Nissha IMD and IML, Simultaneous injection-decoration technologies, are the decoration technologies that transfer a printed layer or insert a multi-colored film on the surface of the molded parts. The components manufactured with IMD, IML are created as cover parts with an aesthetically pleasing appearance as follows.
- Graphic design for the superior appearance of medical devices
Nissha IMD and IML, Simultaneous injection-decoration technologies, are the decoration technologies that transfer a printed layer or insert a multi-colored film on the surface of the molded parts. The components manufactured with IMD, IML are created as cover parts with an aesthetically pleasing appearance as follows.
What are IMD and IML ?
IMD and IML of Nissha are technologies to insert a decorative film in a die and
decorate the surface of a molded part at the same time as injection molding.
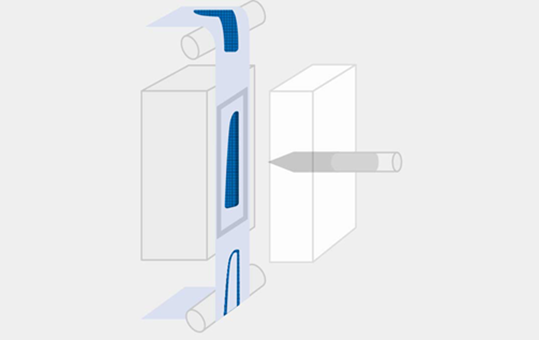
-
IMD(In-mold Decoration)
IMD is a technology that transfers only the printed layer on decorative film to the surface of molded part.
This technology can implement molding and decoration in the same process. -
IML(In-mold Labeling)
IML is a technology to insert a decorated film on the surface of a molded part.
This technology can also insert a film over a molded part with a deep shape.
- *IMD and IML are registered trademarks of NISSHA Co., Ltd.
- *IMD is the abbreviation of “In-mold Decoration.” This is a term of our company that was named from the technology of simultaneous decoration and molding using transfer foil in a die of injection molding. IML is an abbreviation of “In-mold Labeling.”
-
-
- Resin type
- PS, PP, ABS, acrylic, PC, etc.
General thermoplastic resins are acceptable.
We ask customers to request resin materials and examine the optimal processing conditions.
-
-
-
- Vacuum molding of film
- In addition to injection molding, it can also be applied to vacuum molding of plastic films.
We have experience with vacuum molding of plastic films such as acrylic, ABS, and PP.
-
Graphic design is important also for medical settings
The cover panels of medical devices are generally simple. Resins with a single color, such as white, are molded, and most of the switches and product logos are printed in a single color such as black and blue. We believe that more versatile graphical designs are important for the cover panels of medical devices for the following two reasons.
To prevent erroneous operations and improve safety
In single color printing, all operation buttons are in the same color. It is therefore difficult to differentiate between the buttons, and the wrong button may be pressed. For example, what if the buttons are color-coded by function? Multi-colored printed panels possibly enhance operational safety.
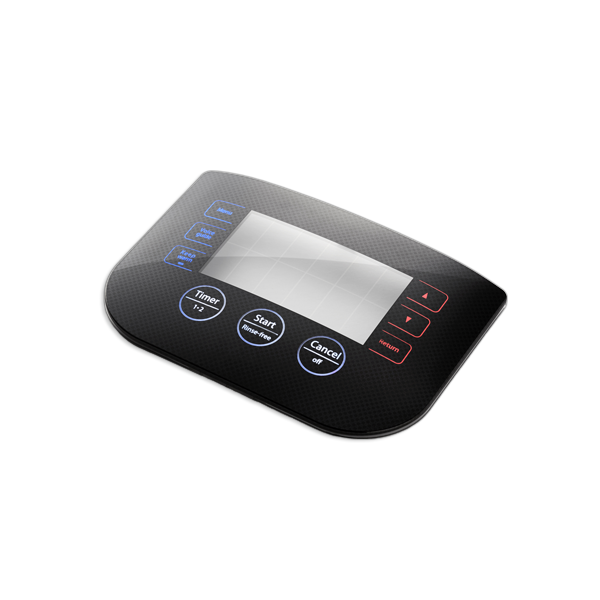
To brighten the medical setting
Hospitals are also residential spaces for healthcare workers and patients who are staying there for a long period. Such people may feel psychological stress if they are in residential spaces with boring machines. Recently, efforts are being made to brighten hospitals by adding certain designs, e.g., infusion stands with animal motifs, CT room ceilings with the picture of a blue sky painted across it. We believe that our IMD and IML technologies that provide medical devices with graphical designs contribute to brighten the medical setting.
