マイクロ成形とは、通常の製品に比べて極めて小さな部品を精密に成形する技術で、主に射出成形が利用されます。医療機器や電子機器などの分野で活用されており、小型部品でも高精度かつ安定した品質で大量生産できる点が特徴です。 この記事では、マイクロ成形の仕組みや特徴、具体的な活用分野、課題について詳しく解説します。
マイクロ成形とは?
マイクロ成形とは、通常の製品よりも非常に小さな部品を成形するための技術です。主に射出成形によって行われ、精密で一貫した品質を持つ小型プラスチック部品を効率的に大量生産できるのが特徴です。
マイクロ成形は一般的なプラスチック射出成形のプロセスを小型化した技術ですが、成形金型の精度や温度管理、材料特性など、マイクロ成形に特化したパラメーターが必要となります。そのため、一般的な成形では実現が難しい1g以下の小さな部品でも高精度に成形できます。
こうした特性から、医療分野や電子部品など、精度が求められるさまざまな産業においてマイクロ成形は重要な役割を果たしています。
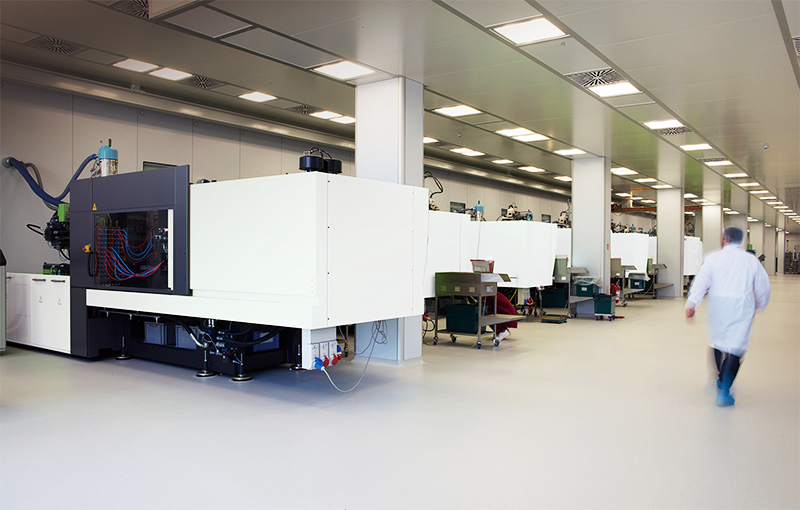
射出成形の仕組み
射出成形は、プラスチック製品を加工する際に用いられる成形方法です。主に熱可塑性樹脂と呼ばれる樹脂を使用します。射出成形機で 加熱・溶融した樹脂を、高い圧力で閉じた金型に射出し、冷却・固化する工程で製品を作ります。基本的には「樹脂を溶かす」「金型に流し込む」「圧力をかけて固める」の3つの工程で成形が行われます。
-
- 樹脂を溶かす
- プラスチック射出成形機の材料を投入するホッパーは、漏斗(ろうと)のような形状をしています。このホッパーに直径3mm程度の球状や円柱状のペレット状の樹脂を供給します。樹脂は円筒状のシリンダーに送られ、シリンダー内部のヒーターとスクリューによって加熱・圧縮しながら混錬します。この過程で樹脂は溶けて、シリンダーの先端部分に蓄えられます。
-
- 金型に流し込む
- シリンダー先端のノズルを金型に密着させ、高圧で樹脂を注入する工程です。このとき、金型を高い圧力で締めつけることで、射出した樹脂が漏れずに流し込めます。樹脂は金型内で冷却され、次第に固化します。冷却時間は製品の厚みや形状によって異なりますが、マイクロ成形では極めて短い時間で済みます。
-
- 圧力をかける
- 射出後は保圧と呼ばれる圧力をかけ続け、金型内の隙間をしっかりと埋めます。冷却に伴う樹脂の収縮で成形品の表面が凹む「ヒケ」を防ぎ、均一で美しい仕上がりを実現するために欠かせない工程です。樹脂が硬化したら金型を開き、成形された製品を取り出します。
- 射出成形は短時間で高品質な製品を大量に作れる方法です。複雑な形状の製品や薄いものでも効率よく成形できるため、プラスチック製品の生産で広く用いられています。
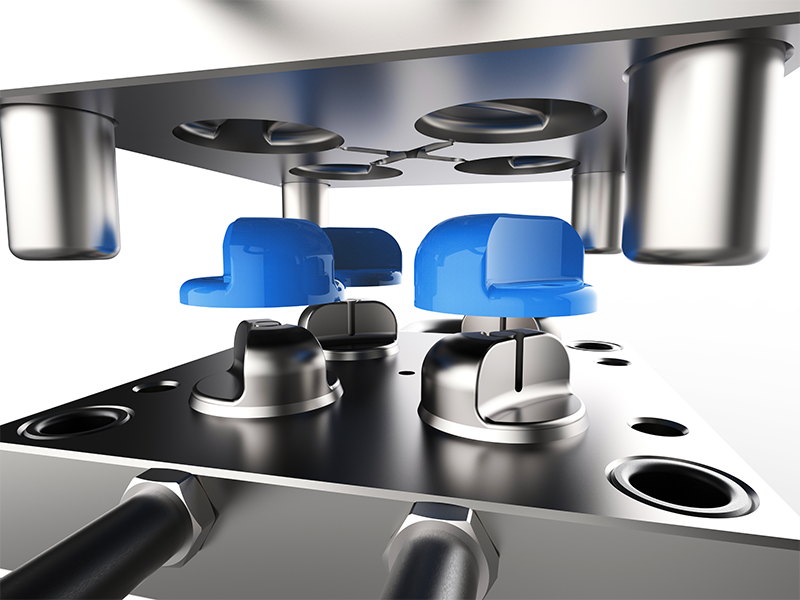
マイクロ射出成形の特徴
