- If a product design has been completed but the manufacturing capability is still needed, then additional resources must be allocated.
- If the production volume is increasing but it's difficult to scale up internally, then external support may be required.
- If the ways to produce devices without compromising quality are needed but there is a lack of manufacturing expertise and know-how for more efficient production.
NISSHA's CDMO services address these challenges, supporting you from prototyping to mass production, and helping you establish a high-quality manufacturing system. We excel in manufacturing products that require stringent clean environment management, and can support in the mass production of various medical devices across all classes.
NISSHA's CDMO Service Offerings
We offer a comprehensive range of services from development prototyping and the production of non-clinical and clinical prototypes to full-scale mass production. Based on your product specifications, we design the optimal manufacturing process and provide support at every stage from prototyping to mass production.
-
- Infrastructure Development
- We support the evaluation and establishment of the manufacturing environment and equipment necessary for mass production. We install the required manufacturing infrastructure and build the optimal production line.
-
- Pilot Line Setup
- We establish a pilot line for the initial production phase of new products. By manufacturing prototypes, we conduct design verification and validation, identifying issues to be addressed for mass production.
-
- QMS System Establishment
- We build a Quality Management System (QMS) compliant with ISO 13485 to ensure thorough quality control. According to your manufacturing specifications, we prepare quality documents such as manufacturing procedure manuals, inspection criteria, and traceability management tables to ensure transparency and consistency in quality management.
-
- Mass Production Line Construction
