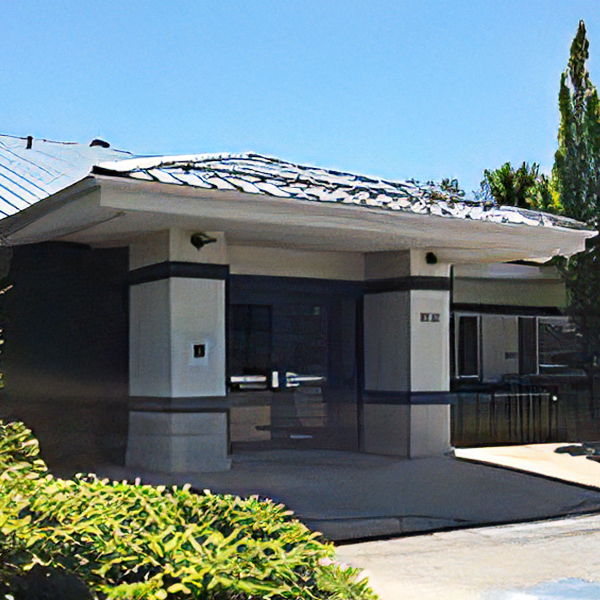
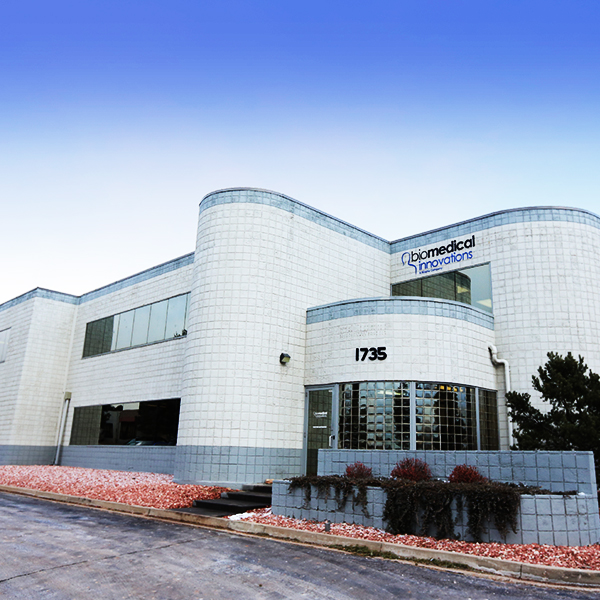
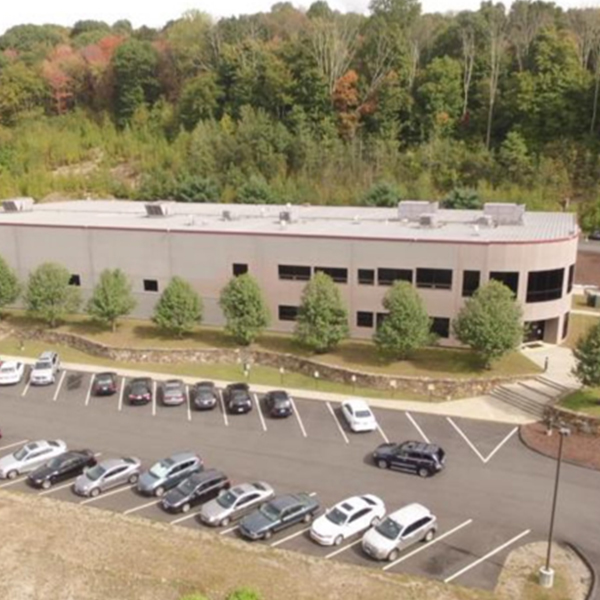
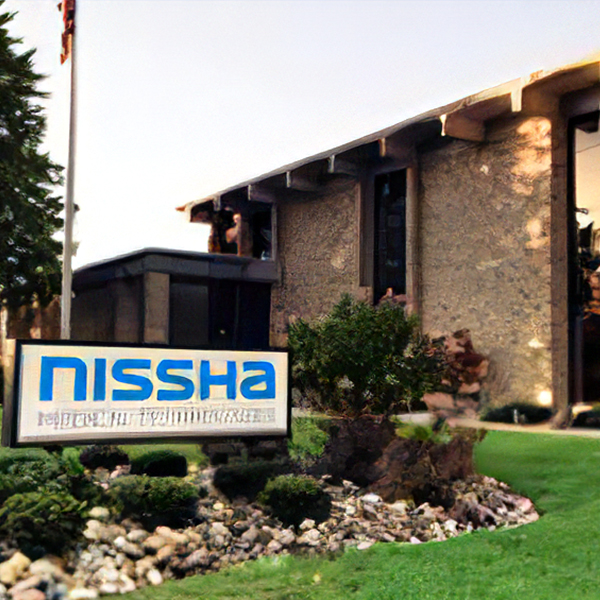