マイクロ射出成形は、非常に高い精度で微細プラスチック成形品を製造できる上、大量生産において費用対効果が高い成形方法です。また、多様な材料に対応でき、特に医療機器や電子機器など、精密さが求められる分野において、高く評価されている技術です。以下では、マイクロ射出成形の主な特徴3つを紹介します。
精度が高い
マイクロ射出成形の最大の特徴は、非常に高い精度を実現できる点です。通常の射出成形では困難な小さい部品でも、細かな形状や複雑なデザインを再現できる上、製造時の公差(誤差許容範囲)も厳格に管理されます。
また、CNC(コンピュータ数値制御)やEDM(放電加工)といった高度な加工技術の駆使により、射出成形部品のサイズや形状を一定に保てます。わずかな誤差が製品性能に大きく影響を与える精密部品の製造において、この高精度な成形は不可欠です。そのため、医療や電子、マイクロ光学などの分野での需要が増加しています。
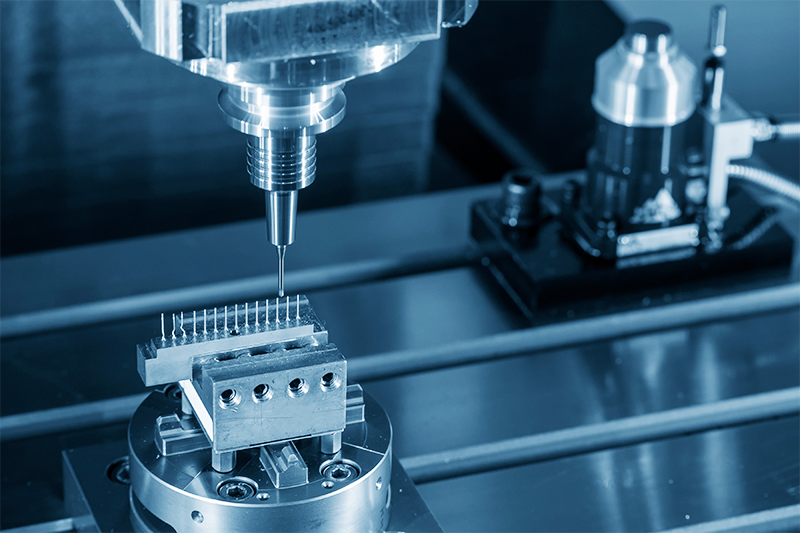
費用対効果が高い
マイクロ射出成形は、コスト効率にも優れています。成形に使用する機器や金型が小型であるため、射出成形機のコストやスペースを効率的に使用することができ、結果的に生産コストの抑制が可能です。さらに、小さな部品は材料消費量が少なく済み、無駄も減るため、材料コストも削減できます。この効率性は、製品のサイズが小さいほど大きな効果を発揮します。
また、アルミニウム製金型の使用で生産速度も短縮され、サイクルタイムが短くなるのも特徴です。自動化機能の活用により生産性とコスト効率の向上を図れるので、特に大量生産体制を整えたい企業にとってコストパフォーマンスに優れた製造方法と言えます。
材料に互換性がある
マイクロ射出成形は、使用する材料に柔軟性がある点も特徴のひとつです。高性能ポリマーや生体適合性を持つ材料など、さまざまな特性を持つ素材に対応できるため、製品の用途に応じた最適な部品を製造できます。
たとえば、医療分野では生体適合性のある部品、電子部品では耐熱性や導電性を持つ部品など、材料の選択によって製品に持たせる機能の変化・調整が可能です。材料選択の多様性により、マイクロ射出成形は幅広い用途に適応できる製造技術として、多くの産業から注目されています。
マイクロ射出成形の製品が活躍する分野
マイクロ射出成形は、精密なマイクロ部品を必要とする分野で多くの注目を集めています。代表的なのが、高精度で複雑な形状が求められる医療・電子・自動車産業です。以下では、マイクロ射出成形の製品が活躍する分野を4つ解説します。
治療分野
治療分野では、マイクロ射出成形が低侵襲医療機器の製造に活用されています。極小の医療機器を体内に挿入する脳神経外科や心臓血管外科では、マイクロ射出成形加工による微細な部品が欠かせません。