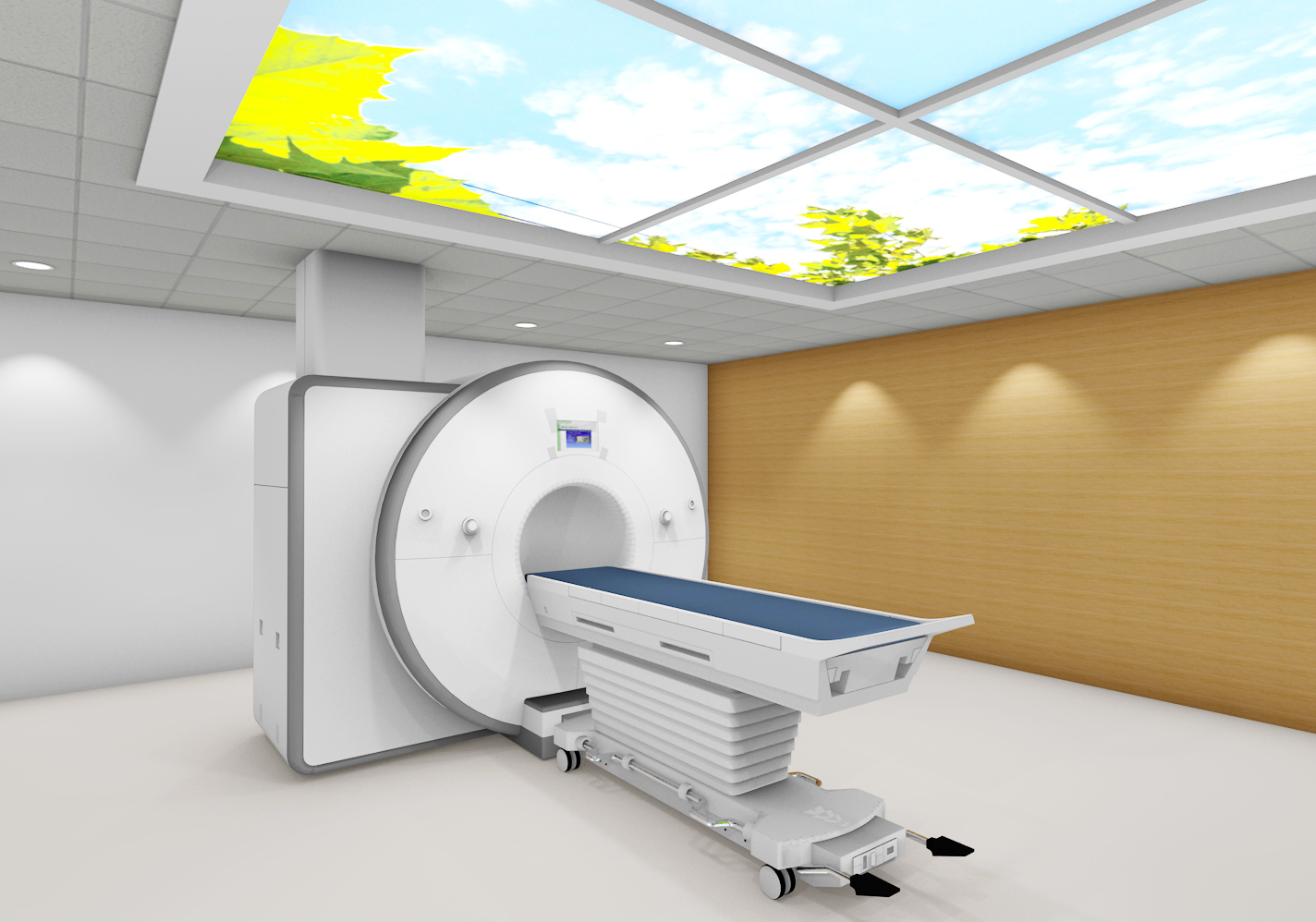
Examples
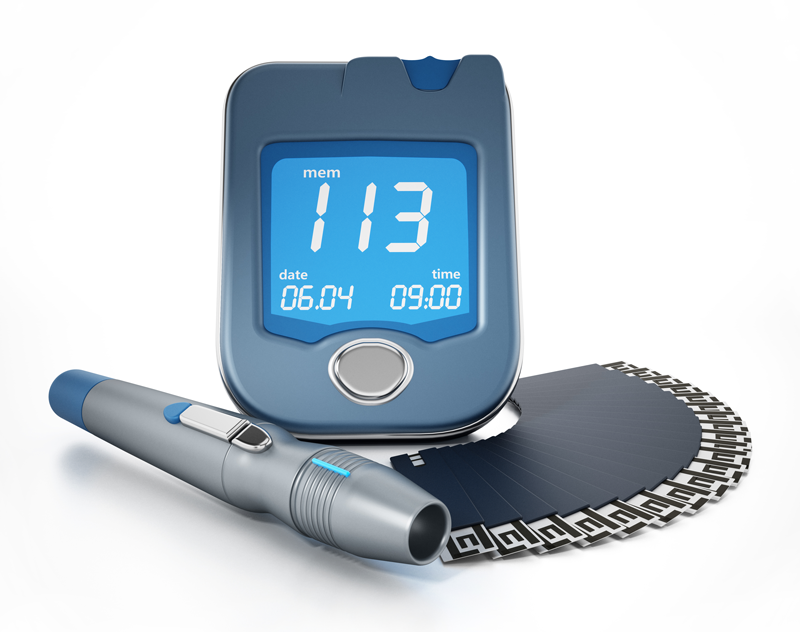