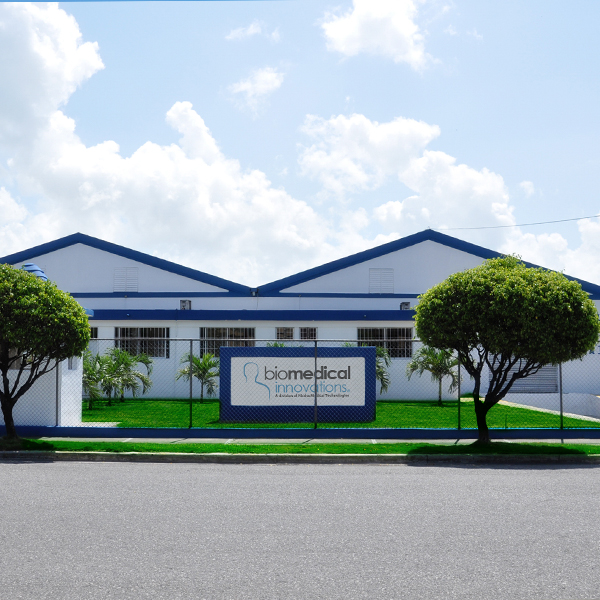
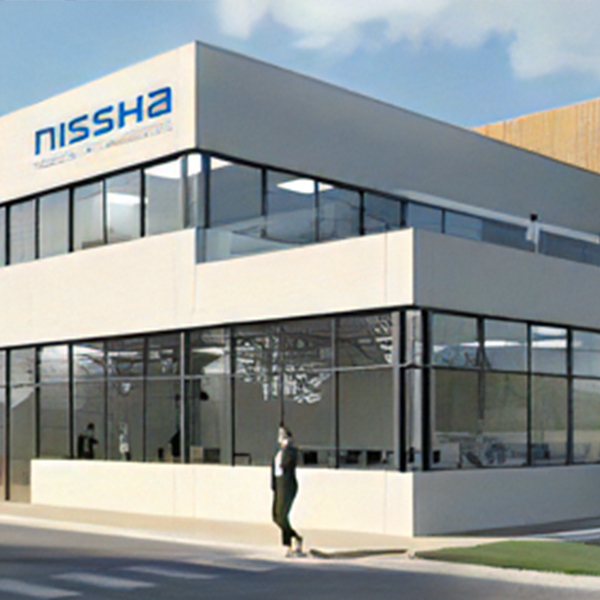
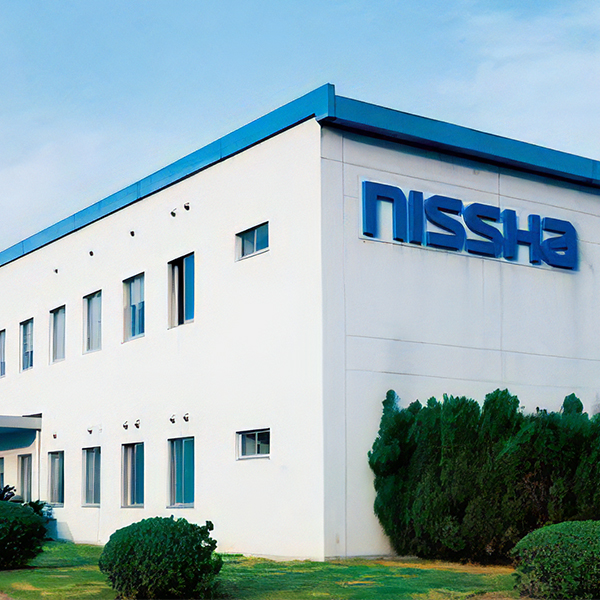
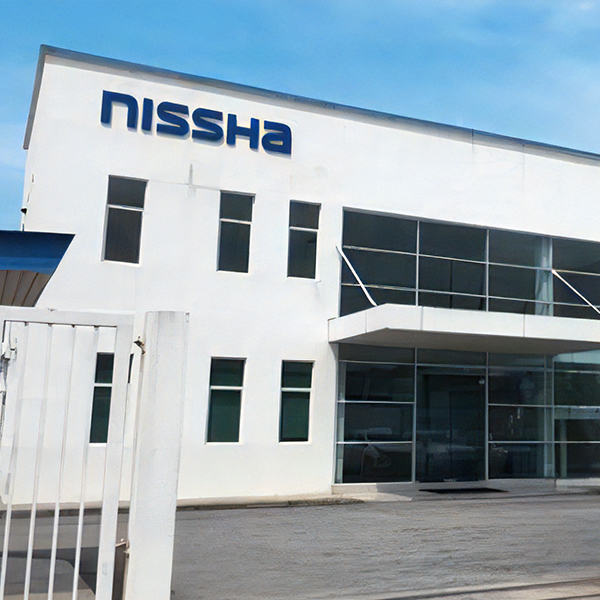