- We optimize the layout of the production line to enhance production efficiency and safety, reducing the burden on workers and improving production speed.
-
- Process Validation
- We conduct validation at each manufacturing stage, ensuring stable quality through Installation Qualification (IQ), Operational Qualification (OQ), and Performance Qualification (PQ).
-
- Mass Production Launch
- Based on feedback obtained from the pilot line, we achieve a smooth transition to mass production through detailed planning and precise management. Leveraging our extensive expertise in processing technology, we extract and standardize manufacturing know-how to establish highly reproducible manufacturing processes, enhancing product quality and production efficiency.
Prototyping and Mass Production
in a Class 10,000 Clean Room
We own clean rooms in Kyoto, Japan, compliant with ISO 13485 and QMS regulations, meeting cleanliness class 10,000 standards. Products in the development phase can be prototyped in a clean test line based on ISO 13485 and QMS regulations. The test line can be adjusted to meet your desired cleanliness level by installing clean booths, so please consult with us for your specific needs.
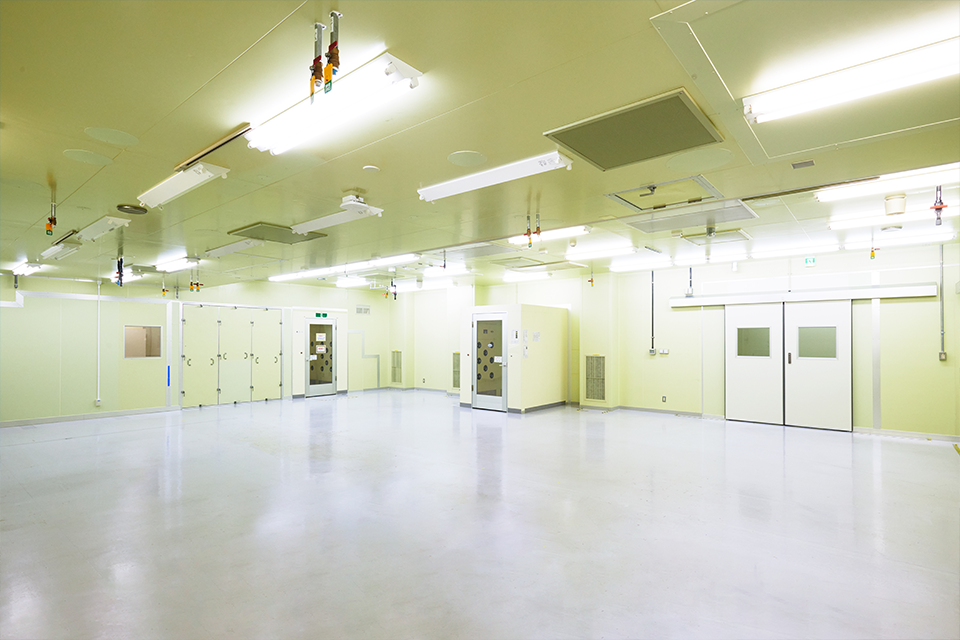
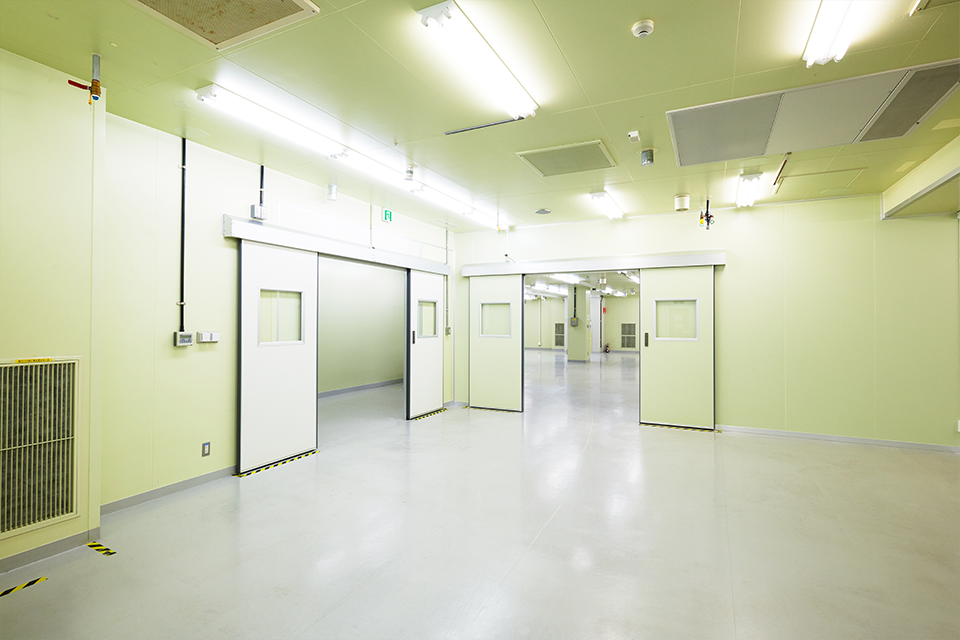
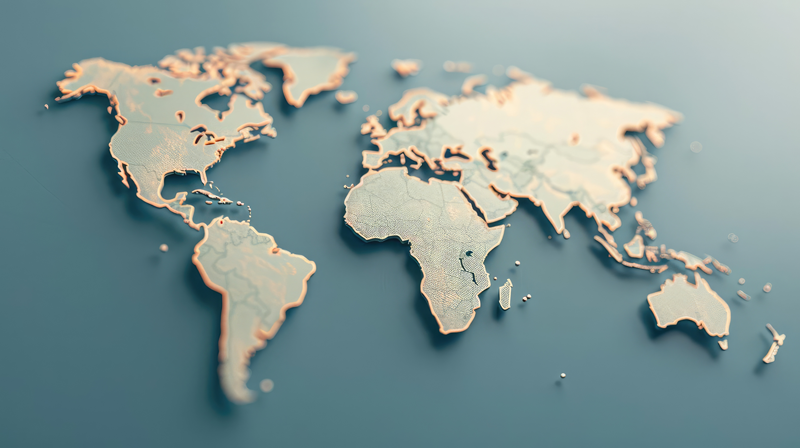
Support for Manufacturing Medical Devices for Overseas Markets
For medical devices requiring overseas shipment, we can support compliance to international regulations such as FDA requirements. We support document preparation and audits to meet FDA regulatory requirements as a manufacturer. NISSHA owns multiple factories, including overseas locations, certified with ISO 13485, the international standard for quality management systems specialized in medical devices, enabling us to propose overseas manufacturing solutions.
NISSHA offers comprehensive contract services from development prototyping and manufacturing of samples for non-clinical and clinical trials to mass production. Please feel free to contact us for any inquiries regarding the development prototyping and manufacturing of medical devices.