たとえば、薬剤を直接患部に届けるドラッグデリバリーデバイスや、血管内で治療を行うカテーテル部品などです。小型で高精度な部品によって治療分野において安全性と精度の両方を向上させられるので、患者さまへの負担軽減にも貢献しています。
診断分野
診断分野でも、マイクロ射出成形技術が使われています。たとえば、内視鏡に搭載される小型カメラや試薬を流すマイクロ流体システムなど、診断装置の小型化と高機能化を支えるのがマイクロ成形技術です。
いずれの部品も小さな誤差が診断の精度に影響を及ぼすため、耐久性と精度を兼ね備えた部品成形が求められています。迅速で正確な診断をサポートする重要な役割を果たすのが、マイクロ射出成形です。
電子工業分野
電子工業分野では、製品の小型化・高機能化に伴い、マイクロ射出成形加工製品が幅広く用いられています。スマートフォンやコンピュータ、音響機器などで必要なコネクタやスイッチ、マイクロチップのカバーなどがその例です。
特に、マイクロ光学機器においては、高精度なレンズやプリズムを小型化するために精密射出成形技術が欠かせません。電子部品の小型化が進む中、マイクロ射出成形は高い精度と複雑な形状の実現により、コンパクトかつ高性能な製品開発を支えています。
自動車分野
自動車分野でも、マイクロ射出成形は多くの小型部品の製造に利用されています。エンジンの小型部品やブレーキシステムのパーツ、ドアロックやクリップなどの内部構造に必要な部品が代表的です。
また、ボタンやスイッチなど、車両操作に必要な小さな電子部品にもマイクロ射出成形が用いられます。軽量でコンパクトな構造により、車両全体の省エネ性が高まることも、自動車産業でのマイクロ射出成形の利点です。
マイクロ射出成形の課題
マイクロ射出成形では、品質管理が大きな課題です。微小な成形品はわずかな異物や静電気でも製品品質に影響してしまいます。粉塵や異物混入防止対策に加え、静電気対策を講じるために、セミクリーンブースや温度湿度の安定した製造環境の整備が不可欠です。
また、成形品のサイズが非常に小さく、顕微鏡や精密重量秤を用いて細かく検査しなければなりません。品質のばらつきを抑えるため、製品の形状や精度に応じた金型の取り数の調整も大切となります。さらに、金型自体にも高精度な加工技術と精密な温度管理が求められる上、定期的な清掃やメンテナンスも必須です。微細成形部品の精度をミクロン単位で維持するには、徹底した品質管理体制が欠かせません。
射出成形技術ならNISSHAにお任せください
マイクロ射出成形は、非常に小さなプラスチック部品を高精度で製造する技術であり、医療分野でも活用されています。
NISSHAでは、射出成形技術を用いた医療機器の製造を行っています。医療機器の全製造拠点で「ISO13485:2016」を有しており、品質に対するニーズに応えられる体制が整っています。射出成形技術を用いた医療機器製造を検討している方は、ぜひ一度お問い合わせください。
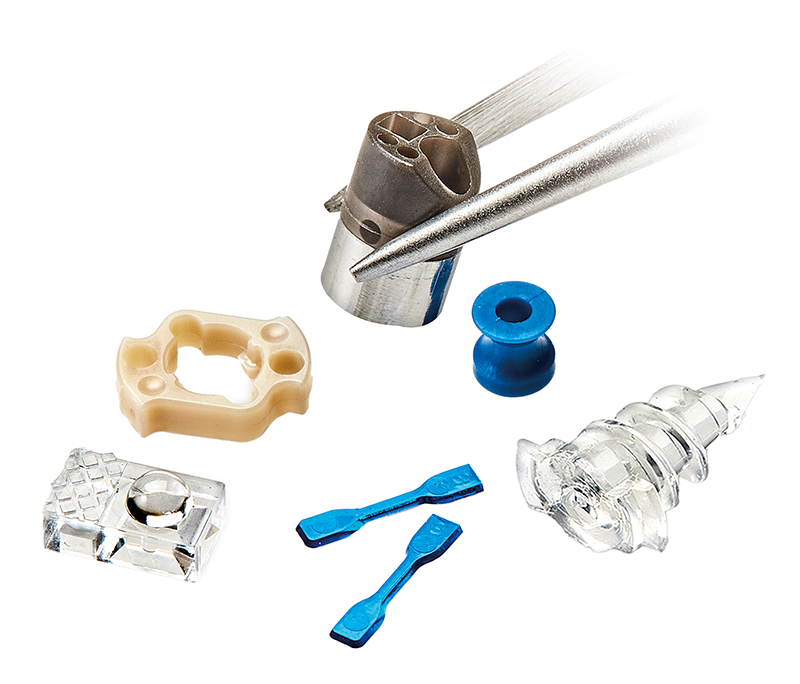