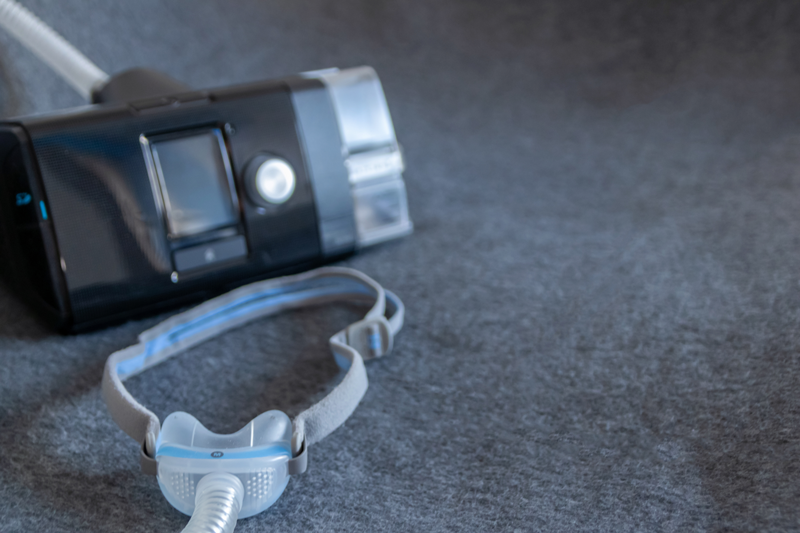
Feel free to ask us about medical injection molding.