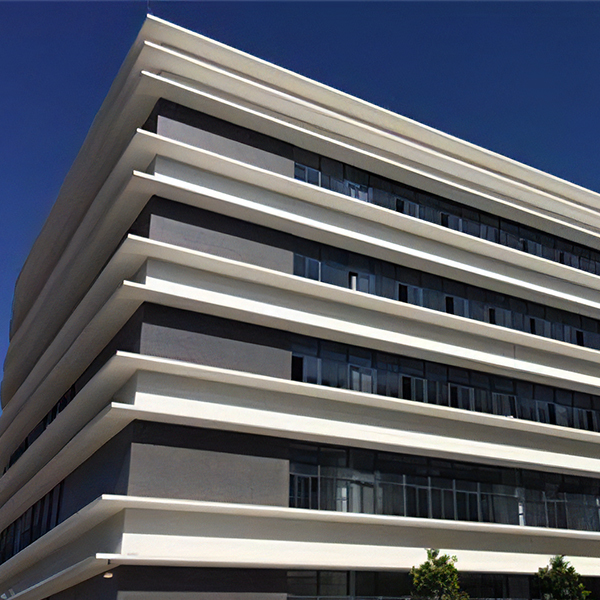
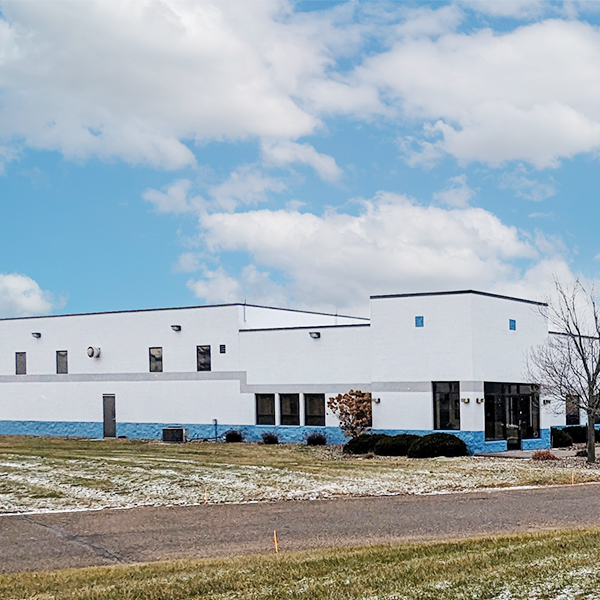
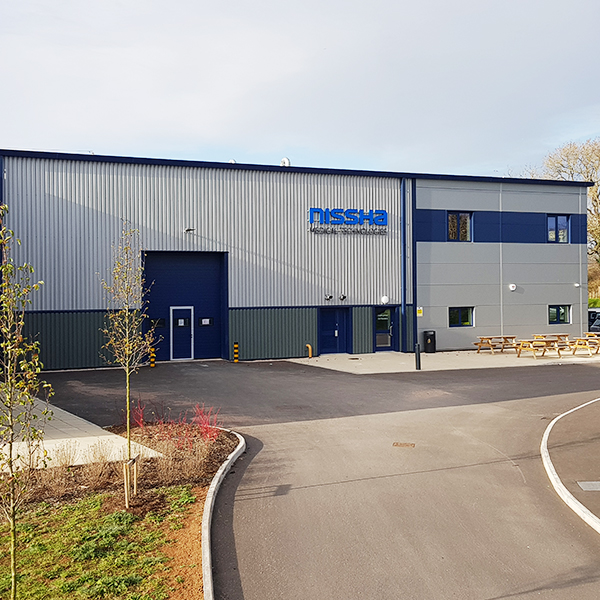
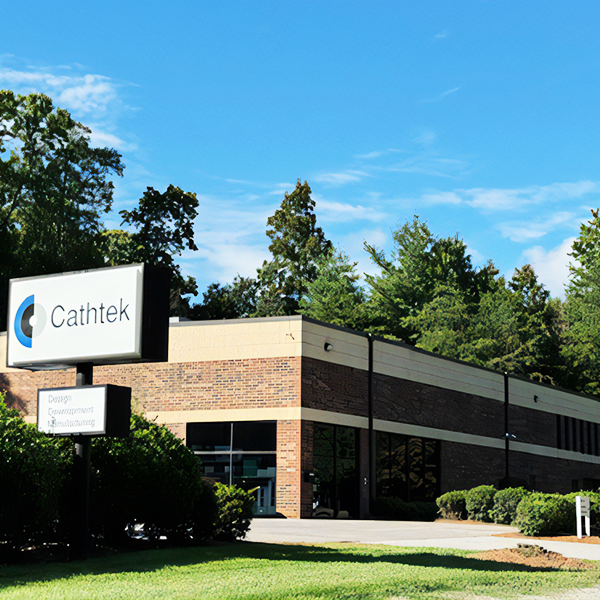